Mastering Impedance Control: A Beginner's Guide to DC Servo Motors
"Unlock precision movement: Discover how impedance control transforms DC servo motors for advanced robotics and automation."
DC servo motors are the workhorses of countless applications, from industrial robots to precision medical devices. The secret to their versatility lies in control systems, which dictate how these motors respond to commands. Traditionally, engineers choose between position control (telling the motor where to go) and force control (dictating how much force the motor should exert). But what if you need both? That's where impedance control comes in. It allows you to regulate the relationship between position and force, opening up possibilities for more nuanced and adaptable systems.
Think of a robotic arm tightening a screw. Position control alone might strip the threads, while force control could leave it too loose. Impedance control, on the other hand, allows the arm to 'feel' the resistance and adjust accordingly, ensuring the screw is perfectly tightened every time. It’s a bit like teaching the robot a sense of touch.
This article will guide you through the fascinating world of impedance control for DC servo motors. We'll break down the fundamental concepts, explore different control strategies, and show you how to implement them effectively. Whether you're a student, a hobbyist, or a seasoned engineer, you'll gain valuable insights into this powerful technique.
Why Impedance Control? Balancing Force and Motion
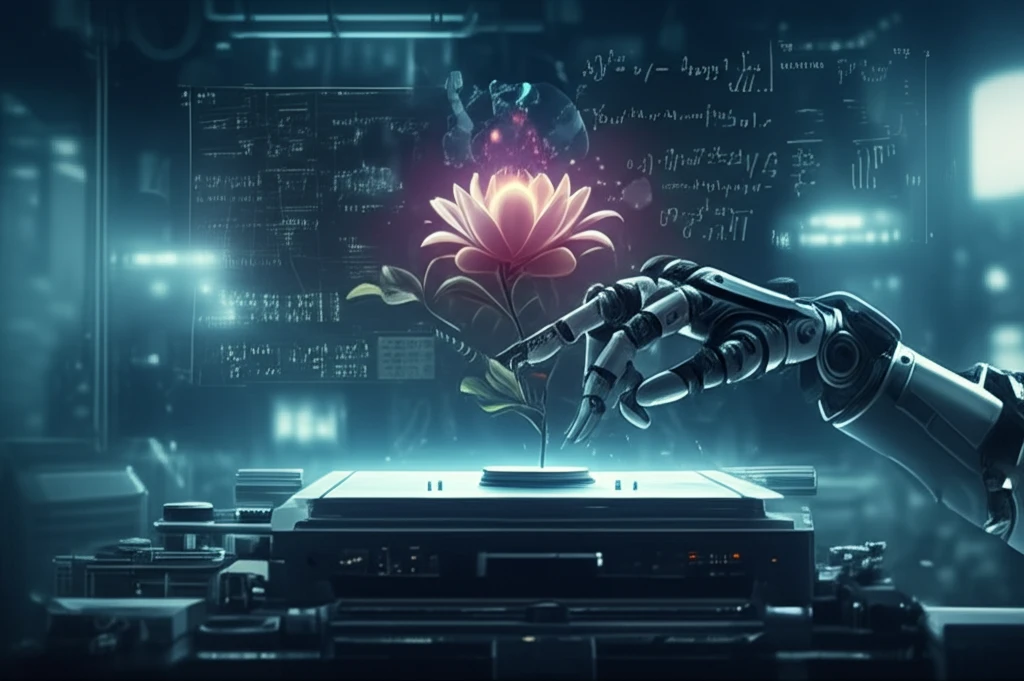
Impedance control isn't just about combining position and force control. It's about defining the relationship between them. Imagine pushing on a spring: the further you push (position), the more force it exerts back. Impedance control allows you to program that spring-like behavior into your DC servo motor.
- Mass (M): Represents the inertia of the system. A higher mass value means the motor will resist changes in motion more strongly.
- Damping/Friction (B): Determines how quickly the motor settles to a desired position. High damping prevents oscillations but can also make the system sluggish.
- Stiffness (K): Controls the motor's resistance to displacement. A high stiffness value means the motor will strongly resist being moved from its desired position.
From Theory to Application: Next Steps in Impedance Control
Impedance control is a powerful tool for designing adaptable and robust robotic systems. While the concepts can be complex, understanding the fundamentals and exploring different control strategies will open up a world of possibilities. Experiment with the methods discussed, fine-tune those parameters, and watch your DC servo motor systems come to life with a newfound sense of touch and adaptability.