Unlocking Corrosion Resistance: The Science of Titanium Nitride Thin Films
"Dive into the cutting-edge research exploring how titanium nitride thin films, created through plasma discharge, could revolutionize material protection and high-tech applications."
In a world increasingly reliant on high-performance materials, the quest for durable, corrosion-resistant coatings is more critical than ever. Among the various techniques available for creating these protective layers, plasma discharge deposition stands out as a promising method. Specifically, the use of cathodic cage discharge, a relatively new technique, has garnered attention for its ability to create thin films with unique properties.
Titanium nitride (TiN) has emerged as a leading material in this field due to its exceptional hardness, high-temperature stability, and excellent corrosion resistance. Its applications span diverse industries, from biomedical implants to cutting tools and decorative coatings. As technology advances, the demand for TiN coatings with enhanced performance characteristics continues to grow.
This article explores the innovative work of researchers who have investigated the electrochemical behavior of TiN thin films deposited on silicon using a plasma discharge technique in a cathodic cage. By manipulating the deposition parameters, such as gas flow and temperature, they've uncovered valuable insights into how these factors influence the films' corrosion resistance and overall performance. These findings promise to unlock new possibilities for tailoring TiN coatings to specific applications, ensuring longevity and reliability in demanding environments.
The Science Behind Titanium Nitride Thin Films
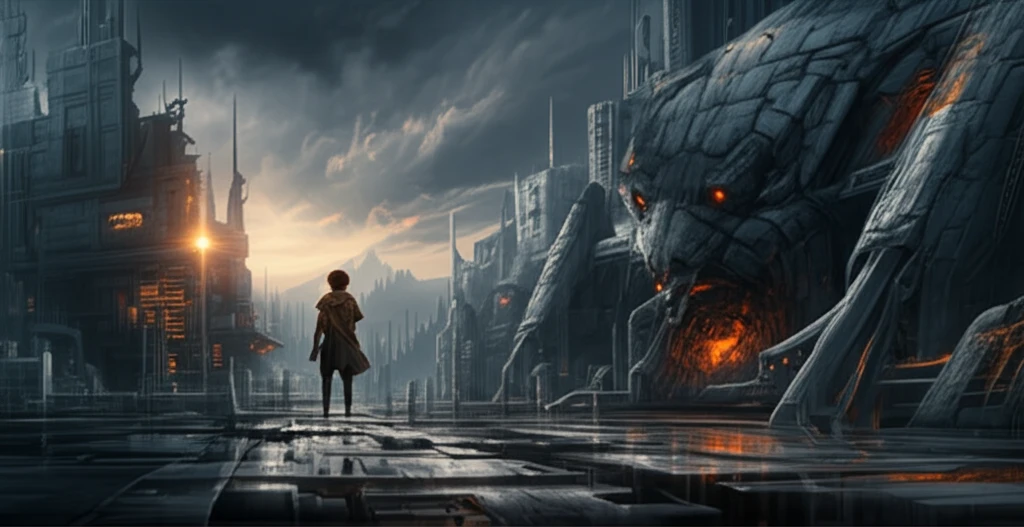
Titanium nitride thin films are created through a process called plasma discharge deposition, a method within the broader category of Physical Vapor Deposition (PVD). In this technique, a cathodic cage, developed and patented, plays a crucial role. The cage, typically a cylinder with or without holes, helps eliminate edge effects and overheating issues common in traditional plasma treatments. This results in more uniform and controlled film deposition.
- Use of existing equipment present in plasma labs
- High rate of films deposition
- Potential to deposit amorphous films with desired magnetic properties
- Excellent corrosion resistance
The Future of Protective Coatings
This study underscores the potential of plasma discharge deposition using a cathodic cage to create TiN thin films with tailored corrosion resistance. By carefully controlling the deposition parameters, researchers can fine-tune the electrochemical properties of the films, making them suitable for a wide range of applications. Further research and development in this area promise to unlock even greater possibilities for creating high-performance, cost-effective protective coatings that enhance the durability and longevity of materials across various industries.