Unlock Superior Coatings: The Power of Hybrid Sputtering
"Discover how combining dcMS and HPPMS technologies revolutionizes industrial coatings for enhanced durability and performance."
In the world of advanced materials, protective coatings are essential for enhancing the lifespan and performance of components across various industries. Physical Vapor Deposition (PVD) techniques, particularly those involving chromium-based nitride coatings, have become increasingly popular for their ability to provide superior wear and corrosion resistance. To optimize these coatings, researchers are constantly exploring new methods to refine the deposition process, with the goal of creating materials that offer both high performance and economic viability.
One promising avenue of exploration is the use of hybrid deposition processes, which combine the strengths of different sputtering techniques. Among these, the hybrid dcMS/HPPMS (direct current magnetron sputtering/high power pulse magnetron sputtering) approach has garnered significant attention. DcMS provides high deposition rates, making it economically attractive, but coatings produced by HPPMS typically exhibit higher hardness, denser morphologies, and smoother surfaces. The challenge lies in harmonizing these two techniques to achieve a synergistic effect.
This article delves into a study that investigates the influence of HPPMS on hybrid dcMS/HPPMS processes. Conducted using an industrial-like coating process with multiple cathodes and targets, this research offers valuable insights into how combining these methods can lead to improved coating properties, revolutionizing the way we protect and enhance materials.
Deciphering the Hybrid dcMS/HPPMS Process
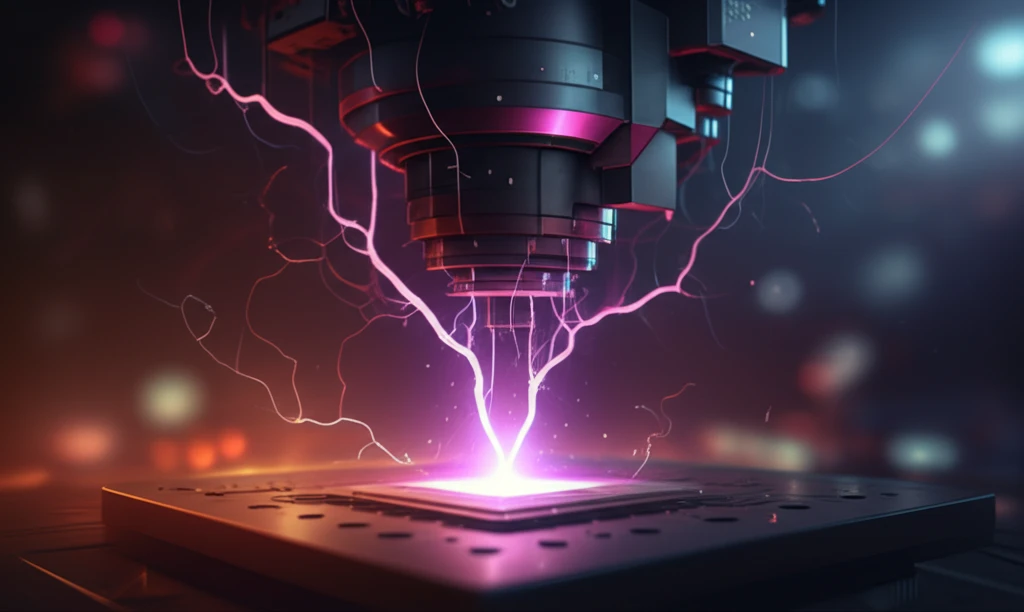
The core of the study revolves around understanding the effects of integrating HPPMS into dcMS processes. Researchers embarked on a detailed analysis of (Cr, Al)N coatings, which were meticulously deposited using industrial-grade equipment. This setup featured six cathodes strategically arranged to coat quenched and tempered tool steel, specifically AISI 420 (X42Cr13, 1.2083). The primary goal was to assess how HPPMS impacts the coating plasma at the substrate level and the resultant characteristics of the deposited coatings.
- Analyzing plasma with fine spatial resolution
- Monitoring plasma composition using optical emission spectroscopy (OES)
- Analyzing morphology and deposition rate using scanning electron microscopy (SEM)
- Determining Al and Cr content using energy dispersive X-ray spectroscopy (EDS)
Revolutionizing Coatings Through Hybrid Technology
In conclusion, this research underscores the transformative potential of hybrid dcMS/HPPMS processes in industrial coating applications. By meticulously analyzing plasma properties and correlating them with the resulting coating characteristics, the study provides invaluable insights into optimizing these techniques. The combination of dcMS and HPPMS offers a pathway to create coatings with enhanced performance and economic viability, setting the stage for future innovations in material science and engineering.