Forging the Future: How Cold Pre-Forging is Revolutionizing Magnesium Alloy Strength
"Unlock the secrets to stronger, lighter materials: Discover how cold pre-forging (CPF) is transforming the tensile properties of extruded AZ80 magnesium alloy, paving the way for innovative applications across industries."
In today's world, the demand for materials that are both strong and lightweight is constantly growing. Industries ranging from transportation to electronics are seeking innovative solutions to improve efficiency and performance. Magnesium (Mg) alloys, known for their low density, high specific strength, and excellent electromagnetic wave shielding, have emerged as promising candidates. While casting has been a traditional method for producing Mg alloy components, wrought Mg alloys, especially those that are rolled or extruded, offer superior mechanical properties, making them ideal for high-stress applications.
Extrusion, a process where a material is forced through a die to create objects with a fixed cross-sectional profile, stands out as an efficient manufacturing technique for Mg alloys. Unlike rolling, which requires multiple passes and intermediate heat treatments, extrusion can produce bars, sheets, plates, and other complex shapes in a single step. However, extruded Mg alloys have historically lagged behind aluminum (Al) alloys in terms of strength, limiting their widespread adoption. This is where the innovative approach of cold pre-forging (CPF) comes into play, offering a pathway to significantly enhance the mechanical properties of extruded Mg alloys without the high costs associated with rare earth elements or powder metallurgy.
This article explores the groundbreaking research into how CPF dramatically improves the microstructure and tensile properties of extruded AZ80 magnesium alloy. By applying CPF to the AZ80 billet before extrusion, scientists are unlocking new levels of strength and ductility. This enhancement promises to broaden the application range of Mg alloys and challenge the dominance of aluminum in lightweight material design.
The Science Behind the Strength: Cold Pre-Forging Explained
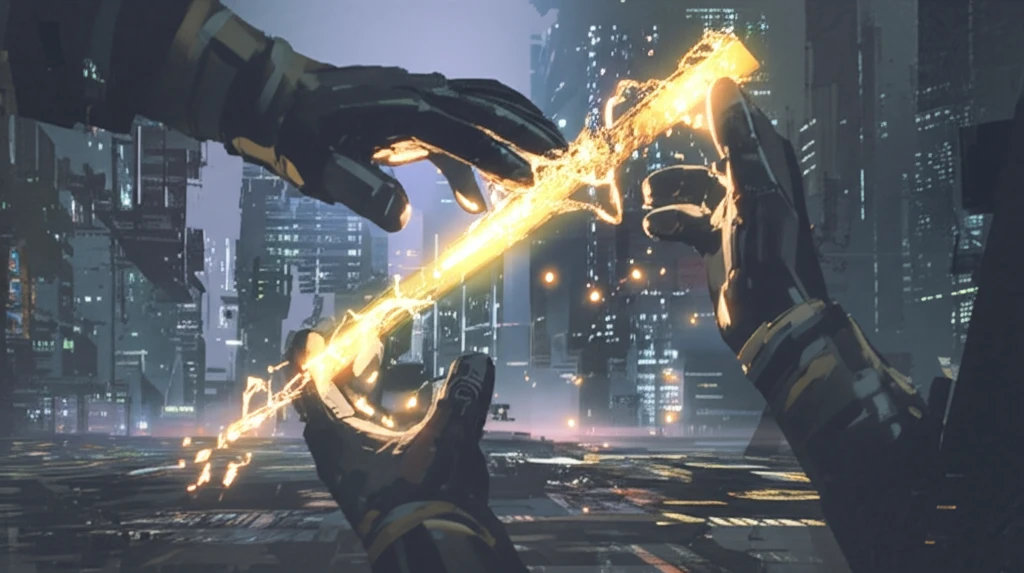
Cold pre-forging involves deforming a metal billet at room temperature before it undergoes further processing, such as extrusion. In the case of AZ80 magnesium alloy, CPF introduces a high density of deformation twins and dislocations within the material's microstructure. These twins, which are essentially mirrored regions within the crystal lattice, act as barriers to dislocation movement, a key mechanism of plastic deformation. By increasing the number of these barriers, CPF effectively strengthens the material.
- Enhanced Strength: Finer grain size due to increased recrystallization.
- Improved Ductility: Reduction in coarse, unrecrystallized grains.
- Cost-Effective: Avoids expensive rare earth elements or powder metallurgy.
- Microstructural Homogeneity: More uniform grain distribution throughout the alloy.
A Promising Future for Magnesium Alloys
The application of cold pre-forging represents a significant step forward in enhancing the mechanical properties of magnesium alloys. By providing a cost-effective and efficient method for improving both strength and ductility, CPF opens up new possibilities for the use of Mg alloys in a wide range of industries. As the demand for lightweight, high-performance materials continues to grow, innovations like CPF will play a crucial role in shaping the future of material science and engineering.