Decoding Steel Fatigue: How Acoustic Emission Reveals Hidden Damage
"Uncover the secrets of material degradation. Learn how acoustic emission techniques are revolutionizing structural health monitoring and ensuring the safety of aging infrastructure."
In industries where high-pressure equipment operates relentlessly, the integrity of materials is paramount. Carbon and ferritic alloy steels, the workhorses of these environments, face constant stress, temperature variations, and corrosive agents. Over decades, these factors can lead to hidden technological defects, compromising structural integrity and raising the specter of catastrophic failures.
Traditional methods of assessing material health often involve invasive procedures that halt operations and can be costly. However, a groundbreaking approach known as acoustic emission (AE) offers a non-destructive, real-time solution for monitoring material degradation. AE acts as a sensitive 'listening' device, capturing the faint sounds emitted by materials as they undergo stress and change at the microstructural level.
This article explores how AE, coupled with in-situ microscopic investigations, provides unprecedented insights into the tensile damage of degraded carbon steel and ferritic alloy-steel. By understanding the correlation between AE signals and material damage, industries can develop proactive strategies to prevent failures, extend equipment lifespans, and ensure operational safety.
What is Acoustic Emission (AE) and Why is it Important?
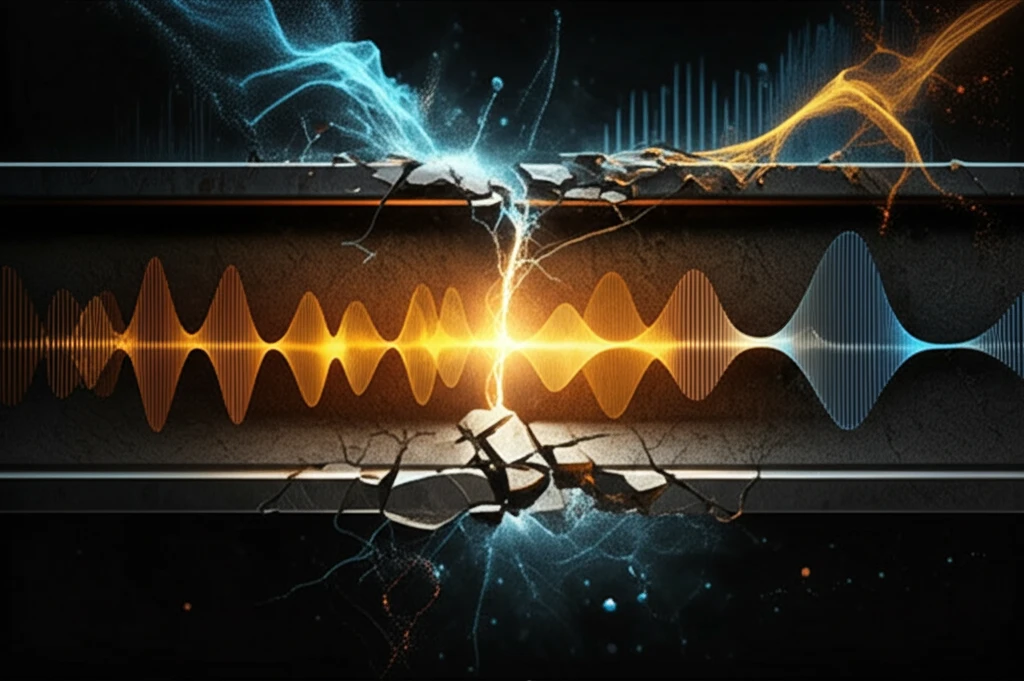
Acoustic emission (AE) is a passive, non-destructive testing (NDT) technique that detects and analyzes the transient elastic waves generated within a material when it undergoes deformation, fracture, or phase changes. Think of it as 'listening' to the material as it experiences stress.
- Real-Time Monitoring: AE provides immediate feedback on material condition, allowing for timely intervention.
- High Sensitivity: AE can detect subtle changes at the microstructural level, often before they become visible or lead to significant damage.
- Non-Invasive: AE doesn't disrupt operations, enabling continuous monitoring of equipment under normal working conditions.
- Versatile Applications: AE is applicable across various industries, from aerospace and automotive to civil engineering and petrochemicals.
The Future of Structural Health Monitoring
As industries grapple with aging infrastructure and the need for enhanced safety and efficiency, acoustic emission technology offers a compelling solution. By combining AE with advanced analytical techniques and in-situ microscopy, engineers can unlock a deeper understanding of material behavior and develop proactive strategies to prevent failures. The research marks a significant step toward a future where structural integrity is continuously monitored, ensuring the safety and reliability of critical infrastructure.