LNG Plant Design: Are You Making These Costly Mistakes?
"Critical decisions in LNG plant design, from train size to technology adoption, can dramatically impact project economics. Learn how to optimize your strategy and avoid common pitfalls."
The landscape of LNG export facilities has seen considerable debate around the scale of liquefaction trains, weighing the advantages of mid-scale versus large-scale operations. While mid-scale trains (0.5 – 2 million tonnes per year) may present commercial and executional benefits in specific scenarios, it's crucial to recognize that a one-size-fits-all approach is insufficient. Large-scale trains (exceeding 3 million tpy) often offer economies of scale, underscoring the complexity of this decision.
Ultimately, selecting the optimal solution hinges on aligning with the operator's distinct objectives and circumstances to ensure maximum long term value. Train size and the choice of liquefaction licensor have a surprisingly limited impact on project capital costs, provided the total facility achieves a minimum output of 8 million tpy (Russell, 2018). This article provides a detailed analysis of these factors, offering objective insights for both mid- and large-scale train construction.
We will delve into the essential areas project stakeholders must consider when determining capacity and selecting a liquefaction licensor. Furthermore, this discussion will extend to crucial considerations for optimizing LNG plant design, including mechanical driver selection, the benefits of modularization, and the strategic integration of digital technologies. The article concludes by emphasizing the importance of a holistic approach that encompasses the entire gas value chain, driving down costs, minimizing risks, and maximizing overall project economics.
Why Train Size Matters: Balancing Scale and Flexibility in LNG
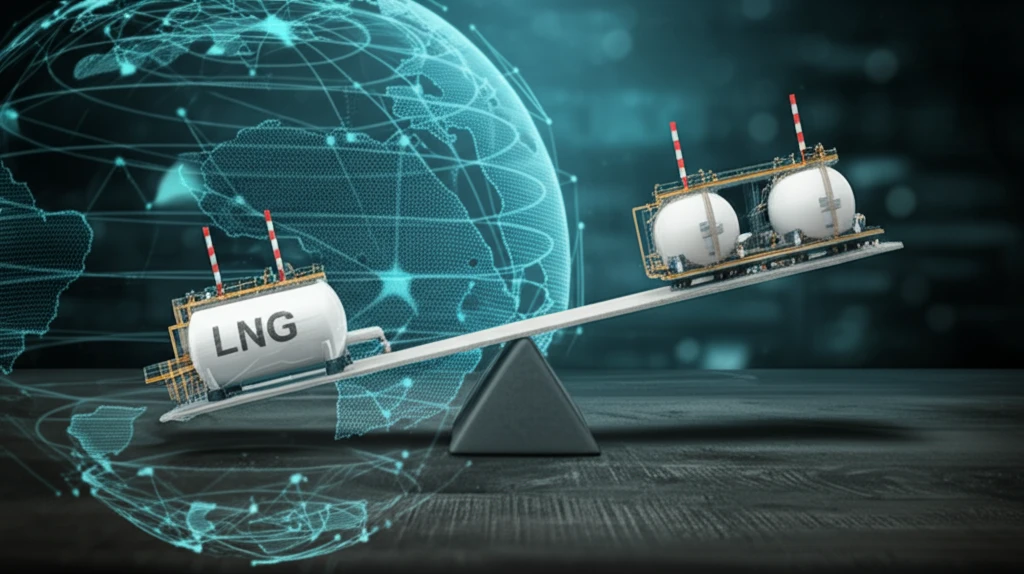
Over the past two decades, the LNG industry has undergone significant transformations. In the period spanning from 1995 to 2005, capital costs for LNG export facilities in many regions were under US$400/t of LNG produced. By 2013, those costs had nearly quadrupled to $1,200/t, and by 2015 some projects in Australia saw capital costs rise as high as $3,500/t (Songhurst, 2014). This surge resulted from factors like limited global gas discoveries, record profits across the value chain, high labor costs, and surging LNG demand.
- Reduced Development Costs: Mid-scale LNG projects often leverage modularization and standardization to decrease initial capital expenditure.
- Faster Market Entry: The streamlined nature of these projects accelerates the delivery of gas to the market.
- Adaptive Capacity: Mid-scale LNG allows capacity to be increased incrementally, aligning with market demand and available feed gas.
Making Informed Choices for a Sustainable Future in LNG
An LNG project typically requires five or more years from initial concept to the final investment decision (FID). During this extended period, significant financial resources and effort are allocated to design and development, regulatory approvals, securing financing, and negotiating offtake agreements. Following FID, several more years are needed for detailed design, manufacturing, and construction before the project achieves commercial operation and generates returns on investment. Selecting the right liquefaction technology and train size are critical technical and commercial decisions for stakeholders involved in developing an LNG project. Owners and developers must consider numerous interrelated factors to reduce costs, including location, gas supply, power sources, and transportation methods. Thorough evaluation of each aspect is crucial to maximizing returns under specific project conditions.