Runs Rules-Based Control Charts: A Simpler Way to Ensure Quality
"Learn how to use runs rules with control charts for effective quality control, even when you don't know all the details."
Imagine you're running a small business that produces organic skincare products. Every batch needs to be just right to maintain your brand's reputation and keep customers happy. But sometimes, things go wrong. Maybe the consistency is off, or the scent isn't quite perfect. That's where control charts come in. These charts help you visually track your production process and spot when something is out of the ordinary. But what if you don't know exactly what 'normal' looks like? What if you're still learning the ropes and figuring out the ideal parameters for your products? That's where runs rules-based control charts can be a game-changer.
Traditional control charts often rely on having precise knowledge of your process parameters, like the average weight of a product or the standard deviation of its purity. However, in many real-world situations, this information isn't readily available. You might be dealing with a new process, changing raw materials, or simply lacking the resources to conduct extensive data analysis. In these cases, estimating the parameters becomes necessary, but it can also introduce additional uncertainty and affect the reliability of your control chart.
This article will guide you through a simpler approach to quality control using runs rules-based control charts. We'll break down the key concepts, explain how to construct and evaluate these charts, and show you how they can help you identify and address potential problems, even when you're operating with limited information. By the end, you'll have a practical understanding of how to use runs rules to maintain consistent quality in your processes, regardless of the challenges you face.
What Are Runs Rules and Why Are They Important?
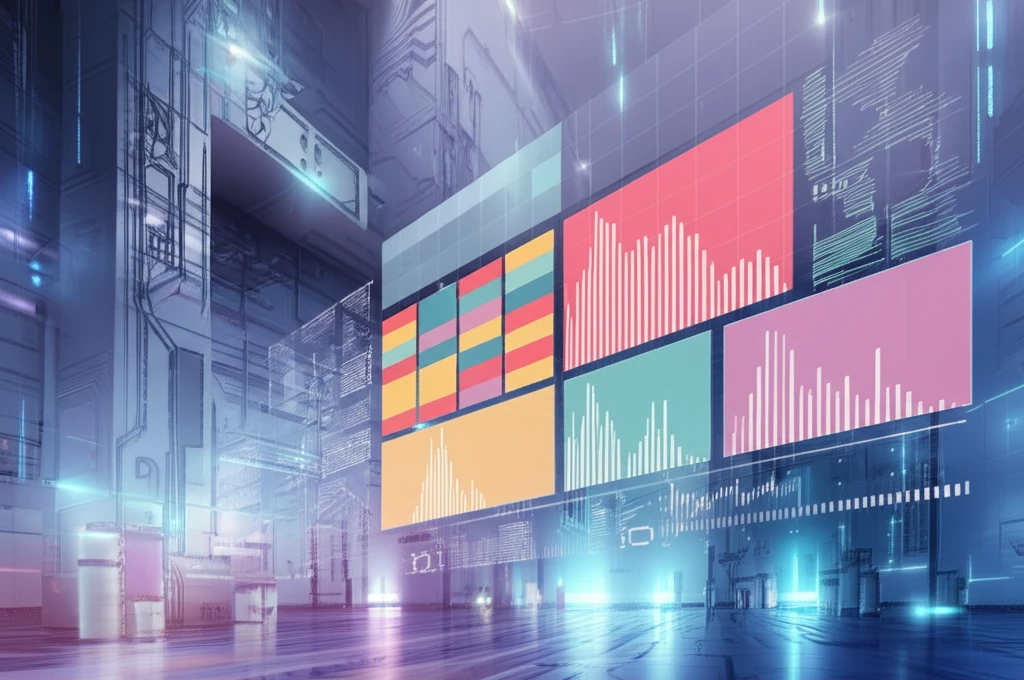
Runs rules, also known as sensitizing rules, are extra decision rules used alongside the basic one-point decision rule in Shewhart control charts. The one-point rule simply flags a process as out-of-control if a single data point falls outside the control limits. Runs rules, on the other hand, look for patterns or trends in the data, making them more sensitive to small-to-moderate shifts that might otherwise go unnoticed.
- Two out of three consecutive points fall beyond the 2-sigma limits: This rule suggests that a sustained shift is occurring, even if individual points aren't extreme enough to trigger the one-point rule.
- Four out of five consecutive points fall more than one standard deviation away from the center line: This indicates a potential trend or bias in the process.
- Eight consecutive points fall on one side of the center line: This rule is highly sensitive to even small shifts in the process average.
Taking Control of Quality
By understanding and applying runs rules-based control charts, businesses of all sizes can take proactive steps to maintain consistent quality and prevent costly problems. Whether you're a small skincare business just starting out or a large manufacturing facility with complex processes, these tools provide a simple yet powerful way to monitor your operations, identify potential issues, and ensure that your products and services consistently meet the highest standards.