Unlocking Iron's Potential: How Temperature Transforms Iron Sand into a Valuable Resource
"Discover the groundbreaking process of turning iron sand into titanomagnetite through temperature-controlled reduction, paving the way for sustainable material sourcing and advanced applications."
Iron sand, abundant along Indonesian coastlines, is more than just ordinary sediment. It's a treasure trove of valuable minerals like hematite, magnetite, ilmenite, and rutile. These minerals, particularly titanium-bearing ones, hold immense potential due to their exceptional properties, including high melting points and corrosion resistance. Recognizing this potential, researchers have been exploring efficient methods to extract and transform these minerals for various high-tech applications.
Traditional methods of extracting iron from iron sand often involve high-temperature processes, which can be energy-intensive and costly. In response, innovative research is focusing on reducing the required temperatures while still achieving high-quality mineral transformations. One promising approach involves using coal as a reducing agent and sodium sulphate as an additive to facilitate the formation of specific iron compounds, like titanomagnetite, at lower temperatures.
This article delves into a fascinating study that investigates the impact of temperature on the formation of titanomagnetite (Fe2TiO4-Fe3O4) from iron sand. By carefully controlling the temperature during the reduction process with coal and sodium sulphate, scientists have identified the optimal conditions for maximizing titanomagnetite yield. This research not only offers a more energy-efficient extraction method but also unlocks new possibilities for utilizing iron sand in advanced materials and industrial applications.
The Key Role of Temperature in Titanomagnetite Formation
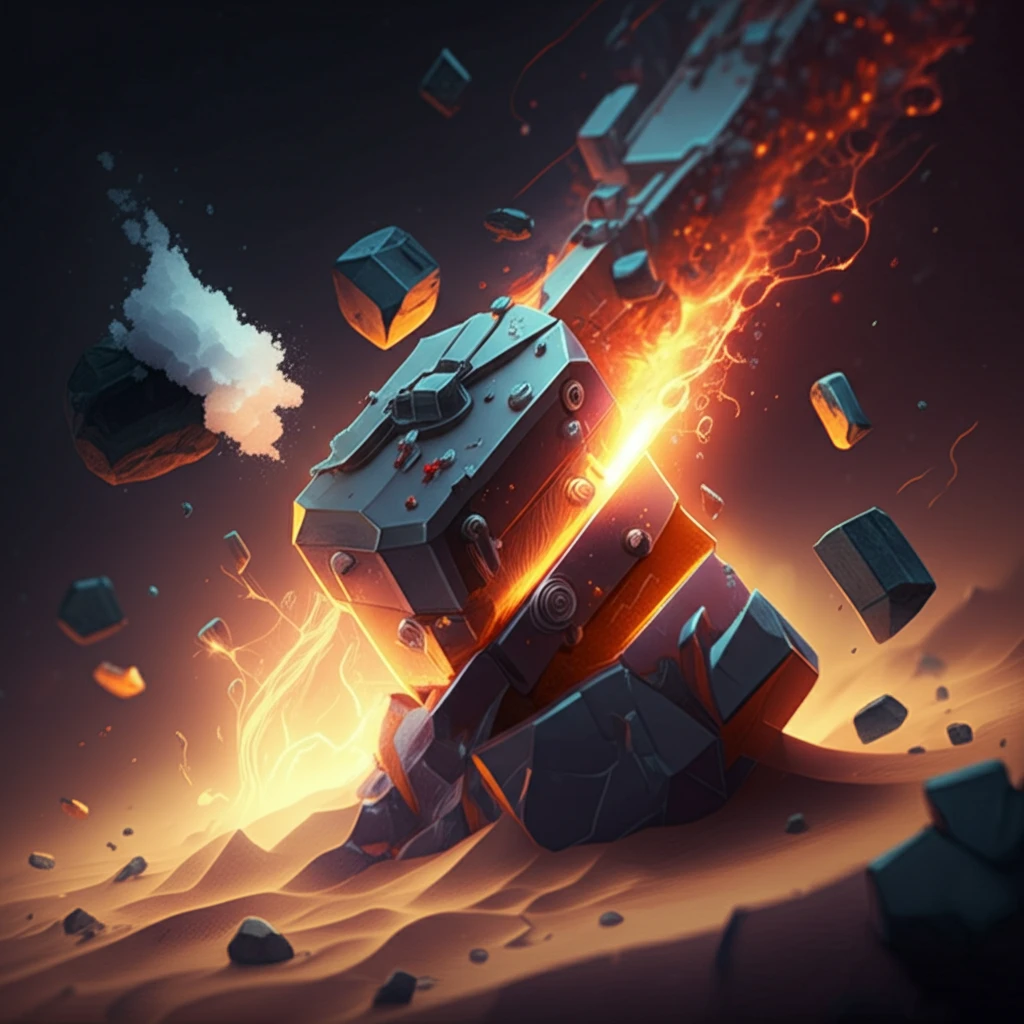
The study meticulously examined the effects of varying temperatures on the iron sand reduction process. Samples of iron sand were mixed with coal (as a reducing agent) and sodium sulphate (as an additive) and then subjected to different temperatures: 700°C, 800°C, and 900°C. The resulting materials were analyzed using X-Ray Diffraction (XRD) to determine the composition and quantity of the formed compounds, particularly titanomagnetite.
- Iron Sand Samples: Characterized by XRD to determine initial composition.
- Coal: Used as a reducing agent to facilitate the removal of oxygen from iron oxides.
- Sodium Sulphate (Na2SO4): Employed as an additive to enhance the reduction process and promote titanomagnetite formation.
- X-Ray Diffraction (XRD): Used to analyze the crystalline structure and composition of the samples after the reduction process.
- Temperature Variation: Reduction experiments conducted at 700°C, 800°C, and 900°C to assess the impact on titanomagnetite formation.
Sustainable Solutions and Future Directions
This research provides valuable insights into optimizing the extraction and transformation of minerals from iron sand. By demonstrating the effectiveness of temperature-controlled reduction using coal and sodium sulphate, it paves the way for more sustainable and energy-efficient methods of producing valuable materials like titanomagnetite. Future studies could explore further optimization of the process, including investigating different types of coal, alternative additives, and innovative reactor designs. The ultimate goal is to develop a cost-effective and environmentally friendly approach to unlocking the full potential of iron sand as a resource for advanced materials and industrial applications.