3D Printing Breakthrough: How SLM Technology is Revolutionizing Manufacturing
"Unlock the potential of Selective Laser Melting (SLM) and discover how it's overcoming challenges to reshape industries worldwide."
Additive manufacturing (AM), often called 3D printing, has changed how we create things across different sectors. Selective Laser Melting (SLM) stands out among these technologies. SLM involves using a laser to melt and fuse metal powders layer by layer, creating complex, custom parts. It's like building with tiny grains of metal, offering unparalleled design freedom and precision.
However, getting SLM right isn't easy. One major hurdle is predicting and managing residual stresses—internal stresses trapped within the manufactured part. These stresses can cause distortions, cracks, and even failure, undermining the benefits of this advanced technology. Understanding and controlling these stresses is critical to unlocking SLM's full potential.
That's where innovative research steps in. A recent study focused on using parametric finite element models to fine-tune the SLM process. By simulating how different parameters affect heat distribution and stress, engineers can optimize the process for stronger, more reliable parts. Let’s dive into how this modeling approach works and how it's paving the way for better 3D-printed metal components.
Understanding the Finite Element Model for SLM Optimization
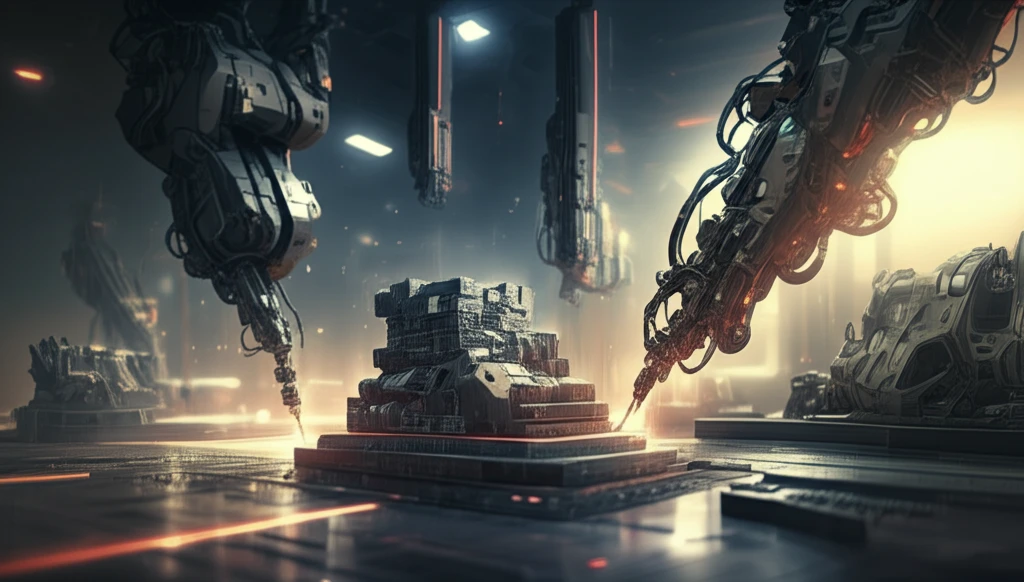
The key to improving SLM lies in understanding the intricate relationship between process parameters, material properties, and resulting stress. The finite element (FE) model helps break down this complexity, offering a virtual environment to test and refine manufacturing strategies. Here’s what makes this approach so effective:
- Thermal Behavior: How heat distributes and dissipates during laser melting.
- Material Transformations: Changes in the material as it transitions from powder to liquid to solid.
- Progressive Activation: Simulating the gradual build-up of the component layer by layer.
The Future of SLM: Precision, Reliability, and Beyond
The use of parametric finite element models represents a significant step forward in optimizing SLM additive manufacturing. By understanding and controlling residual stresses, we can unlock the full potential of this technology, creating stronger, more reliable parts for a wide range of industries. With ongoing research and development, SLM promises to revolutionize manufacturing, offering unprecedented design freedom and performance.