Unlocking Steel's Secrets: How Molecular Dynamics is Revolutionizing Materials Science
"Delve into the microscopic world of steel transformation and discover how cutting-edge simulations are paving the way for stronger, more resilient materials."
For decades, scientists and engineers have strived to understand the intricate behavior of materials at their most fundamental level. This pursuit is especially critical for materials like steel, which underpins countless industries from construction and automotive to aerospace and energy. Understanding how steel transforms at the atomic level can unlock pathways to creating stronger, more durable, and more efficient materials.
Traditional methods of studying these transformations often fall short. Experiments can only reveal so much, and theoretical models often simplify the complex reality. However, a revolutionary approach known as molecular dynamics (MD) simulation is changing the game. MD allows researchers to simulate the movement and interactions of individual atoms, providing an unprecedented view into the dynamic processes that govern material behavior.
A recent study published in the Canadian Metallurgical Quarterly highlights the power of MD in unraveling the mysteries of the austenite-to-ferrite transformation in pure iron – a key process in steelmaking. By simulating this transformation, researchers have gained valuable insights into the structure and orientation relationships of the nucleus interface, which ultimately determines the properties of the final steel product.
What is the Austenite-to-Ferrite Transformation and Why Does It Matter?
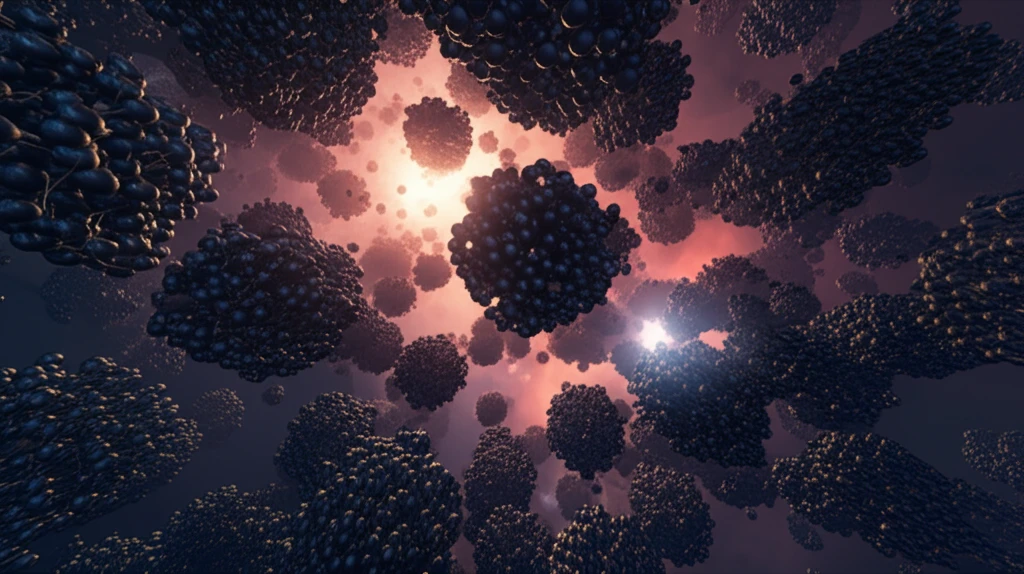
The austenite-to-ferrite transformation is a fundamental process in the production of steel. At high temperatures, iron exists in a face-centered cubic (FCC) structure called austenite (also known as gamma-iron). As the steel cools, it transforms into a body-centered cubic (BCC) structure called ferrite (or alpha-iron). This transformation dictates the steel's mechanical properties, such as strength, ductility, and toughness.
- Temperature: The rate of cooling significantly affects the microstructure of the resulting steel.
- Alloying Elements: Adding elements like carbon, manganese, and silicon can alter the transformation temperature and the resulting phases.
- Grain Boundaries: These interfaces between individual crystals act as nucleation sites for the new ferrite phase.
The Future of Steel Design: Atomic-Level Precision
Molecular dynamics simulations are not just a theoretical exercise; they have profound implications for the future of steel design and manufacturing. By providing a detailed understanding of the austenite-to-ferrite transformation, MD simulations empower materials scientists and engineers to design new alloys with tailored properties. This could lead to stronger, lighter, and more sustainable steel products for a wide range of applications. As computational power continues to increase, MD simulations will undoubtedly play an even greater role in the development of advanced materials, driving innovation across industries and shaping the future of engineering.