Unlocking Catalyst Uniformity: How 3D X-ray Tomography is Revolutionizing Material Science
"Explore how advanced imaging techniques are transforming the development of efficient and reliable catalytic converters, paving the way for cleaner technologies."
For decades, monolithic catalysts have played a crucial role in industries ranging from automotive to chemical processing. More recently, open-cell foams have emerged as promising alternatives, offering improved mass and heat transfer capabilities. To harness the full potential of these foams, it’s essential to coat them with a catalytic layer – a process often achieved through dip-coating.
The dip-coating method involves immersing the foam into a liquid suspension, followed by the critical step of removing excess liquid to create a thin, uniform coating. The challenge lies in achieving this uniformity, as inconsistencies can significantly impact catalytic performance. Recent advancements in 3D X-ray tomography have provided a powerful tool to assess and optimize these coatings.
This article explores how 3D X-ray tomography, coupled with image analysis, is revolutionizing the way researchers analyze catalyst distribution within open-cell foams. By visualizing the spatial localization of the catalytic layer, scientists can now fine-tune coating methods to achieve unprecedented levels of uniformity, leading to more efficient and reliable catalytic reactors.
The Power of 3D X-ray Tomography
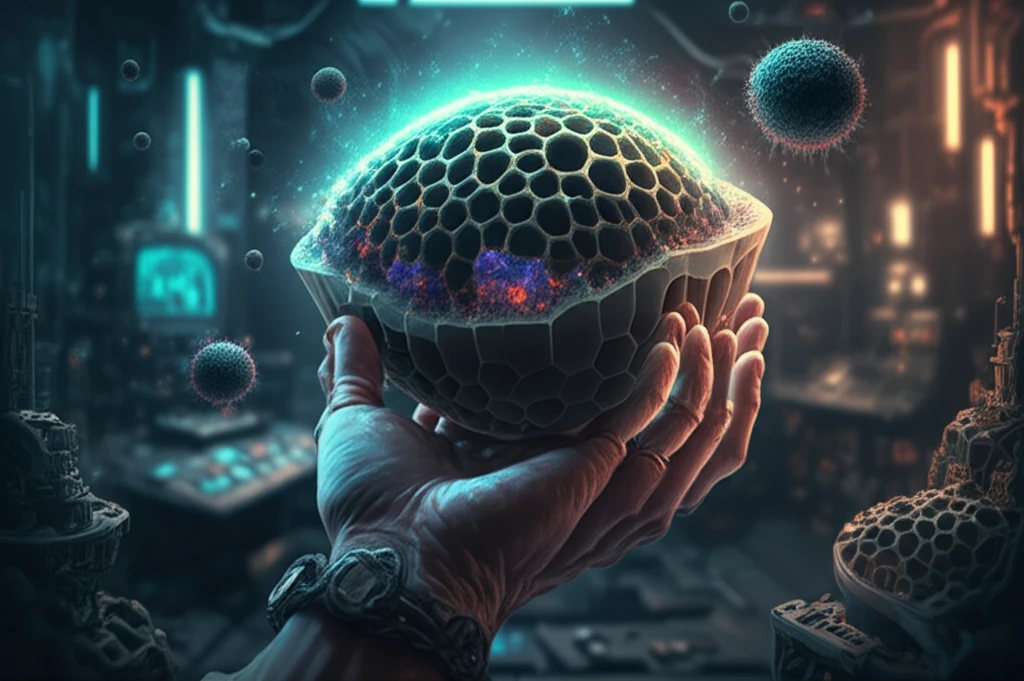
3D X-ray tomography offers a non-destructive method to visualize the internal structure of materials in three dimensions. In the context of catalyst coatings, this means researchers can see exactly how the catalytic layer is distributed throughout the foam structure, identifying areas of over-coating, under-coating, or uneven distribution. This level of detail is simply not possible with traditional methods.
- Non-destructive analysis preserves the sample for further testing.
- Provides detailed 3D visualization of catalyst distribution.
- Enables quantitative measurement of coating thickness and uniformity.
- Facilitates optimization of coating methods for improved performance.
Looking Ahead
As the demand for more efficient and sustainable technologies grows, the importance of optimizing catalytic processes will only increase. 3D X-ray tomography provides a powerful tool for achieving this optimization, enabling researchers to develop catalysts with improved performance, durability, and reliability. By unlocking the secrets of catalyst uniformity, we can pave the way for cleaner air, more efficient chemical processes, and a more sustainable future.