From Lab to Line: How Pilot Hot Rolling Mills are Shaping the Future of Steel
"Unlocking Efficiency and Innovation in Steel Production Through Advanced Process Control Systems"
The steel industry, a cornerstone of modern infrastructure and manufacturing, is constantly evolving. At the heart of this evolution lies the pilot hot rolling mill, a critical tool for experimental research and development of new steel grades and processes. These mills allow for controlled experimentation, paving the way for innovations that eventually make their way into large-scale production.
Pilot hot rolling mills are not new, but recent advancements in their automation and control systems have significantly enhanced their capabilities. These modern mills are equipped with sophisticated measuring devices and automation, enabling precise control over the rolling process and detailed data collection. This level of control is essential for optimizing steel properties and developing specialized products.
This article delves into the workings of a state-of-the-art pilot hot rolling mill, focusing on its process control system (PCS) and how it contributes to enhanced precision and efficiency in steel production. We'll explore the key components of the system, its functions, and real-world applications, demonstrating the transformative potential of this technology.
The Anatomy of a Pilot Hot Rolling Mill
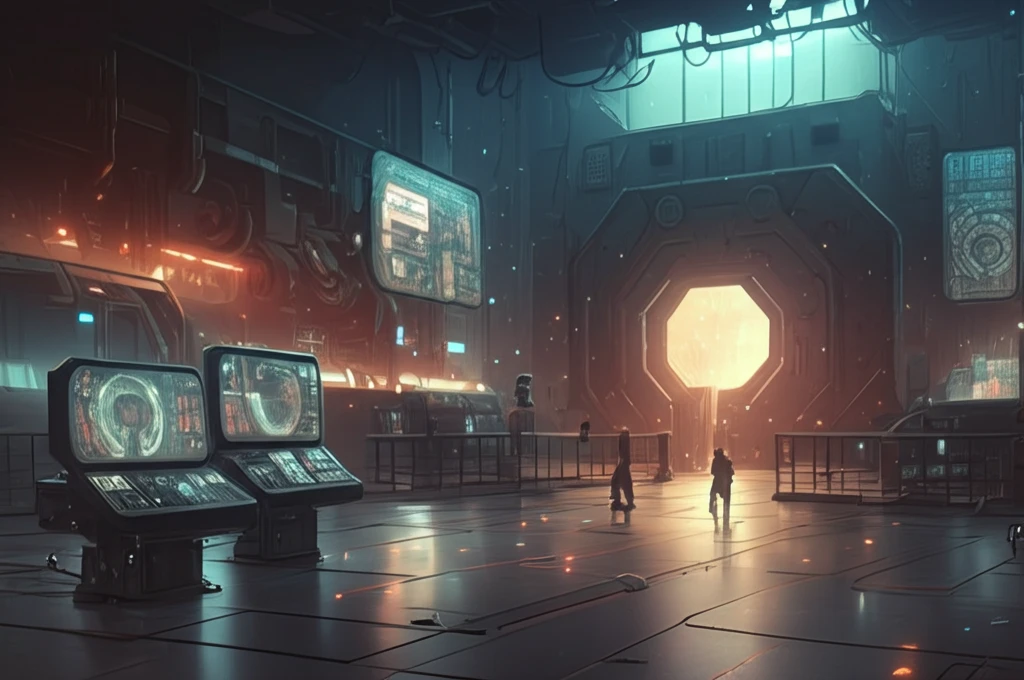
The pilot hot rolling mill replicates the essential steps of a full-scale hot rolling process, but on a smaller, more manageable scale. The process begins with a slab of steel that is heated to a high temperature in a furnace. This heated slab is then passed through a series of rolling stands, where it is gradually shaped and elongated into the desired dimensions. Descaling machines remove any surface oxides formed during heating, ensuring a clean and uniform product.
- Basic Automation System (BAS): The BAS handles the fundamental control functions of the mill, such as motor control, hydraulic systems, and safety interlocks.
- Process Control System (PCS): The PCS is the brains of the operation, responsible for managing the rolling process itself. It collects data from sensors, executes control algorithms, and adjusts mill parameters to achieve the desired product characteristics.
- Human Machine Interface (HMI): The HMI provides operators with a user-friendly interface to monitor and control the mill. It displays real-time data, allows operators to adjust settings, and provides diagnostic information.
The Future of Steel is Precise
The integration of advanced process control systems into pilot hot rolling mills represents a significant leap forward for the steel industry. These systems enable researchers and manufacturers to optimize steel production, develop new and improved steel grades, and enhance the efficiency of their operations. As technology continues to advance, we can expect even greater precision and control in steel manufacturing, leading to stronger, more durable, and more sustainable materials for a wide range of applications. The pilot hot rolling mill, once a simple experimental tool, is now a driving force behind innovation in the steel industry.