Stress-Free Superalloys: How to Boost Fatigue Life in Nickel Alloys
"Discover the innovative techniques researchers are using to combat surface damage and residual stress in nickel superalloys, extending the life of critical components."
In the high-stakes world of aerospace and beyond, the reliability of metal components is paramount. Cracks, dents, and other forms of surface damage can significantly shorten the lifespan of these parts, leading to costly repairs and potential safety hazards. A key area of focus has been on nickel superalloys, prized for their exceptional strength and heat resistance but vulnerable to fatigue failure caused by everyday wear and tear.
Imagine a scenario where a simple tool drop during maintenance could compromise the integrity of a critical engine component. These seemingly minor impacts can create dents and scratches, leading to residual stresses that accelerate fatigue crack growth. The current methods for assessing this damage are often overly conservative, leading to unnecessary part replacements and increased maintenance costs. It's like throwing away a perfectly good apple because of a small bruise.
However, researchers are now digging deeper, exploring the complex interplay between surface damage and fatigue life. By understanding the root causes of failure and developing more accurate prediction models, it's possible to extend the lifespan of nickel superalloy components, reduce maintenance costs, and ensure greater reliability. Let's dive into the fascinating world of material science and explore how cutting-edge research is making a difference.
The Science of Surface Damage: Understanding the Impact on Fatigue Life
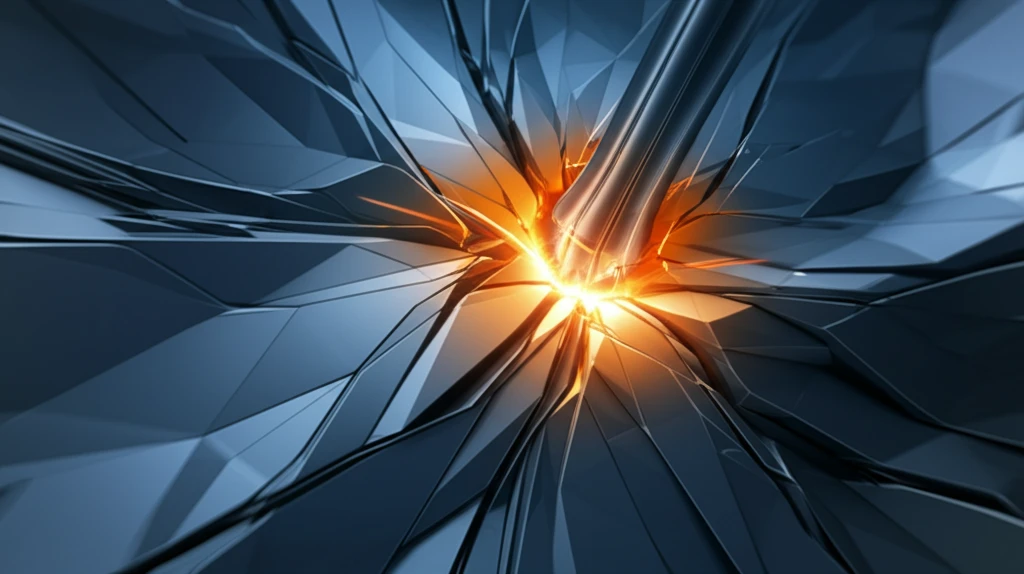
When hard, blunt objects impact the surface of nickel superalloys, they create more than just a visible dent or scratch. This impact generates a zone of residual stress, a hidden force that can significantly impact the material's fatigue life. Think of it like bending a paperclip back and forth – eventually, it weakens and breaks. Similarly, the residual stress caused by surface damage acts as a catalyst for crack formation and growth.
- Geometrical Stress Concentration (Notch Effect): The dent acts like a notch, concentrating stress at its root and accelerating crack initiation.
- Residual Stress Field: The impact generates a complex field of compressive and tensile stresses, influencing crack propagation. Compressive stresses can slow crack growth, while tensile stresses promote it.
- Microstructural Changes: The deformation can alter the material's microstructure, further affecting its fatigue resistance.
The Future of Fatigue Life Prediction: Towards Safer, More Reliable Components
The research into understanding surface damage and residual stresses in nickel superalloys is paving the way for safer, more reliable components in critical applications. By combining advanced modeling techniques with experimental validation, engineers can develop more accurate predictions of fatigue life and optimize maintenance strategies. This not only reduces costs but also enhances safety by preventing unexpected failures. Future research will focus on refining these models, incorporating more complex loading scenarios, and validating predictions with real-world data. The ultimate goal is to create components that are more resilient, longer-lasting, and better equipped to withstand the rigors of demanding operational environments.