Underwater Welding: The Secret to Stronger, More Durable Metals
"Dive into the world of underwater welding and discover how it's revolutionizing industries with its superior strength and resilience."
Ever wondered how massive structures like oil rigs and ships stay afloat and intact? The answer often lies beneath the surface, in the realm of underwater welding. This specialized technique is not just a cool feat of engineering; it's a critical process that's transforming how we build, repair, and maintain essential infrastructure.
Underwater welding, or friction stir welding (FSW) and underwater friction stir welding (UFSW), involves joining metals in a submerged environment. This might sound like a challenge, but it offers significant advantages over traditional welding methods. It's a process that produces stronger, more durable welds, with fewer defects. As a result, various industries are increasingly turning to this technology to ensure the longevity and safety of their assets.
This article will dive deep into the world of underwater welding, exploring its principles, benefits, and applications. Whether you're a curious enthusiast or a professional in the field, you'll discover how this technique is revolutionizing the way we work with metals underwater and in the air.
The Science Behind Underwater Welding: How It Works
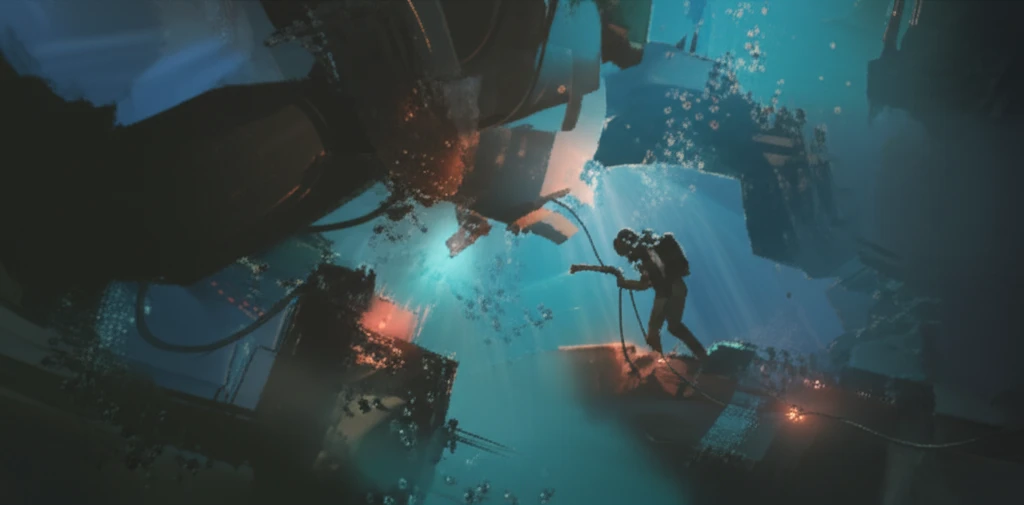
At its core, underwater welding is about joining metals under water, usually by friction stir welding. The process involves creating a localized heat source to melt or fuse the metals together, and the water plays a crucial role in this. The water acts as a cooling agent, which has several benefits. It helps to control the temperature, which reduces the risk of distortion and other welding defects.
- Controlled Cooling: Water rapidly cools the weld, reducing distortion and preventing the formation of cracks.
- Reduced Oxidation: The water shields the weld from oxygen, minimizing oxidation and improving the weld's integrity.
- Enhanced Safety: Specialized equipment and techniques are employed to ensure the safety of the divers and the integrity of the weld.
The Future of Underwater Welding
Underwater welding is a dynamic field, and ongoing research and development continue to improve its capabilities. As technology advances, we can expect to see even more sophisticated techniques and materials used in underwater welding. From improved safety measures to enhanced weld quality, the future of underwater welding holds exciting possibilities, ensuring the continued durability and safety of structures that are essential to our modern world.