Grasping the Future: How Optimized Robotic Grippers Are Changing Manufacturing
"Unlock precision and efficiency with advanced robotic gripper technology, revolutionizing industries from assembly lines to delicate handling tasks."
In today's fast-paced manufacturing landscape, the demand for precision, efficiency, and adaptability has never been higher. Traditional robotic systems, while capable, often lack the finesse required for handling delicate or irregularly shaped objects. This is where the innovative design of underactuated robotic grippers comes into play, offering a solution that mimics the dexterity of the human hand while enhancing operational speed and reliability.
Underactuated grippers represent a significant leap forward in robotic technology. Unlike fully actuated systems, which require a dedicated motor for each joint, underactuated grippers use a clever combination of mechanical linkages, springs, and a limited number of actuators to achieve complex grasping motions. This design results in a more compact, lightweight, and energy-efficient system that can conform to various object shapes, making it ideal for diverse applications.
This article delves into the fascinating world of underactuated robotic grippers, exploring their design principles, optimization techniques, and the transformative impact they are having on manufacturing processes. We'll uncover how researchers are leveraging advanced modeling and optimization algorithms to fine-tune these grippers for maximum performance, ensuring they can grasp the future of manufacturing with confidence.
What Makes Underactuated Grippers the Smart Choice for Modern Manufacturing?
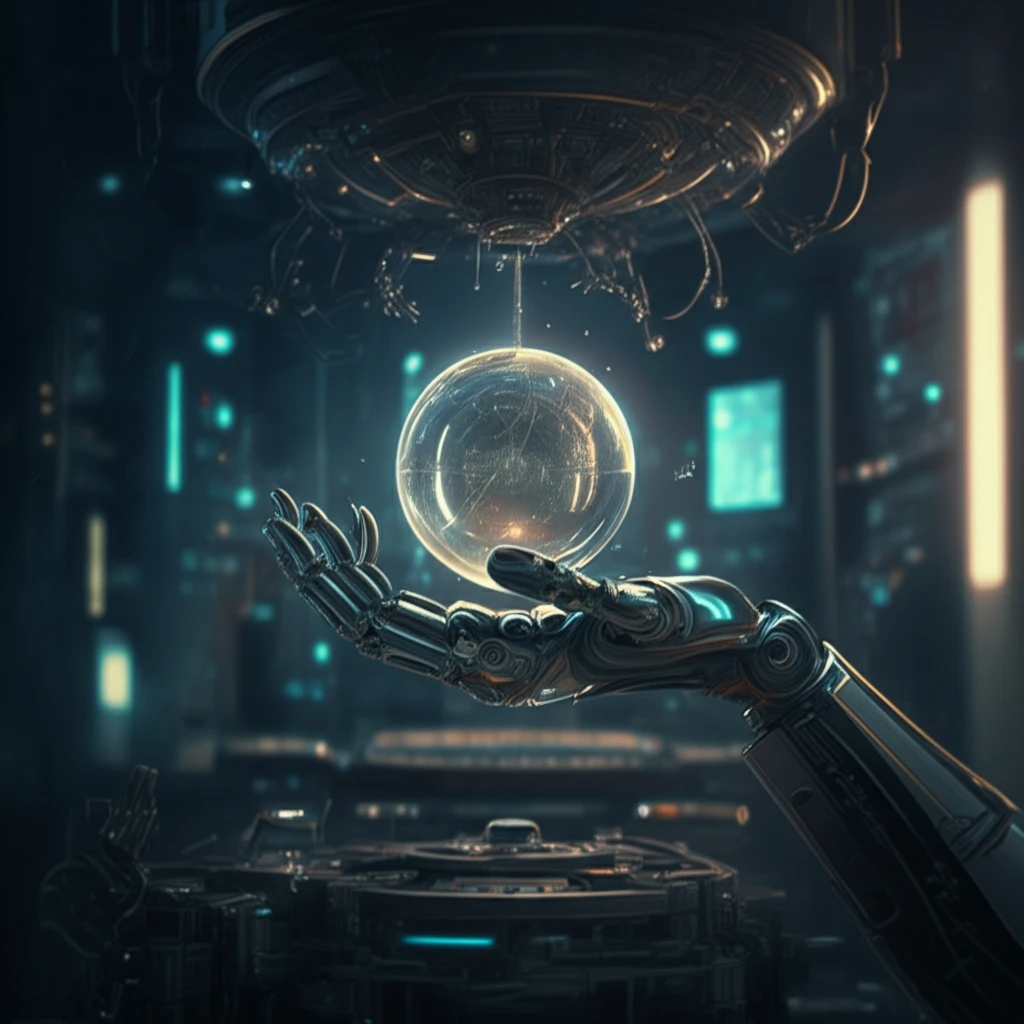
Traditional fully actuated robotic hands, while impressive in their capabilities, often come with significant drawbacks. Their complex designs translate into higher costs, increased weight, and more intricate control systems. Moreover, their rigid structure can make them unsuitable for handling fragile or irregularly shaped objects. Underactuated grippers offer a compelling alternative by addressing these limitations.
- Cost-Effectiveness: Fewer actuators translate into lower manufacturing and maintenance costs.
- Lightweight Design: Reduced complexity leads to a lighter gripper, enabling faster movements and reduced energy consumption.
- Adaptive Grasping: The mechanical design allows the gripper to conform to various object shapes, providing a secure and reliable grip.
- Simplified Control: Fewer actuators simplify the control system, making it easier to program and operate.
- Enhanced Durability: With fewer moving parts, underactuated grippers are generally more robust and reliable than their fully actuated counterparts.
Grasping the Opportunities Ahead
The development and optimization of underactuated robotic grippers represent a significant step toward more flexible, efficient, and cost-effective manufacturing processes. As research continues and new optimization techniques emerge, these grippers are poised to play an increasingly important role in shaping the future of automation. From delicate handling of fragile components to robust grasping of irregularly shaped objects, underactuated grippers are proving their versatility and adaptability, making them an indispensable tool for manufacturers seeking to enhance their operations and stay ahead in a competitive market.