Micro Marvels: How Laser Wire Deposition is Revolutionizing Thin-Walled Aluminum Components
"Discover the groundbreaking process of micro laser metal wire deposition (µLMWD) and its potential to transform industries with high-precision, lightweight aluminum alloy components."
In recent years, the demand for lightweight materials has surged across various industries, including aerospace, automotive, and consumer electronics. Aluminum alloys, with their exceptional strength-to-weight ratio and corrosion resistance, have emerged as a frontrunner in this materials revolution. Traditional manufacturing methods, however, often fall short when it comes to producing complex, thin-walled aluminum components with the precision and efficiency required for modern applications.
Enter micro laser metal wire deposition (µLMWD), a cutting-edge additive manufacturing technique that's poised to redefine the possibilities of aluminum component fabrication. Unlike conventional methods that involve subtractive processes or powder-based additive manufacturing, µLMWD utilizes a focused laser beam to melt and deposit thin layers of aluminum wire, creating intricate three-dimensional structures with remarkable accuracy and control.
This article delves into the exciting world of µLMWD, exploring its underlying principles, advantages, and potential applications. Drawing insights from a recent research paper, we'll uncover how this innovative process is enabling the creation of high-performance, lightweight aluminum components with tailored properties, paving the way for a new era of design and manufacturing.
What is Micro Laser Metal Wire Deposition (µLMWD) and Why is it a Game-Changer?
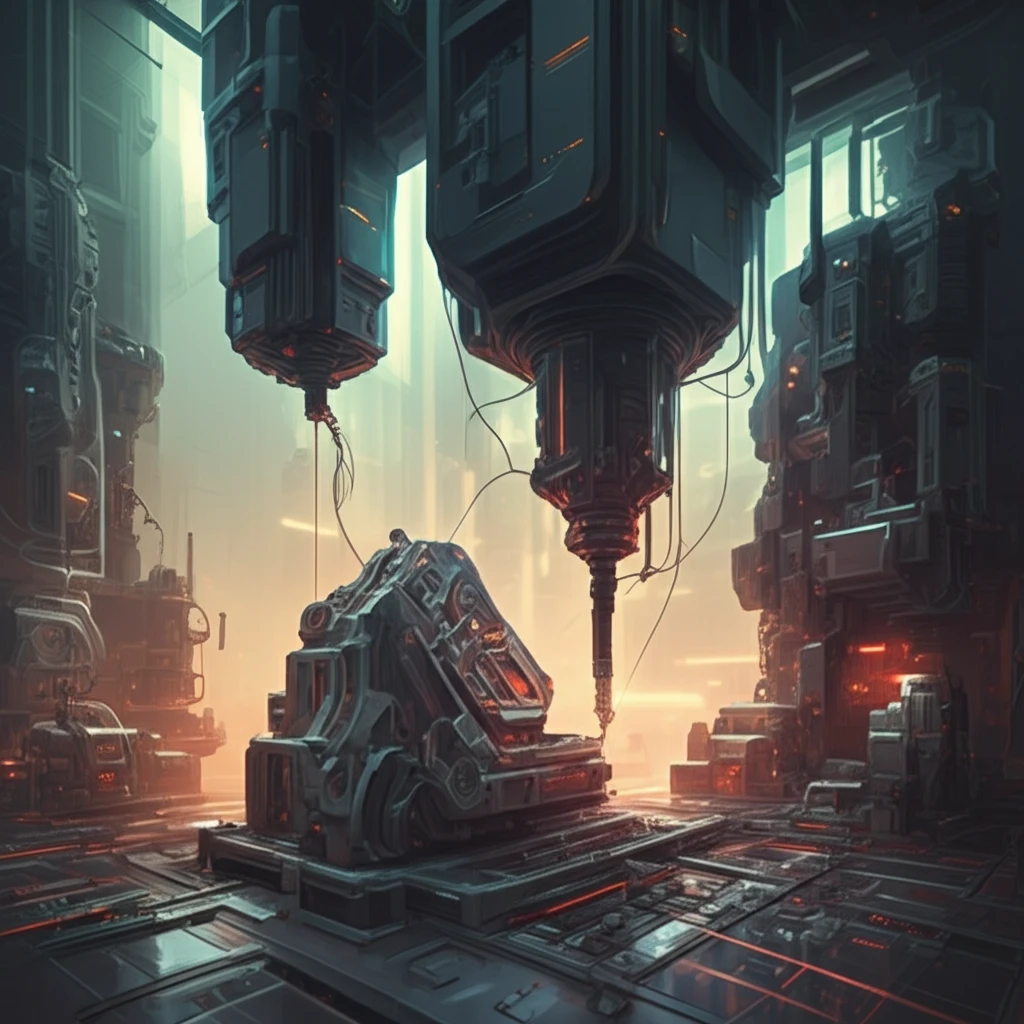
Micro Laser Metal Wire Deposition (µLMWD) is a directed energy deposition (DED) process that uses a laser to melt and deposit a thin metal wire, layer by layer, to create a three-dimensional object. This technique offers several advantages over traditional manufacturing methods and powder-based additive manufacturing processes:
- High Precision: µLMWD allows for the creation of parts with intricate geometries and fine details, making it suitable for applications requiring high accuracy.
- Material Efficiency: Compared to powder-based methods, µLMWD minimizes material waste, as the wire feedstock is directly deposited, reducing the need for post-processing.
- Improved Material Properties: The rapid cooling rates associated with laser deposition can result in enhanced material properties, such as increased strength and hardness.
- Versatility: µLMWD can be used to create freestanding components or add features to existing parts, offering flexibility in design and manufacturing.
- Safer Operation: Using wire feedstock eliminates the risks associated with handling and processing reactive metal powders, enhancing workplace safety.
The Future of Manufacturing is Here
Micro laser metal wire deposition is more than just a manufacturing technique; it's a gateway to a new era of design and production. As research continues to refine the process and expand the range of compatible materials, we can expect to see µLMWD playing an increasingly important role in shaping the future of industries where precision, performance, and sustainability are paramount. From aerospace components to biomedical implants, the possibilities are truly limitless.