Impact Damage in Composites: Can Guided Waves and Artificial Models Lead to Safer Structures?
"New research explores how guided wave-based inspection and experimental models can improve the detection of impact damage in composite materials, paving the way for enhanced structural health monitoring in aerospace and other industries."
Composite materials are increasingly used in various industries due to their high strength and stiffness-to-weight ratios. However, their susceptibility to hidden damage remains a significant concern. Traditional Non-Destructive Testing (NDT) methods, while mature, are often time-consuming and conducted at scheduled intervals, limiting real-time assessment of structural integrity. This is where Structural Health Monitoring (SHM) comes in, offering a continuous and improved approach to evaluating structural health.
SHM promises higher safety standards through automated systems that minimize human interaction during inspections. Studies have shown that effective SHM methods can reduce maintenance costs for aircraft fleets by over 30%. For example, extending the life of the Canadian Air Force's F-18 fleet by monitoring operational loads can save hundreds of millions of dollars. With the rising maintenance costs of aging aircraft estimated at over $10.4 billion worldwide annually, SHM is a crucial area of interest for the aerospace community.
Among the various SHM techniques, guided wave-based strategies stand out for their cost-effectiveness, speed, repeatability, and sensitivity to small damages. These strategies can inspect large structures and detect both surface and internal damage, making them a promising solution for ensuring the safety and reliability of composite structures.
How Can Guided Waves Help?
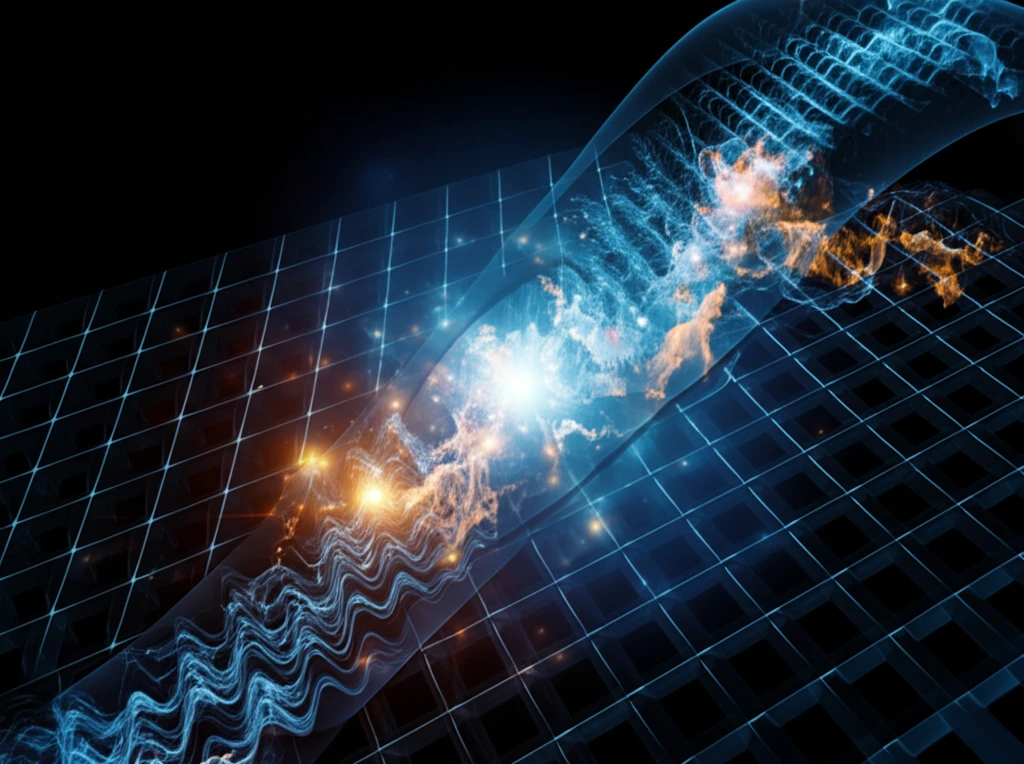
Guided wave techniques utilize piezoelectric transducers to generate waves that propagate through the material. These waves interact with any inhomogeneities, such as structural features or defects, and the resulting echoes provide valuable information about the material's condition. Damage significantly influences wave propagation, causing scattering effects like reflection, transmission, and mode conversion. This forms the basis for elastic wave-based damage identification, as different locations and severities of damage create unique scattering phenomena.
- Surface and Internal Damage Detection: Detects defects not visible externally.
- Piezoelectric Transducers: Generates and measures wave signatures.
- Wave Scattering Analysis: Assesses reflection, transmission, and mode conversion.
Toward Safer Composite Structures
The research concludes that mid-plane artificial delamination and impact damage exhibit distinct diffraction patterns, while non-mid-plane artificial delamination and low energy impact damage show similar directivity patterns. The reflection increases with frequency for both Teflon-type artificial delamination and real impact damage, whereas transmission decreases with increasing frequency. The study's findings offer valuable insights for designing effective SHM systems. Further research will focus on optimizing artificial damage models using Teflon tape to mimic realistic damage scenarios and improve guided wave scattering analysis.