Soaring to New Heights: How Virtual Testing is Revolutionizing Aircraft Design
"Discover how virtual testing is transforming aircraft high lift systems, making air travel safer and more efficient for everyone."
In the quest for safer and more efficient air travel, the aviation industry is constantly evolving. One of the most promising advancements is the use of virtual testing, which leverages computer simulations to analyze and refine aircraft designs. This approach is particularly impactful in the development of high lift systems, crucial components that enhance an aircraft's ability to take off and land safely.
Traditional methods of aircraft testing involve physical models and real-time simulations, such as test rigs and functional integration benches. While these methods have served the industry well, they can be time-consuming and costly. As aircraft systems become increasingly complex, driven by the need for improved efficiency, the limitations of traditional testing methods become more apparent. This is where virtual testing steps in, offering a complementary and often more efficient alternative.
Virtual testing not only addresses the challenges of complexity and shortened development cycles but also introduces a new level of precision and insight into aircraft performance. By creating detailed computer models, engineers can simulate various flight conditions and identify potential issues early in the design process. This proactive approach helps mitigate risks, reduce development costs, and ultimately enhance the safety and reliability of aircraft.
The Power of Virtual Testing in High Lift Systems
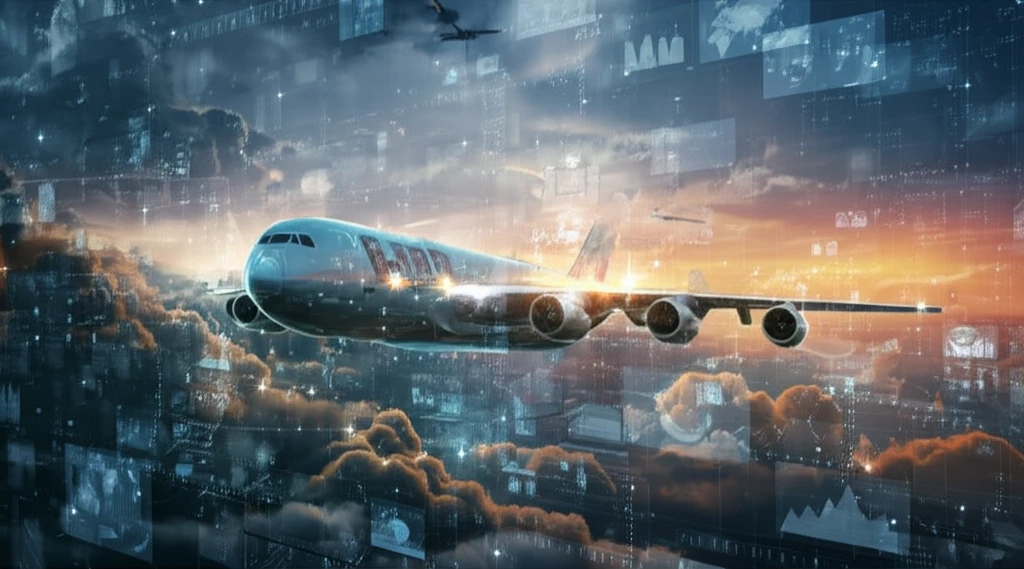
Virtual testing employs sophisticated computer simulations of physical models. This method significantly improves the verification and certification process of an aircraft's high lift system. The growing complexity of aircraft systems, driven by the need for better efficiency, coupled with ever-decreasing development times, necessitates extending traditional testing methods. Virtual testing provides an equivalent, additional test means alongside established physical methods such as test rigs and real-time simulators.
- Linking simulation results to their corresponding models.
- Managing the post-processing of simulation results.
- Tracing the creation of models by capturing model inputs.
- Driving the modeling process efficiently.
The Future of Flight Testing
Virtual testing represents a significant leap forward in aircraft design and certification. By combining physical and virtual tests, the aviation industry can overcome the challenges of increasing system complexity and shortened development timelines. This approach not only enhances the efficiency and traceability of the testing process but also ensures that aircraft are safer, more reliable, and better equipped to meet the demands of modern air travel.