The Productivity Puzzle: How Smart Maintenance Can Unlock Your Business Potential
"Balancing Act: Integrating Maintenance for Peak Performance"
In today's fast-paced business environment, productivity reigns supreme. Every minute counts, and unexpected disruptions can wreak havoc on your bottom line. While many businesses focus on optimizing production processes, they often overlook a critical factor: maintenance. Reactive maintenance, where repairs are only performed when equipment fails, is a recipe for disaster. Not only does it lead to costly downtime, but it also disrupts schedules and strains resources.
Imagine a scenario where a critical machine breaks down in the middle of a major production run. Orders are delayed, customers are frustrated, and profits take a hit. This is the reality for businesses that neglect preventive maintenance. But what if you could predict and prevent these breakdowns before they occur? What if maintenance could be seamlessly integrated into your operations, minimizing disruptions and maximizing efficiency?
This is the promise of proactive and optimized maintenance strategies. By combining smart maintenance practices with your existing operations, you can unlock new levels of productivity and create a more resilient and profitable business. Let's explore how integrating sequence-dependent setup time considerations and preventive maintenance policies can transform your business.
Why Sequence-Dependent Setup Times Matter
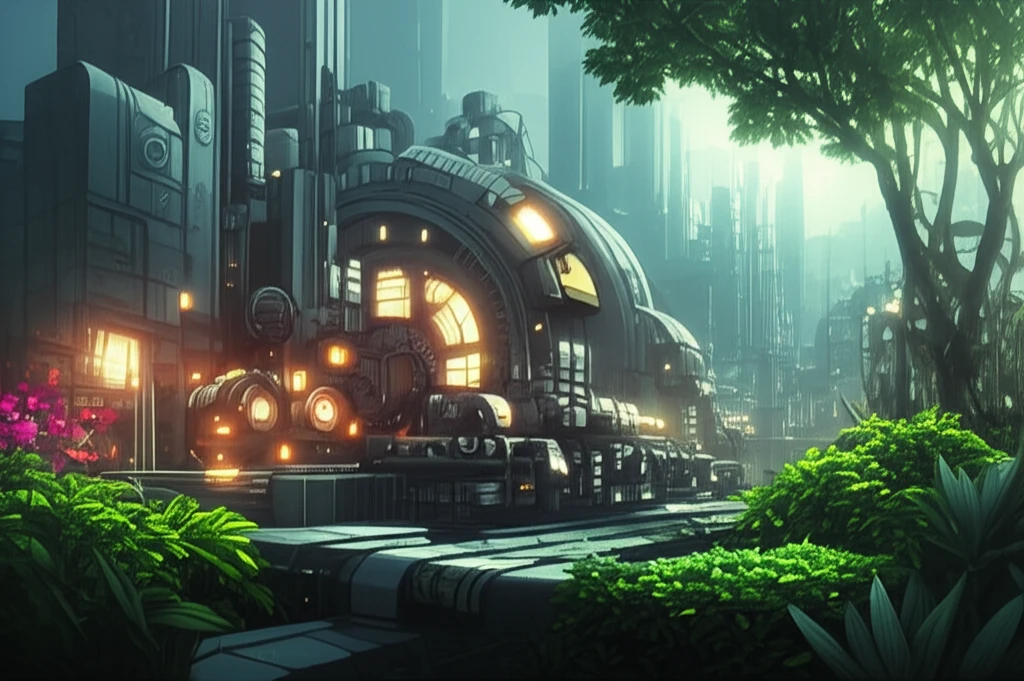
In many production environments, the time it takes to set up a machine for a new task isn't constant. It depends on the order in which jobs are processed. This is known as sequence-dependent setup time (SDST). Ignoring SDST can lead to inaccurate scheduling and increased downtime.
- Improved Scheduling Accuracy: Considering SDST leads to more realistic and efficient production schedules.
- Reduced Downtime: Optimizing job sequences minimizes setup times and keeps machines running longer.
- Increased Throughput: Efficient setups translate to more jobs completed in a given time.
- Cost Savings: Lower setup times and reduced downtime directly impact your bottom line.
The Future of Productivity is Proactive
Integrating preventive maintenance and SDST considerations isn't just about fixing problems; it's about building a more resilient, efficient, and profitable business. By embracing these strategies, you can unlock your business's full potential and gain a competitive edge in today's dynamic marketplace.