Unlock the Secrets of Material Strength: How Boron Could Revolutionize Durability
"Scientists explore how manipulating surface layers with boron could lead to stronger, longer-lasting materials in everything from cars to electronics."
In today's world, the quest for stronger, more durable materials is a constant pursuit. Everything from the cars we drive to the electronics we rely on benefits from increased longevity and resilience. Recent research has shed light on a fascinating process called boriding, which involves modifying the surface layers of materials with boron to enhance their mechanical and tribological (friction and wear) properties.
Think of boriding as a high-tech armor plating for the microscopic world. By infusing the surface of a material with boron, scientists are engineering enhanced resistance to wear and tear. This isn't just about making things last longer; it's about improving performance, reducing maintenance, and potentially revolutionizing entire industries. But how does this process work, and what makes boron such a promising element for material enhancement?
This article delves into the innovative techniques of boriding, revealing how the strategic application of boron can dramatically alter a material’s surface characteristics. We'll explore the science behind this process, examining its impact on hardness, elasticity, and overall durability. Imagine components that withstand extreme conditions, reducing downtime and replacement costs. That's the promise of boriding, and we’re here to unpack the details.
The Science of Boriding: A Deep Dive
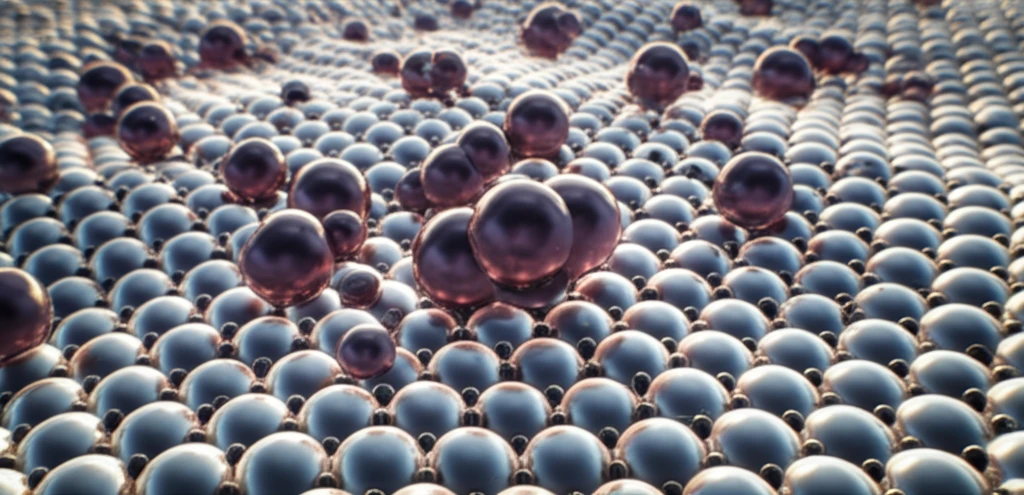
At its core, boriding is a surface-hardening process that diffuses boron atoms into the surface of a metal. This infusion creates a boride layer, a compound of boron and the base metal, which boasts exceptional hardness and wear resistance. The process typically involves heating the metal in a boron-rich environment, allowing the boron atoms to penetrate and form the desired boride layer. The depth and properties of this layer can be precisely controlled by adjusting the temperature, time, and boron concentration of the process.
- Temperature is a critical factor: The depth and composition of the boride layer varied significantly with temperature.
- Phase transformation: Different iron boride phases (Fe2B and FeB) formed depending on the temperature, each with distinct properties.
- Optimal hardness: The highest microhardness was observed in samples borided at around 900°C (1652°F).
The Future of Boriding: Applications and Potential
The research highlights the potential of boriding as a versatile technique for enhancing the durability and performance of materials. By carefully controlling the boriding process, engineers can tailor the surface properties of components to meet specific application requirements. This opens doors to a wide range of possibilities, from extending the lifespan of automotive parts to improving the efficiency of industrial machinery. As materials science continues to advance, boriding is poised to play an increasingly important role in creating stronger, more sustainable products for the future. The ability to manipulate material surfaces at the atomic level offers unprecedented control over their properties, leading to innovations that were once considered science fiction.