Welded Together: How Modern Techniques are Revolutionizing Pipeline Construction
"Friction vs. Fusion: Unpacking the science behind stronger, safer, and more reliable pipeline welds using residual stress evaluation"
Welding is the backbone of numerous industries, and the oil and gas sector is certainly no exception. Pipelines, the lifelines of this industry, depend on reliable welding techniques to ensure safe and efficient operations. Traditionally, gas tungsten arc welding (GTAW) has been a favored method for joining pipeline sections, known for its ability to produce high-quality welds. However, the quest for even better, more cost-effective solutions has led to the exploration of alternative techniques, with friction welding emerging as a promising contender.
Friction welding, particularly with a rotating ring, offers a unique approach to pipeline construction. Unlike traditional fusion welding, friction welding creates a bond by generating heat through mechanical friction, pressing two components together under high pressure while rotating one against the other. This solid-state process avoids melting the base materials, resulting in a weld with distinct properties and potential advantages.
A recent study has investigated and compared the residual stress states in API 5L X65 girth welded pipes joined by both friction welding and GTAW. By evaluating residual stresses, microstructural characteristics, and microhardness, the research sheds light on the strengths and weaknesses of each method. This article will explore the findings of this study, providing a comprehensive look at how these welding techniques impact the integrity and performance of pipelines.
The Science of Stress: Understanding Residual Stress in Welds
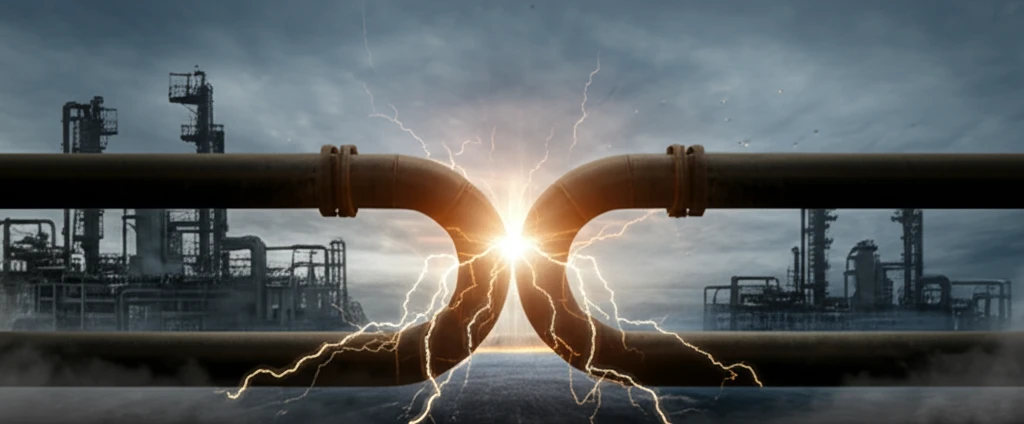
Before diving into the specifics of the study, it’s important to understand the concept of residual stress. Welding, by its very nature, involves localized heating and cooling, which can create internal stresses within the material. These residual stresses can be either tensile (pulling the material apart) or compressive (squeezing the material together).
- Residual Stress: Internal stresses remaining in a material after manufacturing processes.
- Tensile Stress: Stress that pulls material apart, often detrimental in welds.
- Compressive Stress: Stress that squeezes material together, can improve fatigue resistance.
- API 5L X65: A high-strength, low-alloy steel commonly used in pipeline construction.
Welding the Future: Innovations in Pipeline Construction
The evaluation of different welding techniques is vital for advancing pipeline construction. Friction welding shows promise in reducing residual stress and creating more homogenous welds. As technology evolves, adopting these advanced methods can lead to enhanced safety, durability, and efficiency in the oil and gas industry.