Thermoelectric Breakthrough: Enhancing Efficiency with Innovative Wet Etching
"New Research Reveals How Wet Etching Can Significantly Improve the Performance of Thermoelectric Devices"
Thermoelectric modules are gaining increased attention as a promising avenue for sustainable energy solutions, capable of converting heat energy directly into electricity and vice versa. These modules leverage the Seebeck effect, generating electric currents from temperature gradients, and the Peltier effect, creating temperature differences through electric currents. Their application in thermoelectric generators requires numerous elements to be connected in series, making the quality and reliability of each bond critical to overall performance.
A significant challenge in the fabrication of these modules lies in ensuring robust and durable connections between the thermoelectric elements and the conductive layers. Traditional soldering methods often suffer from the formation of brittle intermetallic compounds, particularly when using tin-based solders with telluride-based thermoelectric materials. These compounds degrade the bond strength over time, reducing the module's efficiency and lifespan. A common solution involves creating a diffusion barrier, often a nickel or nickel alloy layer, between the thermoelectric material and the solder.
Electroless plating is an attractive method for applying these barrier layers, offering uniform coating thickness even on complex shapes. However, achieving strong adhesion between the electrolessly plated layer and the thermoelectric element can be difficult. Surface treatments like sandblasting have been used to enhance adhesion by increasing surface roughness, but this method can introduce unwanted physical damage. Recent research explores a gentler approach: wet etching. Wet etching uses chemical solutions to selectively remove material from the surface, creating a controlled roughness without the drawbacks of mechanical methods.
The Science Behind Wet Etching for Enhanced Thermoelectric Performance
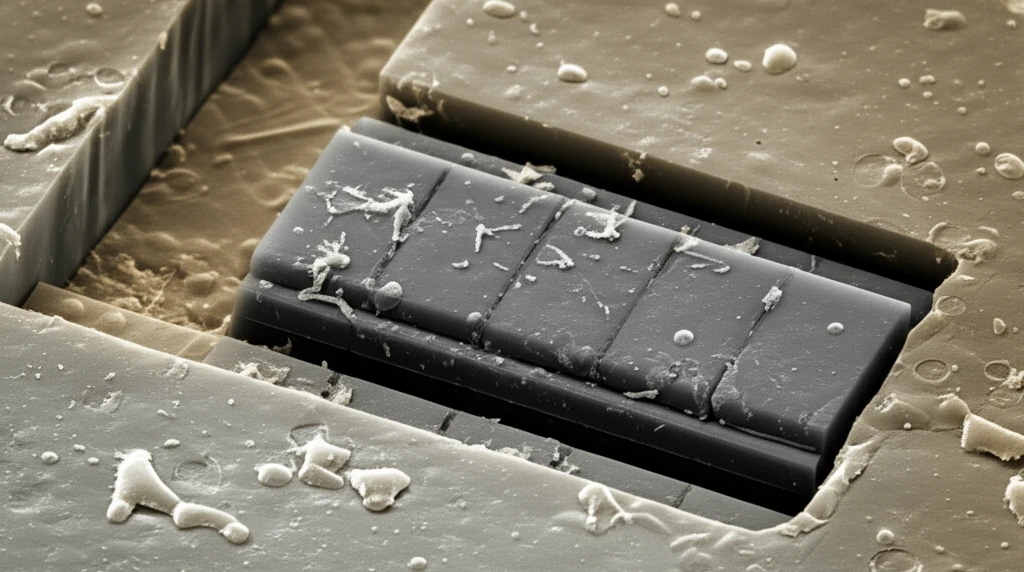
A study published in the Journal of Nanoscience and Nanotechnology details a novel wet etching method to improve the electroless nickel-phosphorus (Ni-P) plating on bismuth-telluride (Bi-Te) thermoelectric elements. The research focuses on creating a reliable and efficient fabrication process for thermoelectric modules, addressing common issues related to bond strength and durability. The team, led by Sung Hwa Bae from Kyungpook National University, investigated the impact of wet etching on the surface properties of Bi-Te elements and the resulting adhesion of the Ni-P plating.
- Improved Adhesion: Wet etching significantly increased the surface roughness of the Bi-Te thermoelectric element, creating an anchoring effect that enhanced the adhesion of the Ni-P plating.
- Enhanced Bond Strength: Thermoelectric modules fabricated using the wet etching method demonstrated excellent bond strength, with values around 10 MPa.
- Heat Treatment Stability: The Ni-P plating exhibited remarkable adherence, even after heat treatment at 200°C for 24 hours, indicating its suitability for high-temperature applications.
- Uniform Plating: The electroless plating method ensured a uniform thickness of the Ni-P layer, crucial for consistent performance of the thermoelectric module.
Future Directions and Implications
This research demonstrates the potential of wet etching as a viable and effective method for enhancing the fabrication of thermoelectric modules. By carefully controlling the etching process, it is possible to create a surface roughness that promotes strong adhesion of electrolessly plated layers without causing physical damage to the thermoelectric material. This approach can lead to more durable and efficient thermoelectric devices, which are essential for various applications, including waste heat recovery, automotive thermoelectric generators, and portable power sources. Future studies could focus on optimizing the etchant composition and etching parameters to further improve the performance and reliability of thermoelectric modules.