Friction Stir Welding: Is Water the Key to Stronger, More Reliable Joints?
"A comparative study reveals how water-assisted friction stir welding can significantly improve the integrity of aluminum alloy joints, offering new possibilities for manufacturing and engineering."
Friction stir welding (FSW) has emerged as a game-changing technique in the world of materials joining. Unlike traditional welding methods that rely on melting materials together, FSW uses a solid-state process, which means the materials aren't melted. A rotating tool generates friction and heat, plasticizing the metal and creating a robust joint. This method is particularly effective for aluminum alloys, known for their widespread use in industries ranging from aerospace to automotive.
However, FSW isn't without its challenges. The high temperatures involved can lead to undesirable microstructural changes, weakening the joint. To combat this, researchers have explored various modifications to the FSW process, one of the most promising being underwater friction stir welding (UFSW). By submerging the welding area in water, engineers can better control the heat, leading to improved mechanical properties.
Recent research has focused on comparing FSW and UFSW techniques, specifically using AA-5754 aluminum alloy. This alloy is commonly used due to its excellent corrosion resistance and strength. The study, titled 'Friction stir welding of AA-5754 in water and air: a comparative study,' delves into how these two methods affect the microstructure and mechanical properties of the welded joints, providing valuable insights for optimizing welding processes.
FSW vs. UFSW: Understanding the Key Differences and Benefits
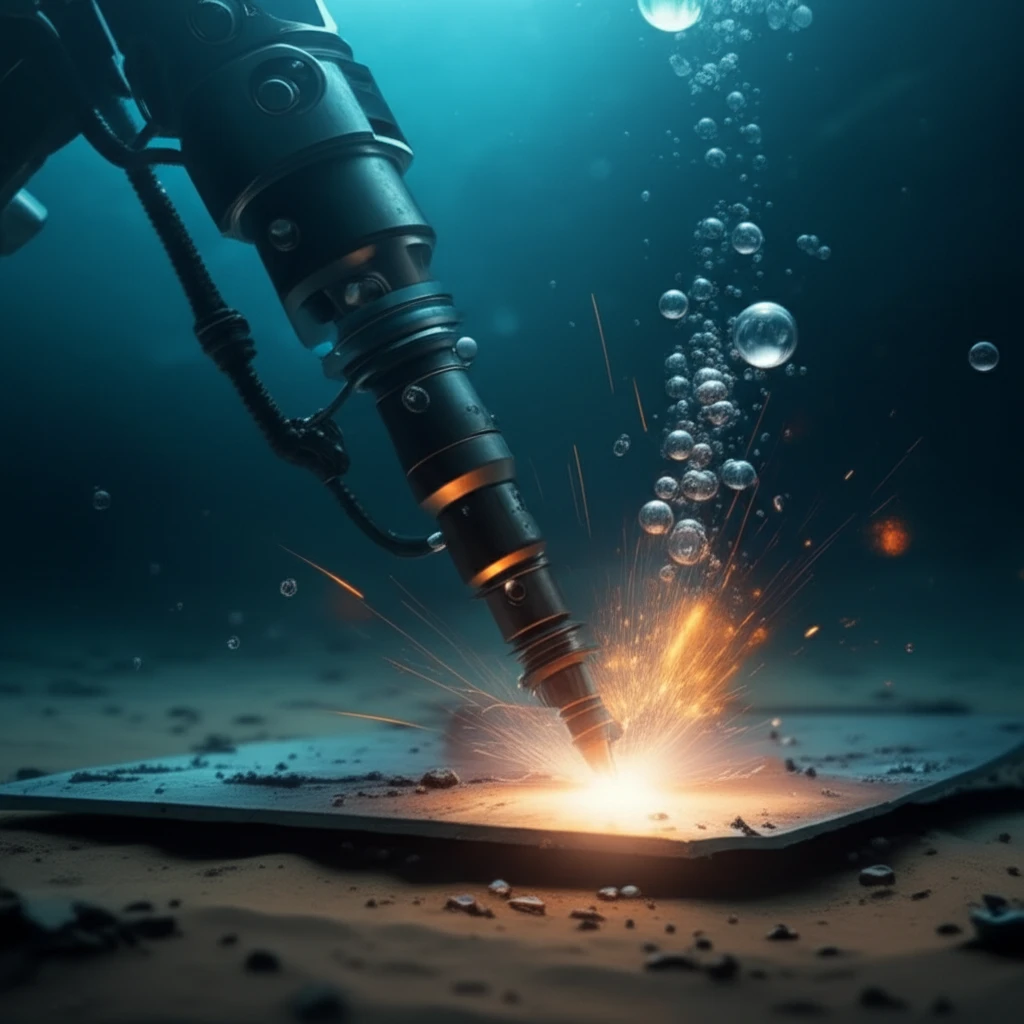
The core of the study involves a detailed comparison between conventional FSW performed in air and UFSW, where the welding process occurs underwater. The researchers varied the rotational speeds of the welding tool to observe the effects on the resulting joints. One of the most significant findings was that UFSW produced defect-free joints across different rotational speeds, while FSW in air resulted in defects at higher speeds (specifically at 1120 rpm).
- Enhanced Microstructure: UFSW results in finer and more uniform grains within the stir zone (SZ), the area most affected by the welding process. This fine-grained structure contributes to improved strength and durability.
- Superior Mechanical Properties: Joints created with UFSW exhibit better tensile strength and microhardness compared to those made with FSW in air. This means the UFSW joints can withstand greater forces and are more resistant to wear and tear.
- Reduced Thermal Impact: The water cooling in UFSW minimizes the heat-affected zone (HAZ), reducing undesirable changes in the material's properties adjacent to the weld.
The Future of Welding: Why UFSW Could Be the Next Big Thing
The research clearly indicates that underwater friction stir welding offers significant advantages over traditional FSW methods, especially for aluminum alloys like AA-5754. By providing better heat management, UFSW leads to stronger, more durable joints with fewer defects. As industries continue to seek more efficient and reliable welding techniques, UFSW stands out as a promising solution that could revolutionize manufacturing and engineering applications.