Unlock Stronger Welds: A Beginner's Guide to Friction Stir Welding with Aluminum
"Discover how to master friction stir welding (FSW) for aluminum alloys, ensuring high-quality joints and optimal mechanical properties."
Friction stir welding (FSW) has emerged as a game-changing technique for joining metals and composites, offering a straightforward and eco-friendly alternative to traditional welding methods. Unlike conventional welding, FSW avoids melting the materials, reducing environmental hazards and producing high-quality welds across a wide range of materials.
Developed in 1991 by The Welding Institute (TWI) in the UK, FSW has quickly gained global acceptance due to its ability to consistently create welds with minimal distortion, even in materials considered difficult to weld using traditional techniques. This has led to significant cost savings through reduced inspection and re-weld procedures.
This guide breaks down the essentials of FSW with aluminum, focusing on how different process parameters affect the mechanical properties of the weld. We’ll explore the critical factors influencing weld strength and quality, providing you with the knowledge to achieve optimal results in your welding projects.
What is Friction Stir Welding and Why is it Important?
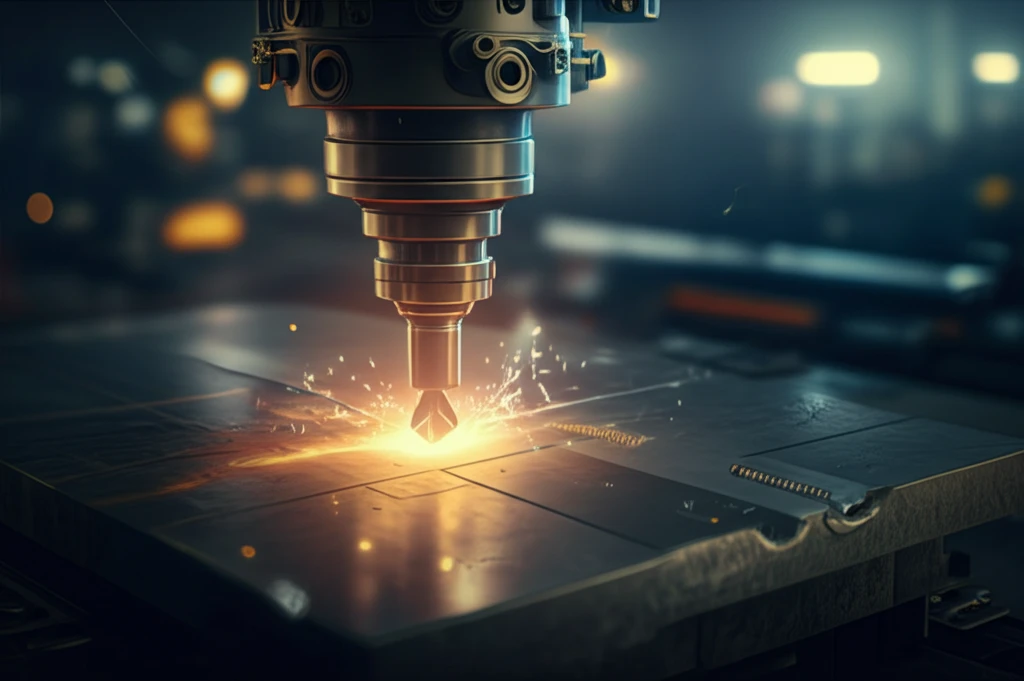
Friction stir welding is a solid-state welding process that joins materials by using a rotating tool to generate frictional heat and plastic deformation at the joint interface. This process involves three main stages:
- High-Quality Welds: Consistently produces welds with low distortion and excellent mechanical properties.
- Versatility: Suitable for a wide range of materials, including aluminum, copper, and steel.
- Environmentally Friendly: Eliminates the need for filler materials and reduces fume emissions.
- Cost-Effective: Reduces the need for extensive inspection and rework.
Mastering FSW for Stronger Aluminum Joints
By understanding and carefully controlling the key process parameters, anyone can harness the power of friction stir welding to create high-quality, reliable joints in aluminum alloys. This guide provides a solid foundation for beginners, empowering you to explore the endless possibilities of FSW and unlock new levels of precision and efficiency in your welding projects.