Unlock the Future: How Digital Twins are Revolutionizing Internal Combustion Engine Development
"Cut costs and development time with virtual engine testing using digital twins – the technology transforming the automotive industry."
In today's fast-paced industrial landscape, the pressure to innovate quickly and efficiently is higher than ever. For the automotive industry, this means finding ways to develop and test internal combustion engines (ICEs) faster and at a lower cost. Enter digital twin technology—a game-changing approach that's transforming how engines are designed, tested, and optimized.
Digital twins are virtual replicas of physical systems, processes, or products. They allow engineers to simulate real-world conditions, test different scenarios, and identify potential issues before they ever manifest in a physical prototype. This technology is rapidly gaining traction in the development and production of internal combustion engines, offering unprecedented opportunities to enhance performance, reduce development time, and cut costs.
Traditionally, developing and testing ICEs has been a complex and time-consuming process. It involves extensive physical prototyping, rigorous testing under various conditions, and iterative design improvements. However, digital twins are changing the rules of the game by providing a virtual environment where engineers can experiment and optimize engine designs without the limitations and expenses of physical testing.
What Makes Digital Twins the Key to Next-Gen Engine Design?
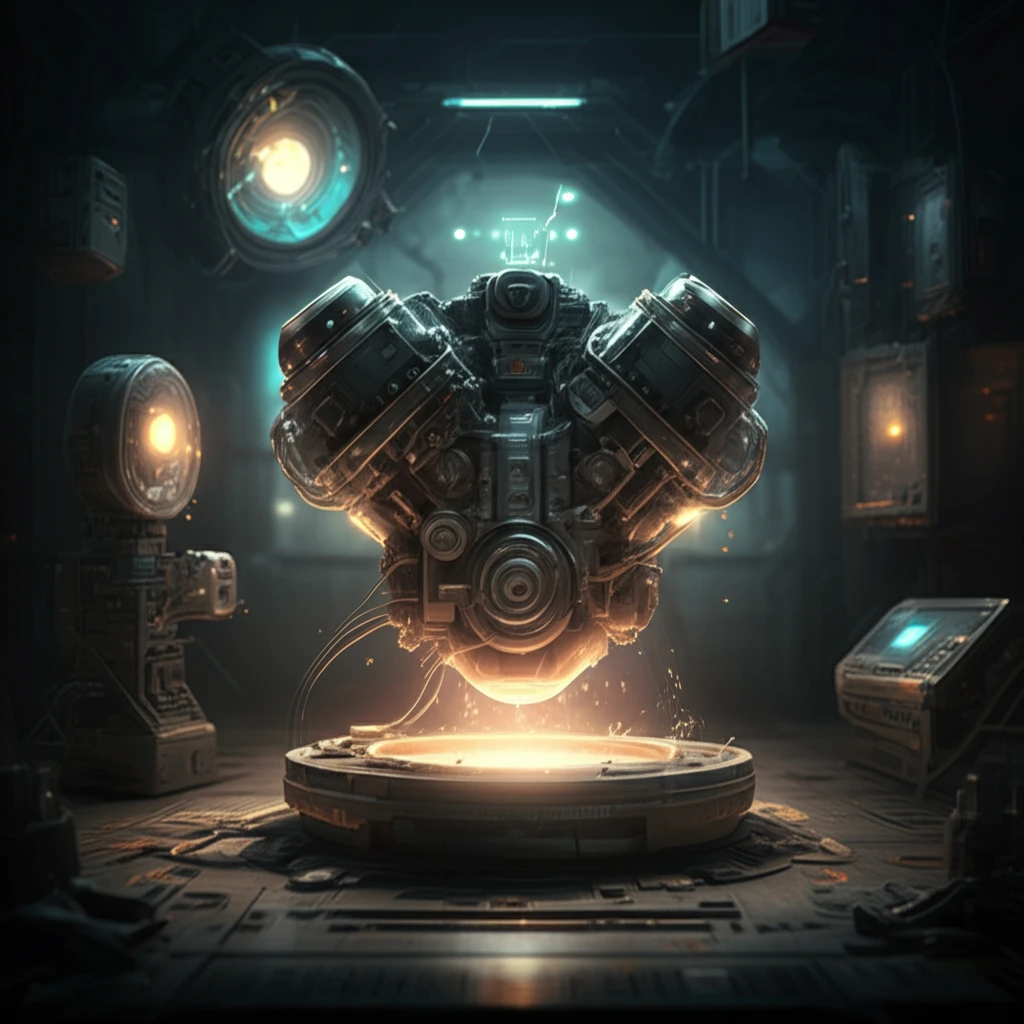
Digital twin technology offers a comprehensive and integrated approach to engine development. Unlike traditional methods that rely on physical prototypes and isolated testing, digital twins provide a holistic view of the engine's behavior, allowing engineers to understand the interplay between different systems and mechanisms. By creating a virtual replica of the engine, engineers can:
- Test under various conditions: Engineers can subject the digital twin to a wide range of operating conditions, from cold starts to high-speed runs, without the need for physical testing facilities.
- Optimize performance: By analyzing the simulation results, engineers can identify areas for improvement and optimize engine parameters to enhance performance, fuel efficiency, and emissions.
- Predict potential issues: Digital twins can help predict potential failures and identify design flaws early in the development process, reducing the risk of costly rework and delays.
- Reduce development time and costs: By replacing physical prototypes with virtual models, digital twins significantly reduce the time and expense associated with engine development and testing.
The Road Ahead: Embracing Digital Twins for a Sustainable Future
Digital twin technology is poised to play an even greater role in the future of internal combustion engine development. As engines become more complex and regulations become more stringent, the ability to simulate and optimize engine designs in a virtual environment will be essential for meeting performance, efficiency, and emissions targets. By embracing digital twins, the automotive industry can accelerate innovation, reduce costs, and create more sustainable and efficient engines for the future.