Decoding Cracks: How Deposition Techniques Impact the Strength of Metal Alloys
"Dive into the science of metal deposition and discover how controlling the process can prevent structural failures."
In the world of aerospace, where precision and reliability are paramount, the nickel-based IN718 superalloy stands as a critical material. Known for its exceptional strength at high temperatures, its resistance to corrosion, and its impressive fatigue strength, IN718 is a staple in the construction of aero engine components. However, these components, particularly turbine blades, face constant stress and vibration, making them susceptible to fatigue and potential failure.
To combat this, laser additive manufacturing has emerged as a key technique for repairing damaged components and creating new ones. This method involves depositing materials layer by layer using a high-energy beam, allowing for precise control over the final product. Yet, the very process that makes it so valuable—the rapid heating and cooling—can also introduce significant residual stress, leading to hot cracking in the deposited alloy. Overcoming this cracking is essential to ensure the integrity and longevity of these critical parts.
Recent research has focused on understanding and mitigating weld metal liquation cracking, a common issue in laser-deposited IN718 alloys. While some micro-cracks can heal, larger issues like pores, coarse eutectic formations, and thermal stress remain a concern. This article will delve into a study analyzing how different alloying powders and cooling conditions affect crack formation in laser-deposited IN718 alloys. We'll explore the microstructural characteristics and analyze the impact of metallurgical factors and residual stress on crack sensitivity.
How Do Deposition Parameters Influence Crack Sensitivity?
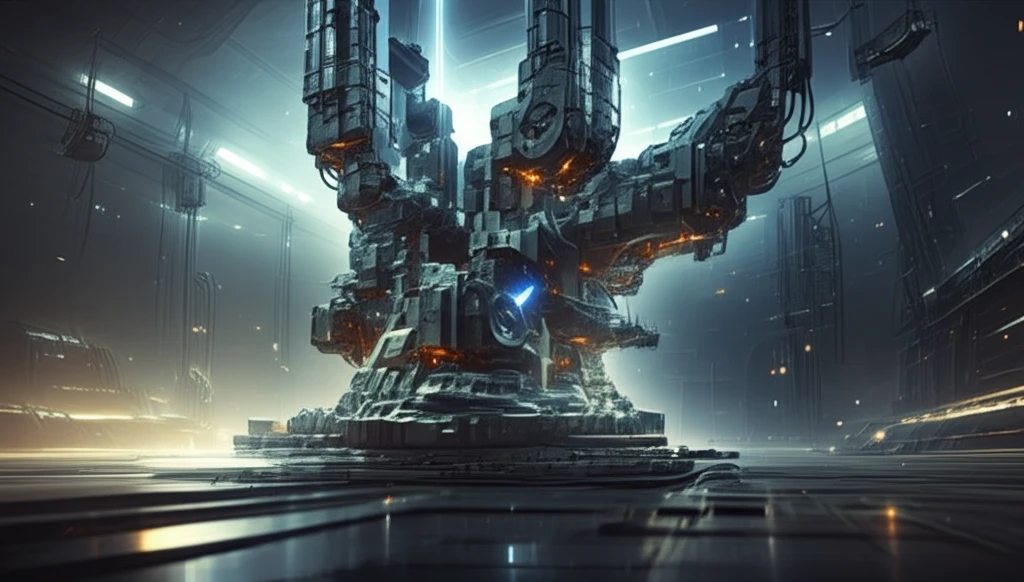
A study examined the effects of varying deposition parameters on the microstructure and crack susceptibility of IN718 alloys. Researchers fabricated IN718 alloys using laser cladding under different conditions, carefully analyzing the resulting microstructures and crack formations. This meticulous approach allowed them to pinpoint the factors that contribute to cracking and identify potential strategies for improvement.
- Dendritic Laves Phases: Continuous formations create weak interfaces susceptible to cracking.
- Nanohardness Distribution: Uneven hardness indicates stress concentrations, promoting crack initiation.
- Crack Propagation: Cracks spread along laser scanning and buildup directions, influenced by residual stress.
Engineering Stronger Alloys for the Future
This research provides valuable insights for optimizing laser deposition processes to minimize cracking in IN718 alloys. By carefully controlling cooling rates, alloy composition, and deposition parameters, manufacturers can reduce the risk of crack initiation and propagation, leading to stronger, more reliable components. The findings emphasize the importance of understanding the complex interplay between metallurgical factors and residual stress in additive manufacturing, paving the way for improved techniques and more durable materials in aerospace and other critical industries.