The Future of Plastics: How Flow and Pressure Could Revolutionize Material Performance
"Unlocking the secrets of isotactic polypropylene (iPP) to create stronger, more reliable plastics through advanced crystallization techniques."
In the world of manufacturing, the quest for stronger, more durable materials is never-ending. Polymers, those ubiquitous building blocks of modern life, are often at the center of this pursuit. From the humble plastic bottle to high-tech automotive components, the performance of a polymer hinges significantly on its crystalline structure.
Flow and pressure, two critical factors during polymer processing, can dramatically alter this crystalline structure, influencing the final properties of the material. Imagine the ability to fine-tune these parameters to create plastics with specific, enhanced characteristics. That's precisely what a new study on isotactic polypropylene (iPP) delves into, offering a glimpse into the future of polymer engineering.
Isotactic polypropylene, a common thermoplastic polymer, is known for its versatility and widespread applications. However, achieving optimal performance requires precise control over its crystalline structure. This study, leveraging synchrotron radiation and advanced X-ray scattering techniques, re-examines how the interplay of flow and pressure can induce the formation of thick lamellae – the building blocks of polymer crystals – within iPP, leading to materials with superior qualities.
The Science of Stronger Plastics: Flow, Pressure, and Thick Lamellae
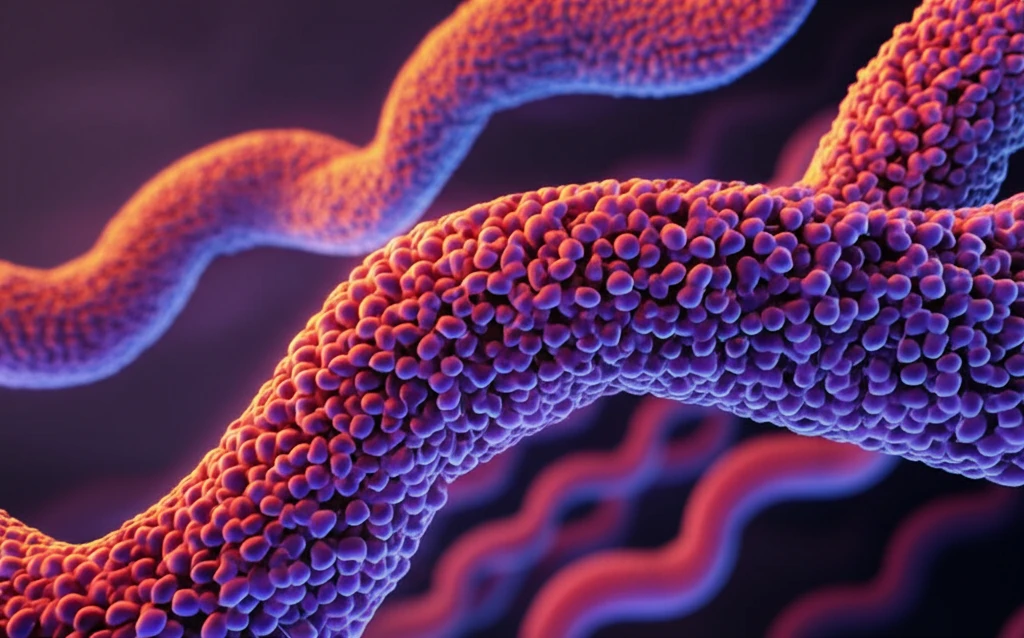
The research focuses on isotactic polypropylene (iPP), a polymer prized for its versatility but whose crystalline structure is key to its performance. By applying shear flow (think of it as a controlled stretching and aligning force) at rates of 3 to 30 s⁻¹ and a constant pressure of 100 MPa (roughly 1000 times atmospheric pressure), scientists were able to observe the formation of distinctly thick lamellae. These lamellae, which are essentially organized layers within the polymer structure, reached a thickness of 28 nanometers, a significant size achieved under these specific conditions. This process led to a material boasting a high melting temperature of 177°C, indicating enhanced thermal stability.
- Oriented Thick Lamellae: The study successfully produced oriented thick lamellae with a thickness of 28 nm under a pressure of 100 MPa and specific shear rates.
- High Melting Temperature: The resulting iPP exhibited a high melting temperature of 177°C, indicating enhanced thermal stability.
- Compact Stacking: The oriented thick α-parent lamellae displayed a small lattice spacing, implying a dense stacking of molecular chains within the crystal.
- Flow-Induced Nuclei: The research suggests that these oriented thick α-parent lamellae originate from flow-induced nuclei, which grow and thicken during isothermal crystallization.
Implications and the Road Ahead
This research provides valuable insights into how flow and pressure can be harnessed to manipulate the crystalline structure of iPP, leading to materials with enhanced properties. The ability to create thick, oriented lamellae with compact molecular packing opens doors for designing high-performance iPP products tailored for specific applications. By understanding and controlling these fundamental parameters, manufacturers can potentially create plastics that are stronger, more durable, and more resistant to heat and stress. Further research promises to unlock even more sophisticated methods for engineering polymer structures, paving the way for a new generation of advanced materials.