Beat the Heat: How Advanced Coatings Keep Turbine Engines Cool
"Explore the groundbreaking thermal barrier coatings revolutionizing turbine engine efficiency and longevity, ensuring optimal performance under extreme temperatures."
In the relentless pursuit of greater efficiency and performance, modern gas turbines operate under increasingly extreme conditions. At the heart of this technological frontier lies the challenge of managing intensely high temperatures that threaten the structural integrity and operational lifespan of turbine components. Thermal barrier coatings (TBCs) have emerged as a critical solution, providing a protective shield that allows turbines to operate at temperatures far exceeding the melting point of their metal alloys. But the story doesn't end there.
The integration of TBCs with advanced film cooling techniques represents the cutting edge in turbine engine thermal management. Film cooling involves introducing a thin layer of cool air between the hot gases and the component surface, further reducing the thermal stress. When combined effectively, TBCs and film cooling offer a synergistic effect, enhancing both performance and durability. However, the complexities of this integration—particularly in realistic operating conditions—require continuous research and innovation.
One of the most pressing challenges is understanding how these systems perform over time, especially when exposed to contaminants that can deposit on the coatings and cooling holes. This deposition can severely impact the cooling effectiveness and overall engine performance. Recent research is focusing on realistic scenarios, exploring advanced trench designs within TBCs to mitigate these issues and maintain optimal cooling efficiency. Let’s dive into the innovative methods pushing the boundaries of what’s possible in turbine engine technology.
The Science of Staying Cool: Film Cooling and TBCs
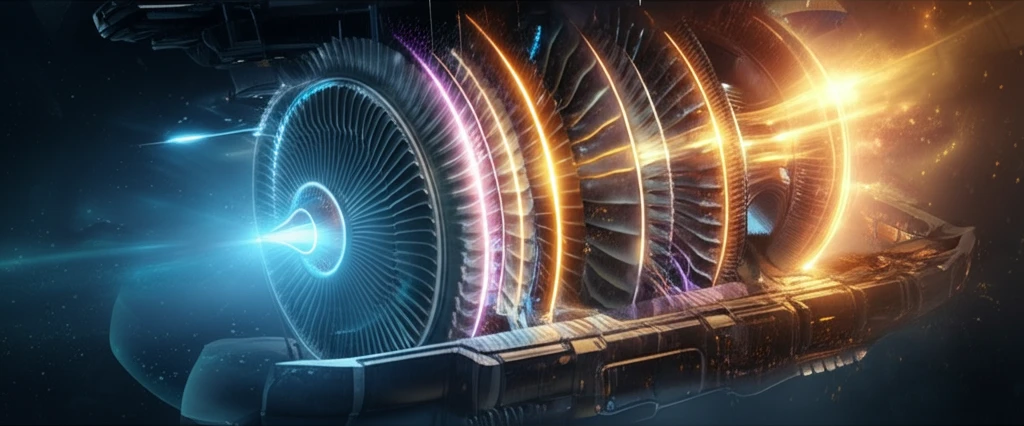
The core concept behind thermal barrier coatings is elegantly simple: create a layer of insulation that minimizes the heat transferred to the underlying metal. Typically made from ceramic materials with very low thermal conductivity, TBCs reduce the metal temperature significantly. Film cooling works by bleeding cool air from the compressor and channeling it through small holes in the turbine components. This air forms a thin film that acts as a barrier against the hot gas flow, reducing direct heat transfer. The effectiveness of film cooling depends greatly on the geometry of the cooling holes and the flow rate of the coolant air. This is a balancing act; too little airflow, and the component isn't adequately protected; too much, and engine efficiency suffers.
- Improved Efficiency: Higher turbine inlet temperatures mean more power from the same amount of fuel.
- Enhanced Durability: Reduced thermal stress extends the lifespan of critical components.
- Optimized Performance: Synergistic effects of TBCs and film cooling provide superior thermal management.
- Advanced Design: Sophisticated geometries maximize cooling effectiveness and minimize coolant usage.
Looking Ahead: The Future of Turbine Cooling
The ongoing research into TBCs and film cooling is crucial for advancing turbine engine technology. As engines are designed to operate at even higher temperatures, the demands on thermal management systems will continue to increase. Innovations in coating materials, cooling geometries, and deposition mitigation strategies will be essential. Future work will likely focus on developing more robust TBCs that are less susceptible to spallation and contaminant deposition, as well as optimizing trench designs to balance cooling effectiveness with deposition resistance. The ultimate goal is to create turbine engines that are not only more efficient but also more durable and reliable, ensuring they can meet the energy demands of the future.