The Comfort Code: How Variable Stiffness Can Revolutionize Hand Exoskeletons
"Unlocking the secrets of optimal hand exoskeleton design with variable stiffness profiles to enhance comfort and performance."
Imagine a glove that enhances your hand's strength and dexterity, assisting with tasks from delicate surgeries to heavy lifting. That's the promise of hand exoskeletons, wearable robots designed to augment human capabilities. However, a significant hurdle remains: discomfort. Traditional exoskeletons often create concentrated pressure points, leading to pain and limiting their usability. The key to unlocking the full potential of these devices lies in understanding and optimizing the interface between the machine and the human hand.
The challenge is that the human hand is not uniformly rigid. Its bony prominences and soft tissues have varying degrees of stiffness. When a rigid exoskeleton applies force, it can create pressure hotspots, especially on the dorsal (back) surface of the hand. This is where the robot typically attaches, bearing the brunt of reaction forces from the fingers. The result is often discomfort, which can lead users to abandon the device, regardless of its potential benefits.
Researchers are pioneering a new approach: variable stiffness profiles. Instead of a uniformly stiff interface, they propose designing exoskeletons with contact points that adapt to the hand's natural stiffness variations. The goal is to distribute pressure more evenly, minimizing discomfort and improving the overall experience.
Decoding the Hand: Measuring and Modeling Stiffness
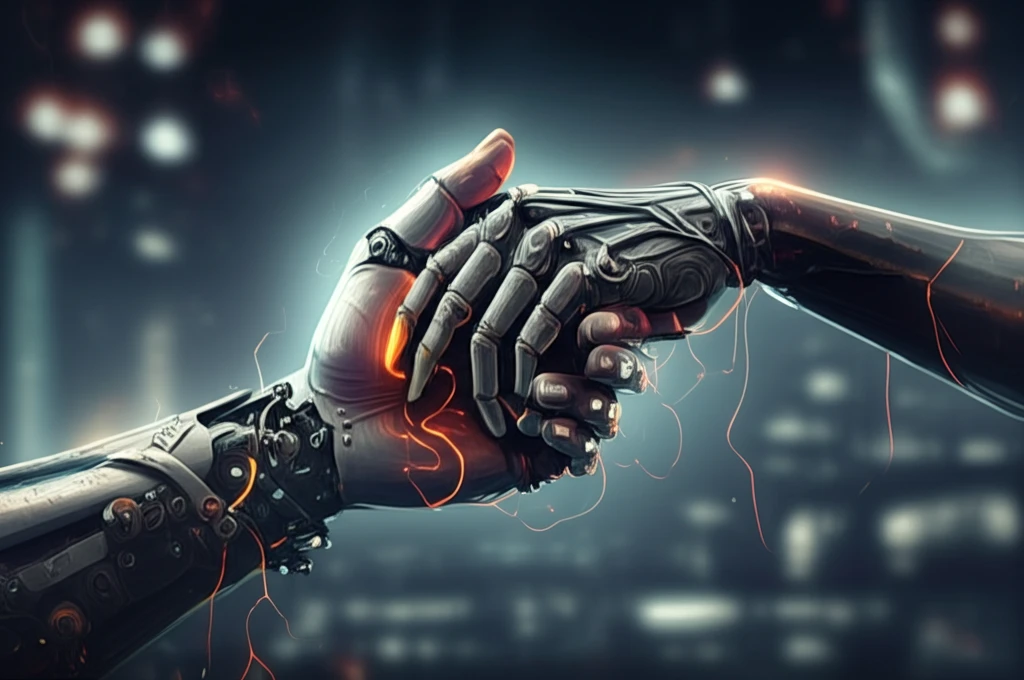
The first step in creating a comfortable exoskeleton is understanding the hand's stiffness landscape. Researchers at the University of Texas at Austin, the University of Washington, and Oculus & Facebook have undertaken detailed studies to map the spatial stiffness distribution of the hand dorsum. Their approach involves a combination of experimental measurements and computational modeling.
- The stiffness of the hand dorsum varies significantly across its surface.
- The regions above the metacarpal bones are generally stiffer than the areas in between.
- Increasing grasp force leads to an increase in measured dorsum stiffness.
The Future of Comfortable Robotics
This research marks a significant step towards creating more comfortable and usable hand exoskeletons. By understanding and adapting to the hand's natural stiffness variations, engineers can minimize pressure points and improve the overall user experience. The implications extend beyond exoskeletons, potentially informing the design of other wearable devices, prosthetic sockets and any application where a close human-machine interface is critical. As robotics and wearable technology become increasingly integrated into our lives, ensuring user comfort will be paramount to their success.