Shielding Breakthrough: How New Steel Composites Are Revolutionizing Nuclear Safety
"Discover how titanium-enhanced, high-boron alloyed stainless steel composite plates are setting new standards in nuclear shielding and material performance."
In an era defined by the growing demand for nuclear energy and advanced shielding technologies, the limitations of traditional materials have become increasingly apparent. Modern protective equipment requires materials that not only offer superior shielding but also demonstrate robust mechanical integrity, corrosion resistance, and resilience against radiation. This demand has spurred intensive research into innovative materials capable of meeting these stringent requirements.
Boron alloyed stainless steel has emerged as a pivotal material in the realm of thermal neutron shielding. Its application in nuclear shields is well-documented, yet challenges remain. Stainless steel with a boron content of approximately 2.0% is known to form hard and brittle borides such as Cr2B, Fe2B, and (Fe,Cr)2B within its matrix. These compounds, often characterized by their dendritic and blocky shapes, significantly compromise the steel's hot forming properties. Overcoming this limitation hinges on achieving a uniform distribution of boron without disrupting the matrix, a goal that demands precise control over the material's microstructure.
The introduction of titanium (Ti) offers a promising pathway to refine the boride distribution within the matrix, thereby enhancing the toughness of high-boron alloyed stainless steel. This approach has garnered considerable attention, prompting detailed investigations into the effects of titanium on the microstructure and mechanical properties of these advanced composites. This article delves into a study focused on high-boron alloyed stainless steel with a 2.25%B content, augmented with titanium. The research explores the evolution of borides within the material's core, the microstructure of the interface, and the resulting mechanical properties of the final product.
The Science Behind Titanium's Impact on Steel
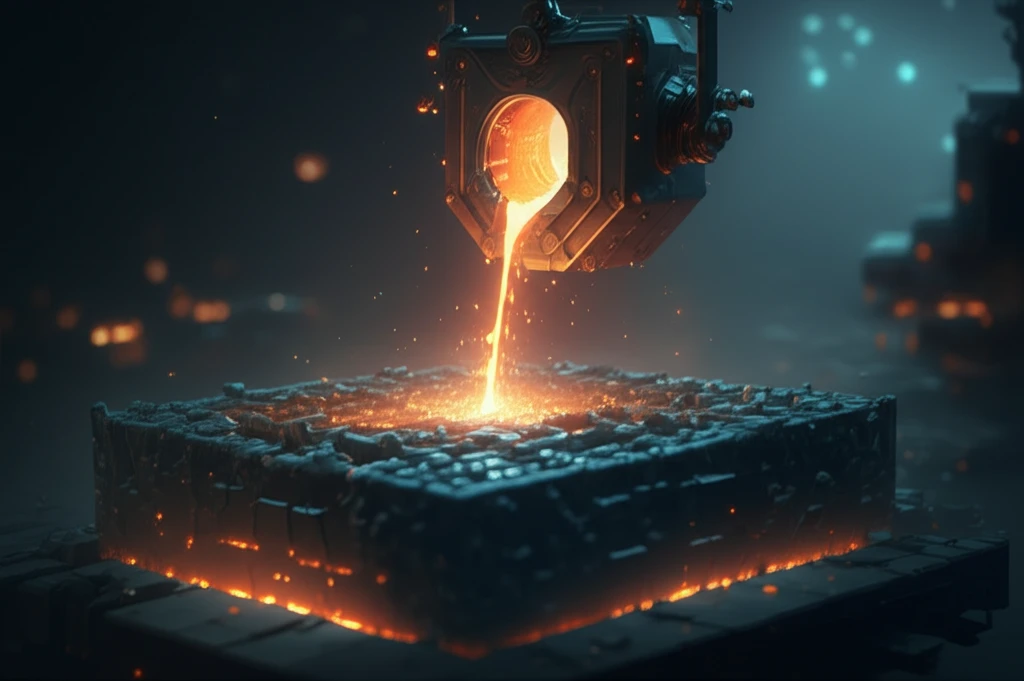
The research detailed in the study involves fabricating a three-layer composite casting slab composed of high-boron alloyed stainless steel containing titanium as the central core, clad with plain 304 stainless steel, which does not contain titanium. This design allows for a focused examination of how titanium influences the core's microstructure and the overall mechanical properties of the composite plate. The material undergoes several key processes, including hot forging, hot rolling, and solution treatment, each designed to optimize its final characteristics.
- Boron Distribution: How titanium promotes a more uniform distribution of boron, preventing the formation of large, brittle boride clusters.
- Phase Transformation: The role of titanium in transforming the boride phases to enhance mechanical properties.
- Processing Effects: How hot rolling and solution treatment further refine the microstructure, optimizing the material for demanding applications.
- Mechanical Performance: The specific improvements in plasticity and overall strength achieved through titanium addition.
Future Implications and Applications
The advancements in high-boron alloyed stainless steel composites containing titanium represent a significant leap forward in materials science and engineering. These materials not only enhance the safety and efficiency of nuclear applications but also pave the way for broader applications in industries requiring high-performance shielding and structural components. As research continues, the potential for further optimization and customization of these composites promises to unlock new possibilities in energy, defense, and beyond.