Ultrasonic Waves: The Unexpected Key to Stronger, More Sustainable Plastics?
"Revolutionizing HDPE/UHMWPE Blends for Enhanced Performance and Eco-Friendly Solutions"
Polyolefin pipes are the unsung heroes of modern infrastructure, reliably transporting water and gas across vast distances. Their lightweight nature and resistance to corrosion have made them indispensable in countless applications. Among these, high-density polyethylene (HDPE) pipes, particularly those meeting the PE-100 standard, stand out for their exceptional long-term performance and processability.
However, even with their robust properties, PE-100 pipes face limitations, especially when it comes to producing large-diameter, thick-walled structures. The molten polymer tends to sag before it can fully harden, compromising the integrity of the final product. While nucleating agents have been used to combat this issue, a more innovative approach is gaining traction: blending HDPE with ultra-high molecular weight polyethylene (UHMWPE).
UHMWPE, known for its superior strength, toughness, and resistance to wear and stress cracking, offers a promising avenue for enhancing HDPE's mechanical properties. Now, researchers are exploring the potential of ultrasonic oscillations to further optimize these HDPE/UHMWPE blends, unlocking new possibilities for stronger, more sustainable plastic materials. This article delves into the groundbreaking research that explores the effects of ultrasonic waves on the performance and crystallization behaviors of these advanced plastic blends.
How Ultrasonic Oscillations Optimize HDPE/UHMWPE Blends
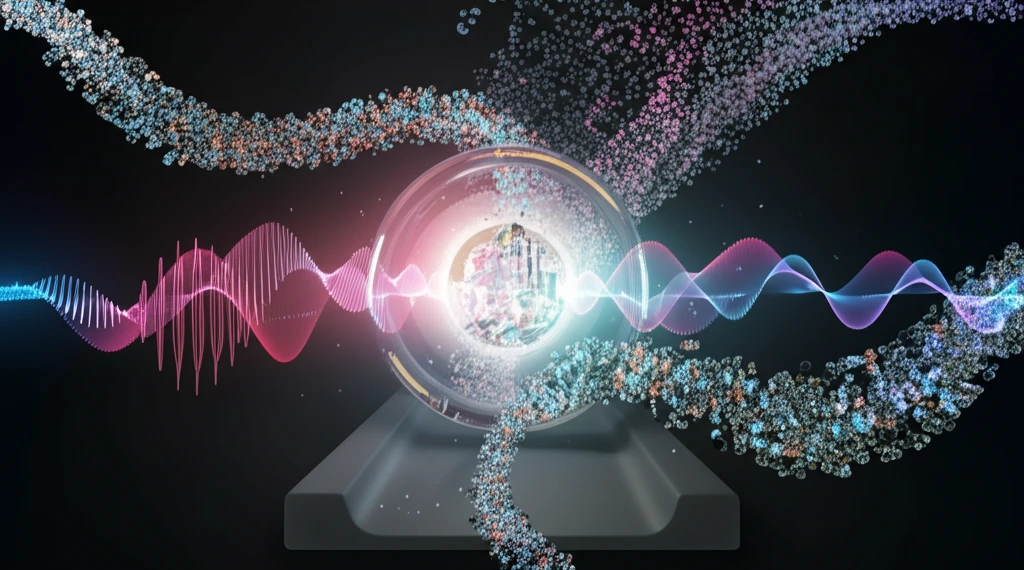
A recent study published in Materials Research Express has shed light on the remarkable benefits of using ultrasonic oscillations during the production of HDPE/UHMWPE blends. Xuefeng Pan and his team investigated how these sound waves influence the crystallization behavior, orientation, and mechanical properties of the resulting material. The researchers combined HDPE with UHMWPE in a twin-screw extruder, employing an ultrasound transmitter that vibrated at 20 kHz. By carefully analyzing the blends, they uncovered some game-changing results.
- Enhanced Dispersion: Ultrasonic treatment significantly improves the uniformity of UHMWPE within the HDPE matrix.
- Oriented Structures: Even a small amount (3 wt%) of UHMWPE, combined with ultrasound, promotes the formation of large, oriented shish-kebab structures, known for their reinforcing effect.
- Faster Crystallization: Differential scanning calorimetry (DSC) measurements showed that UHMWPE and ultrasound increase the rate at which the plastic blend crystallizes, leading to more stable and robust structures.
- Improved Nucleation: Polarized optical microscopy (POM) and X-ray diffraction (XRD) analyses confirmed that UHMWPE encourages the formation of smaller, more concentrated nuclei within the blend, contributing to its enhanced properties.
The Future of Plastics: Stronger, Greener, and Sound-Enhanced
The research by Pan and his team offers a compelling glimpse into the future of plastics manufacturing. By harnessing the power of ultrasonic oscillations, we can create HDPE/UHMWPE blends with enhanced mechanical properties, improved durability, and potentially greater sustainability. These advancements promise to benefit a wide range of industries, from infrastructure and transportation to packaging and consumer goods.