Revolutionizing Steelmaking: The Electroslag Remelting Breakthrough You Need to Know
"How a New Current Conductive Stationary Mold Technology is Poised to Transform Material Quality and Manufacturing Processes"
In the relentless pursuit of higher-performance materials, industries are constantly seeking innovative methods to refine their production processes. Electroslag remelting (ESR) has long been a cornerstone of high-quality alloy production, prized for its ability to enhance purity, compactness, and uniformity. However, traditional ESR methods have limitations, particularly in balancing surface quality with internal integrity.
Enter a groundbreaking advancement: Electroslag Remelting with Current Conductive Stationary Mold (ESR-CCSM). This technology represents a significant leap forward, promising to address the shortcomings of conventional ESR by optimizing current flow and thermal distribution during the solidification process. The implications are far-reaching, potentially impacting industries from aerospace to automotive, where material performance is paramount.
This article will explore the principles behind ESR-CCSM, how it differs from traditional ESR, and the potential benefits it offers. Join us as we delve into the science and engineering that could reshape the future of material production.
The Science Behind ESR-CCSM: A New Approach to Current Control
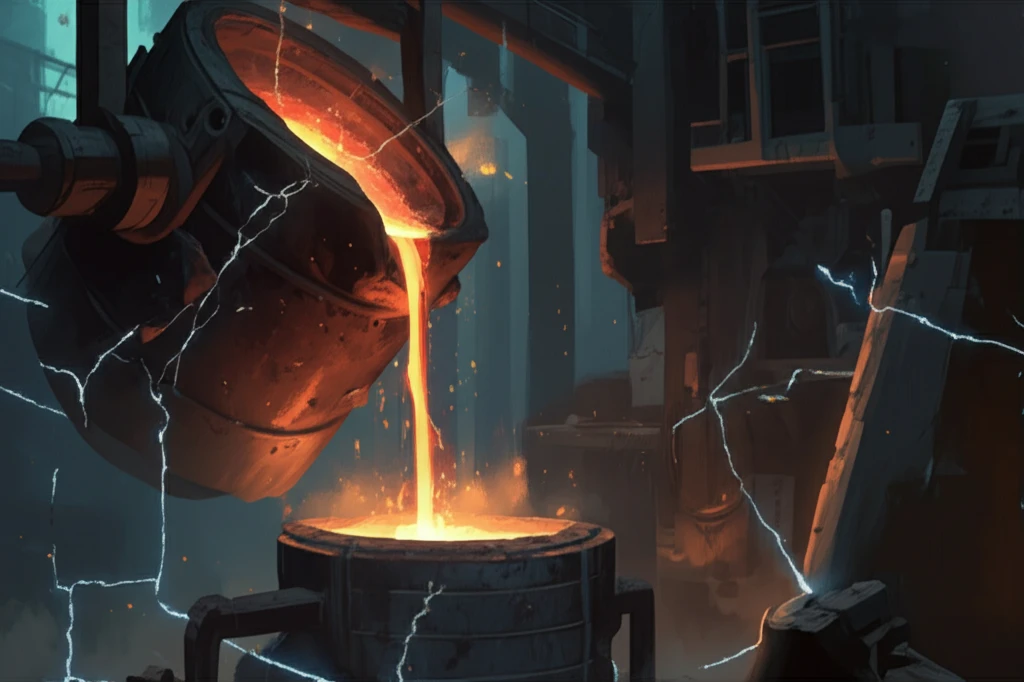
Traditional ESR relies on a specific current flow path: power → consumable electrode → slag → metal pool → solidified ingot → water-cooled baseplate → power. While effective, this method can sometimes lead to inconsistencies in temperature distribution and metal pool depth, affecting the final product's quality. ESR-CCSM reimagines this flow by directly linking the current to the mold. This innovation allows for more precise control over heat generation and distribution within the system.
- Enhanced Temperature Uniformity: More consistent heating reduces the risk of localized defects.
- Shallower Metal Pool: Promotes directional solidification and reduces segregation.
- Improved Surface Quality: Controlled cooling minimizes surface imperfections.
- Optimized Crystallization: Encourages the formation of desirable grain structures for enhanced mechanical properties.
The Future of Steelmaking: ESR-CCSM and Beyond
Electroslag Remelting with Current Conductive Stationary Mold represents more than just an incremental improvement; it signals a paradigm shift in how we approach material production. As industries increasingly demand higher-performance alloys with greater consistency and fewer defects, technologies like ESR-CCSM will become indispensable. By embracing these innovations, manufacturers can unlock new levels of material quality, efficiency, and sustainability, paving the way for a future where the possibilities of material science are limited only by our imagination.