Hydro Turbine Efficiency: How Fluid-Structure Interaction Can Revolutionize Renewable Energy
"Uncover the cutting-edge research that's making hydro turbines more efficient, sustainable, and reliable through advanced simulation techniques."
Hydro turbines harness the mechanical pressure of water to drive generators, producing clean, renewable energy. The force of the water against the turbine blades creates torque, which spins the turbine shaft and generates electricity. This process, while seemingly straightforward, involves complex interactions between the water flow and the turbine's structure. Traditionally, engineers have designed these turbines using a simplified approach, calculating mechanical stresses and deflections based on water pressure. However, this traditional method often overlooks a crucial element: the deformation of the turbine blades and its effect on the water flow itself.
Imagine a turbine blade bending slightly under the immense pressure of the water. This seemingly small bend can alter the shape of the blade, which in turn changes how the water flows around it. This change in water flow affects the pressure distribution on the blade, creating a feedback loop. Neglecting this feedback can lead to inaccuracies in design calculations and potentially compromise the turbine's performance and longevity. This is where fluid-structure interaction (FSI) simulation comes into play, offering a more comprehensive and accurate approach.
Recent research has explored the use of two-way coupled FSI simulations to analyze and optimize hydro turbine performance. This advanced simulation technique considers the interplay between the fluid (water) and the structure (turbine blade) allowing engineers to fine-tune designs for maximum efficiency and reliability. This article delves into the world of FSI simulations, exploring how they are applied to propeller turbines, the challenges involved, and the potential benefits for the future of hydropower.
Understanding Fluid-Structure Interaction (FSI) in Hydro Turbines
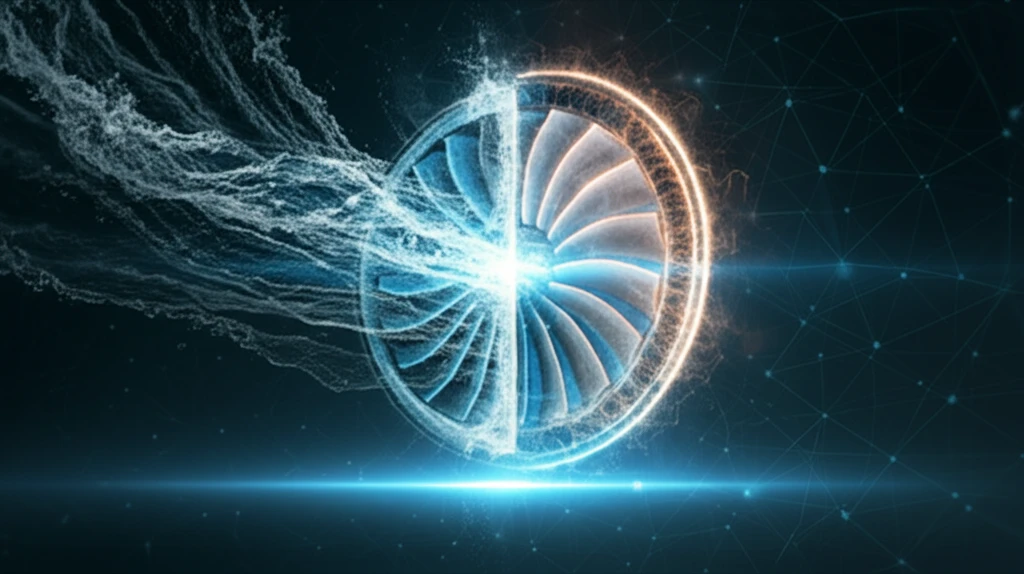
The fundamental principle behind hydro turbine operation is the conversion of water pressure into rotational energy. Water exerts force on the turbine blades, causing them to rotate and drive a generator. However, this force also induces stress and deformation in the blades. In the past, designers primarily used a one-way coupled approach. This involves calculating the water pressure on the blades using computational fluid dynamics (CFD) and then using that pressure as a load in a finite element analysis (FEA) to determine the stress and deflection. This method assumes that blade deformation does not significantly affect the water flow.
- Improved Accuracy: Accounts for the impact of blade deformation on water flow, leading to more precise performance predictions.
- Enhanced Design: Enables engineers to optimize blade shape and material properties for maximum efficiency and durability.
- Reduced Risk: Identifies potential structural weaknesses and prevents costly failures.
- Greater Efficiency: Contributes to the development of hydro turbines that extract more energy from the same amount of water.
The Future of Hydropower: Embracing FSI for Sustainable Energy
As the demand for clean, renewable energy continues to grow, hydropower will play an increasingly important role in meeting global energy needs. By embracing advanced simulation techniques like FSI, engineers can design and optimize hydro turbines for maximum efficiency, reliability, and sustainability. This technology will help realize a future where hydropower contributes significantly to a cleaner, more sustainable energy future for all.