Beyond the Hype: How High-Entropy Ceramics Could Revolutionize Aerospace
"Unlocking the potential of advanced materials for extreme environments."
The quest for materials that can withstand extreme conditions has long been a driving force behind scientific innovation, especially in fields like aerospace. Ultra-high temperature ceramics (UHTCs), including carbides and borides, have emerged as promising candidates for thermal protection systems due to their exceptional heat resistance and hardness. However, their limitations in sinterability and fracture toughness have hindered widespread adoption.
Now, a new class of materials called high-entropy carbides (HECs) is capturing the attention of researchers worldwide. These unique solid solutions, composed of four or more transition metal carbides in near-equal proportions, exhibit superior properties compared to traditional monocarbides. Specifically, HECs demonstrate enhanced hardness and improved resistance to oxidation, making them ideal for applications in the most demanding environments.
Recent research published in Scripta Materialia details an innovative method for synthesizing single-phase high-entropy carbide powders. This breakthrough could pave the way for more efficient and reliable production of HECs, unlocking their full potential for use in hypersonic aerospace and other extreme applications.
What Makes High-Entropy Carbides So Special?
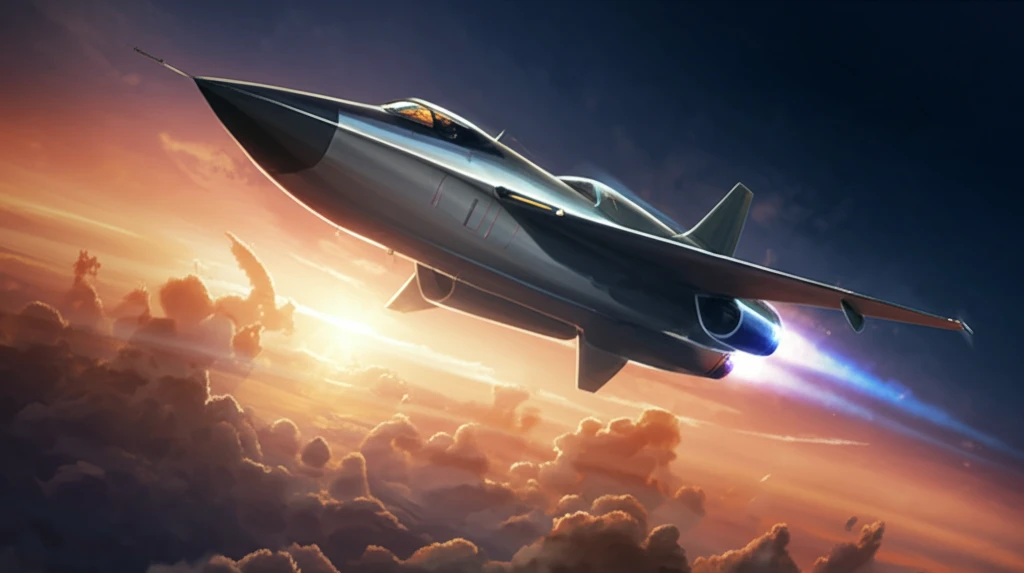
Traditional ceramics often consist of a single metallic element combined with carbon, boron, or nitrogen. High-entropy carbides, however, defy this convention by incorporating multiple metallic elements in a single, homogenous phase. This unique composition gives rise to several remarkable properties:
- Enhanced Hardness: The presence of multiple elements distorts the crystal lattice, making it more difficult for dislocations (defects that cause material failure) to move. This results in significantly higher hardness compared to conventional carbides.
- Improved Oxidation Resistance: The complex composition of HECs creates a more stable oxide layer on the surface, preventing further oxidation at high temperatures.
- Lower Thermal Diffusivity: Some HECs exhibit lower thermal diffusivity and conductivity than their single-component counterparts, which could improve their ability to insulate components from extreme heat.
The Future is Hot: HECs for Extreme Environments
The development of this two-step synthesis method represents a significant step forward in the field of high-entropy ceramics. By enabling the production of fine, high-purity HEC powders, this approach could pave the way for more efficient and reliable manufacturing of components for hypersonic aircraft, re-entry vehicles, and other demanding applications. While further research is needed to optimize the sintering process and fully characterize the properties of these materials, the potential of HECs to revolutionize aerospace and beyond is undeniable.