Beyond Steel: How Advanced Alloys Are Shaping the Future of Everything
"Explore the innovative world of tungsten-zirconium dioxide composites and their groundbreaking impact on industries from aerospace to medicine, and how alloy advancements are transforming the tech landscape."
In a world hungry for materials that can withstand ever-increasing demands, the spotlight is on advanced alloys. These aren't your grandfather's metals; we're talking about sophisticated blends engineered at the atomic level to deliver unprecedented performance. From the scorching heat of rocket engines to the corrosive depths of the ocean floor, these materials are crucial.
One alloy garnering significant attention is the tungsten-zirconium dioxide (W-ZrO2) composite. This material combines the high melting point and strength of tungsten with the enhanced stability and fracture resistance of zirconium dioxide. The result? An alloy that can withstand extreme temperatures and pressures, making it ideal for applications where failure isn't an option.
This article delves into the fascinating science behind W-ZrO2 alloys, exploring how different preparation techniques influence their microstructure and mechanical properties. Understanding these relationships is key to unlocking the full potential of these materials and tailoring them for specific, high-performance uses.
What Makes W-ZrO2 Alloys a Game Changer?
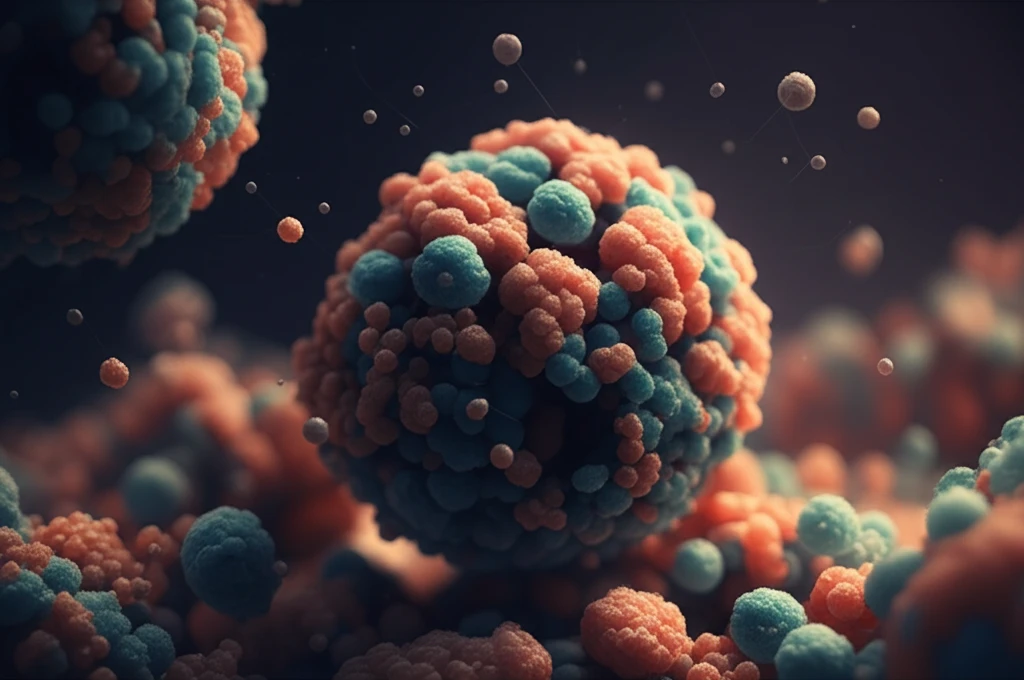
Tungsten alloys have long been prized for their exceptional properties, including a high melting point, impressive hardness, and remarkable wear resistance. These characteristics make them indispensable in various sectors, such as aerospace, nuclear energy, and defense. However, pure tungsten suffers from brittleness, limiting its applications. This is where zirconium dioxide comes in, acting as a strengthening agent and improving the alloy's overall performance.
- Azeotropic Distillation: This method is used to ensure a homogenous mixture of tungsten and zirconium dioxide at the nanoscale level. By carefully controlling the pH of the initial solutions, scientists can influence the size and distribution of the particles, leading to enhanced alloy properties.
- Sintering Techniques: Different sintering methods, including conventional sintering, hot isostatic pressing (HIP), and vertical sintering, dramatically affect the density and strength of the final alloy. HIP, for example, applies high pressure and temperature simultaneously, resulting in a denser, more robust material.
- Mechanical Alloying: This technique involves high-energy ball milling to create a uniform blend of tungsten and zirconium dioxide powders. The resulting powder is then consolidated using methods like HIP to produce a dense, strong alloy.
The Future is Forged in Innovation
As industries continue to push the boundaries of what's possible, advanced alloys like W-ZrO2 are poised to play an increasingly critical role. Whether it's enabling more efficient energy production, creating lighter and stronger aircraft, or developing advanced medical implants, these materials are at the forefront of innovation. Continued research and development in alloy preparation techniques will unlock even greater potential, paving the way for a future where materials are no longer a limiting factor.