Safer Robots, Happier Humans: How Sensor-Free Tech Could Revolutionize Workplace Safety
"Unlock the potential of collaborative robots with groundbreaking sensor-less force detection for safer, more intuitive human-robot interactions."
Imagine a factory floor where robots and humans work side-by-side, seamlessly collaborating to assemble products, move materials, and perform intricate tasks. This vision of human-robot collaboration (HRC) is rapidly becoming a reality, promising increased efficiency, improved safety, and a more engaging work environment. But to truly unlock the potential of HRC, we need robots that can sense and respond to their human partners in a safe and intuitive way.
Traditionally, achieving this level of responsiveness has required equipping robots with a variety of external sensors, such as force/torque sensors, tactile sensors, and vision systems. These sensors provide robots with the data they need to detect human presence, understand human intent, and react appropriately to unexpected contact. However, adding these sensors can be costly, complex, and difficult to integrate into existing robotic systems.
Now, a groundbreaking new approach is emerging that eliminates the need for external sensors altogether. This sensor-less force detection technology uses sophisticated algorithms and dynamic models to allow robots to "feel" their environment and detect external forces without relying on additional hardware. This innovative approach promises to make collaborative robots more accessible, affordable, and adaptable, paving the way for a new era of human-robot collaboration.
Why Sensor-less Force Detection is a Game-Changer for Industrial Robots
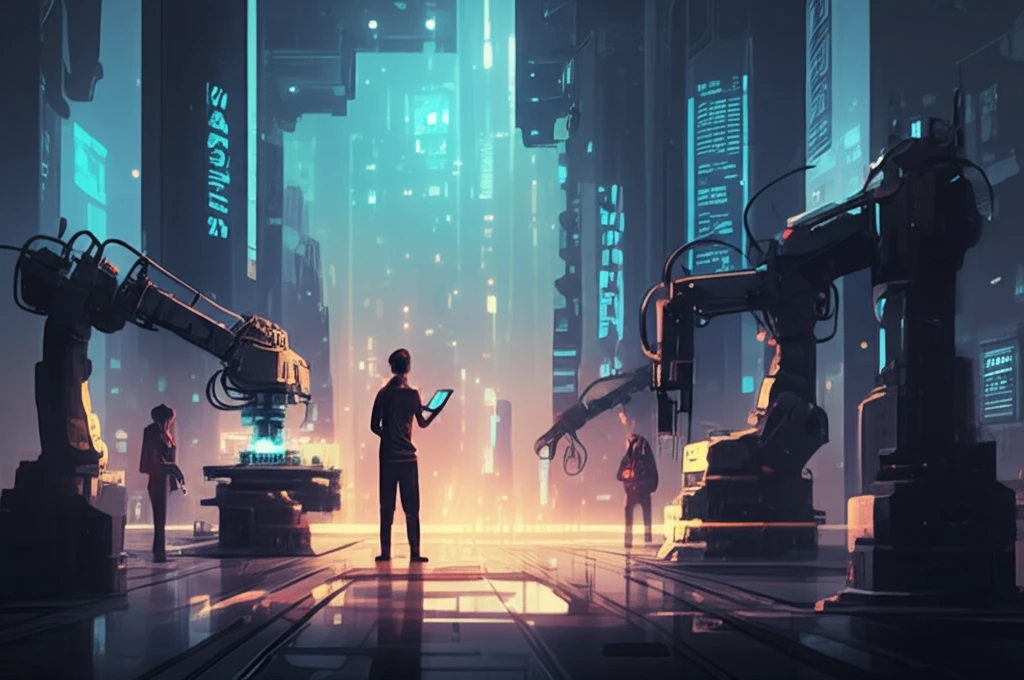
The core idea behind sensor-less force detection is to leverage the robot's existing internal sensors – such as joint position sensors and actuator current/torque sensors – to infer information about external forces acting on the robot. By analyzing the data from these sensors in conjunction with a detailed dynamic model of the robot, it's possible to estimate the magnitude and direction of external forces without the need for dedicated force sensors.
- Dynamic Modeling: A detailed dynamic model of the robot is created, capturing its inertial properties, friction characteristics, and other relevant parameters.
- Parameter Identification: The parameters of the dynamic model are identified using advanced algorithms and experimental data.
- Torque Residual Analysis: The difference between the predicted torque (based on the dynamic model) and the measured torque (from the robot's internal sensors) is analyzed to estimate external forces.
- Threshold Detection: A threshold is set to distinguish between normal operating forces and external forces that may indicate human contact.
The Future of Human-Robot Collaboration is Sensor-Free
Sensor-less force detection technology has the potential to revolutionize human-robot collaboration, making industrial robots safer, more adaptable, and more accessible. By eliminating the need for external sensors, this innovative approach reduces costs, simplifies integration, and opens up new possibilities for collaborative manufacturing, assembly, and other industrial applications. As the technology continues to develop and mature, we can expect to see sensor-less force detection playing an increasingly important role in the future of human-robot collaboration, creating safer and more efficient workplaces for everyone.