Crash Course: How Car Materials Impact Safety and Fuel Efficiency
"Discover how CFRP and aluminum tubes perform under multiple impacts, ensuring safer vehicles for everyone."
In the quest for safer and more fuel-efficient vehicles, automotive engineers are constantly exploring innovative materials and designs. Lightweight materials like carbon fiber reinforced plastics (CFRP) and aluminum are increasingly used in car manufacturing to enhance energy absorption and reduce overall weight. This push towards lighter vehicles not only improves fuel efficiency but also plays a crucial role in mitigating crash impact forces, thus enhancing passenger safety.
Vehicle pileups, unfortunately a common occurrence on today's roads, present a unique challenge for automotive safety. During these multi-impact events, a vehicle's front and back rails are subjected to a series of collisions, accumulating plastic deformation and progressive folding. Understanding how different materials respond under these repeated impacts is crucial for designing vehicles that can effectively manage crash energy and protect occupants.
Recent research has focused on understanding the impact response and residual properties of thin-walled CFRP and aluminum tubes, key structural components in vehicle design. By subjecting these materials to multiple axial impacts, scientists can simulate real-world crash scenarios and gain insights into their energy absorption capabilities and post-impact behavior. This knowledge is invaluable for optimizing vehicle structures to ensure maximum safety and reliability.
Understanding Crash Dynamics: CFRP vs. Aluminum
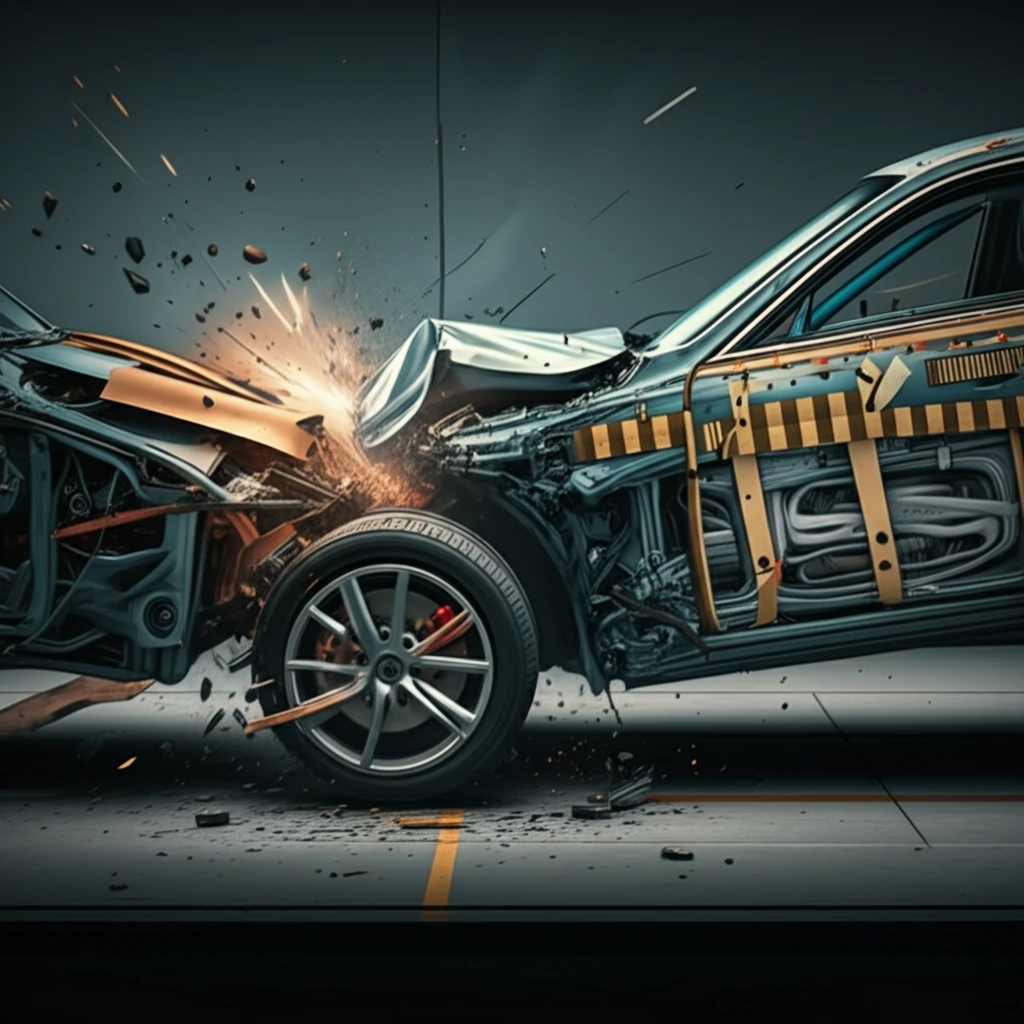
A recent study explored the impact responses and residual properties of thin-walled CFRP and aluminum tubes under multiple axial impacts. The researchers subjected the tubes to five repeated impacts with the same energy, evaluating the effect of repeated impacts. Crushing tests were then conducted to explore the post-impact residual behavior of the materials.
- CFRP Tubes: Exhibited progressive end crushing modes under repeated dynamic impacts. These tubes showed the highest specific energy absorption (SEA) during the first impact, followed by similar SEA values in subsequent impacts.
- Aluminum Tubes: Displayed a stable progressive folding mode. The SEA of aluminum tubes fluctuated with the number of repeated impacts, correlating with the formation of different folds.
- Residual Properties: Quasi-static crushing tests showed that the residual SEAs of both CFRP and aluminum tubes were not significantly affected by the number of impacts, varying by only about 5% after five repetitive impacts.
The Future of Vehicle Safety: Material Innovations
The study underscores the importance of material selection in enhancing vehicle safety and crashworthiness. By understanding the unique properties of materials like CFRP and aluminum under various impact conditions, engineers can design safer, more efficient vehicles. As automotive technology advances, continued research into material behavior will pave the way for even greater improvements in vehicle safety, reducing the risk of injuries and fatalities on the road.