Unlocking the Secrets of Wood Panel Ductility: How to Design Stronger, Safer Structures
"Engineers are rethinking wood panel construction to maximize flexibility and resilience. Discover how new approaches can protect buildings from collapse."
In modern construction, wood panels are a popular choice for their sustainability and aesthetic appeal. However, ensuring the structural integrity of these panels, especially in the face of extreme loads, requires a deep understanding of their ductility. Ductility, in simple terms, is the ability of a material to deform significantly before it breaks. For wood panels, this means they can bend and flex under stress, absorbing energy and preventing sudden collapses.
Traditionally, engineers have used the shear field girder method to model wood panel constructions. This method simplifies the panel into a series of ideal shear fields, making calculations more manageable. However, this approach often overlooks the complex, non-linear behavior of wood, particularly the interaction between the panel's sheathing and its supporting ribs. This simplification can lead to underestimations of the panel's true ductility, potentially compromising the safety of the structure.
Recent research is challenging these traditional methods, exploring the nuances of wood panel ductility to create more resilient and reliable designs. By understanding the factors that contribute to a panel's ability to deform without failing, engineers can develop construction techniques that enhance structural performance and improve overall safety.
What Makes Wood Panels So Ductile?
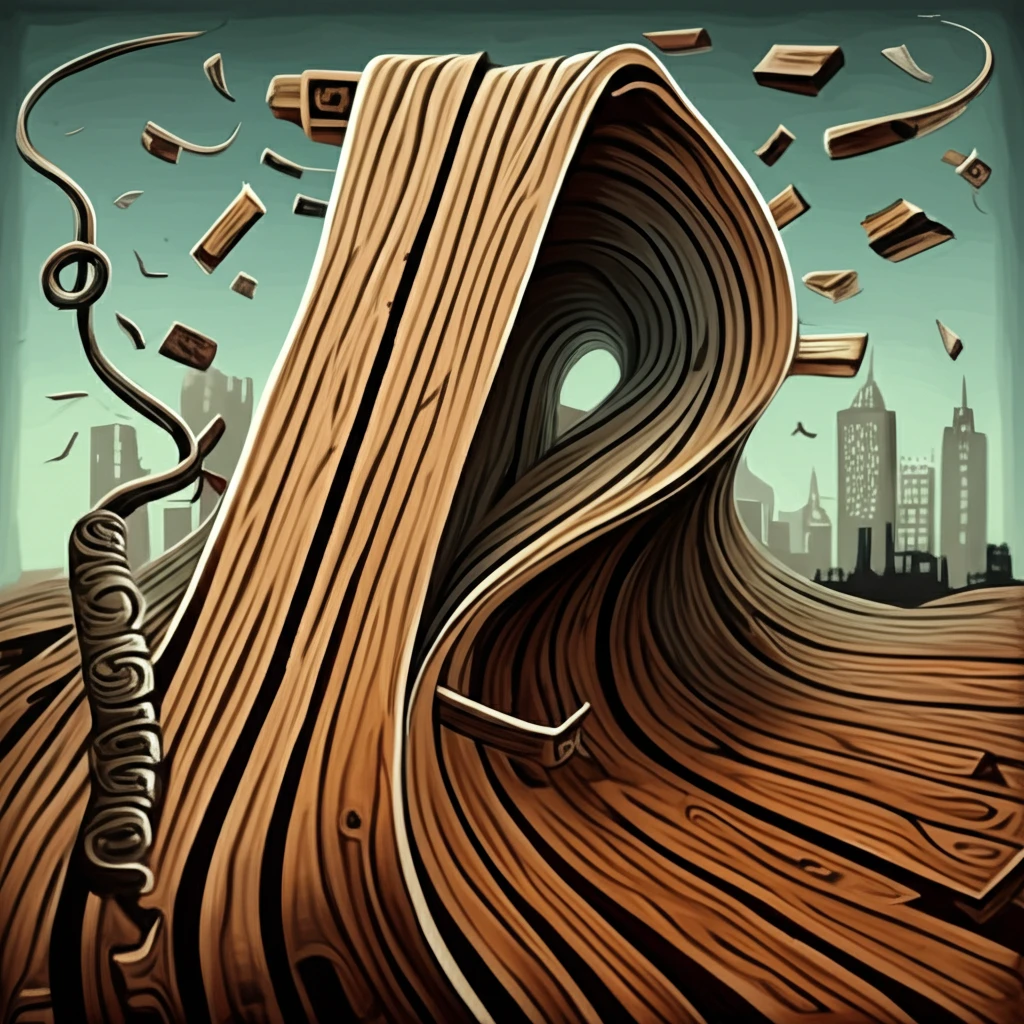
The inherent ductility of wood panels comes from their unique composite structure. Unlike homogenous materials like steel, wood panels consist of multiple components – the sheathing (the panel's surface) and the ribs (the supporting frame). These components are connected by various fasteners, creating a complex system that can absorb and distribute stress in ways that a simple shear field model cannot fully capture.
- Material Properties: Wood itself exhibits some degree of ductility, especially along the grain.
- Connection Flexibility: The fasteners used to connect the sheathing and ribs allow for controlled slippage.
- Composite Action: The interaction between the sheathing and ribs distributes stress.
- Energy Dissipation: The panel's ability to absorb and dissipate energy through deformation.
The Future of Wood Panel Design
As research continues to shed light on the complex behavior of wood panels, engineers are developing more sophisticated design methods that move beyond simplified shear field models. These advanced methods, often utilizing finite element analysis (FEA), allow for a more accurate representation of the panel's behavior, including the effects of free edges and non-linear material properties. By embracing these new approaches, the construction industry can unlock the full potential of wood panels, creating structures that are not only sustainable and aesthetically pleasing but also incredibly strong and resilient.