Drag Reduction Revolution: How Air Cavities are Changing Ship Design
"Explore the innovative use of air layer technology in naval architecture, enhancing efficiency and reducing environmental impact."
For decades, the maritime industry has sought ways to improve ship efficiency and reduce fuel consumption. With growing concerns about environmental impact and rising fuel costs, innovative solutions are more critical than ever. One promising technology is the use of air cavities to reduce drag, the resistance a ship encounters as it moves through water.
The concept involves creating a layer of air between the ship's hull and the water, effectively reducing the wetted surface area and, consequently, the frictional resistance. This air layer, often achieved through air injection, allows the ship to glide more easily, leading to significant fuel savings and reduced emissions. While the idea isn't new, recent advancements in computational fluid dynamics (CFD) and experimental techniques have made it more viable.
This article delves into the numerical simulation of air layer morphology on a flat bottom plate with an air cavity, evaluating the drag reduction effect. By examining the dynamic behavior of air layers and their interaction with the hull, we can understand how this technology is shaping the future of naval architecture.
How Do Air Cavities Reduce Drag?
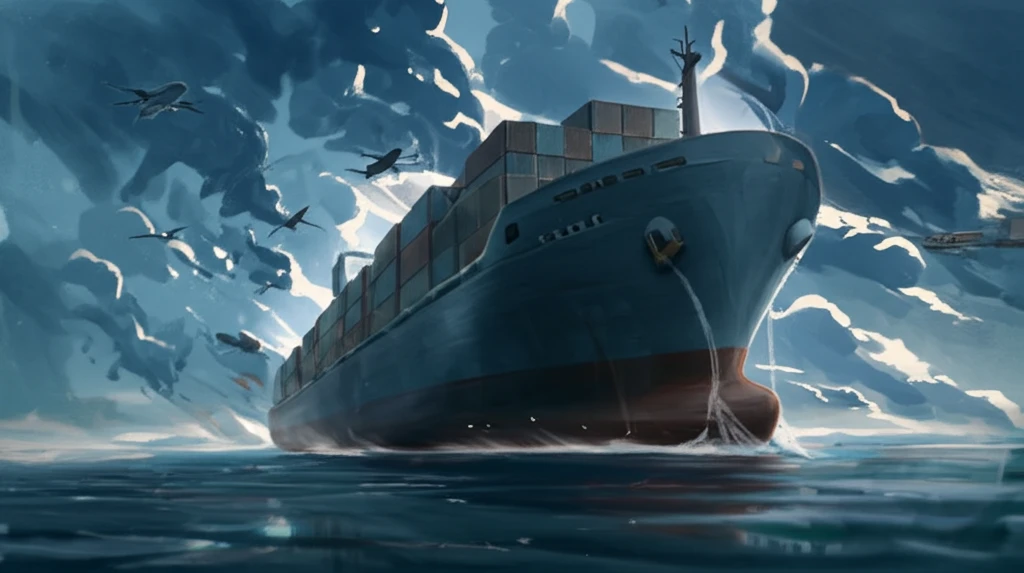
The fundamental principle behind air cavity drag reduction is simple: reduce the contact area between the ship's hull and the water. By injecting air into специально designed cavities on the hull, a layer of air forms, separating a significant portion of the hull from direct contact with the water. This minimizes frictional resistance, which is the primary component of drag for many vessels, especially at lower speeds.
- Air Cavity Design: The shape and dimensions of the air cavity significantly affect the stability and coverage of the air layer.
- Air Injection Rate: The amount of air injected must be carefully controlled to maintain a consistent air layer without excessive air loss.
- Ship Speed and Hull Shape: The technology's effectiveness can vary depending on the vessel's speed and hull geometry, requiring tailored designs for different applications.
The Future of Air Layer Technology
As the maritime industry continues to seek ways to reduce its environmental footprint and improve efficiency, air layer technology is poised to play an increasingly important role. Ongoing research and development efforts are focused on refining air cavity designs, optimizing air injection systems, and exploring new materials and coatings to further enhance drag reduction performance. The future may see widespread adoption of air cavity technology across various vessel types, contributing to a more sustainable and efficient maritime industry.