Unlocking Pump Efficiency: The Surprising Secret of Rotor-Stator Spacing
"Could Less Space Really Mean More Power in Axial Pumps? New Research Reveals the Optimal Gap for Peak Performance"
Axial pumps, those workhorses of fluid transport, are found everywhere from water treatment plants to sophisticated cooling systems. But how do you squeeze the most performance out of these vital machines? A key lies in a seemingly small detail: the gap between the rotating rotor and the stationary stator.
Think of it like tuning an engine. The rotor-stator interaction dictates how smoothly and efficiently energy is transferred to the fluid. Too much turbulence or poorly directed flow, and you're wasting power. That's why researchers are constantly digging into the nitty-gritty of pump design to find those marginal gains that add up to significant improvements.
New research is shedding light on how tweaking the axial spacing—the distance between the rotor and stator—can dramatically impact a pump's performance. This isn't just about abstract engineering; it's about real-world efficiency, potentially saving energy and resources across countless applications.
The Sweet Spot: How Axial Spacing Affects Pump Performance
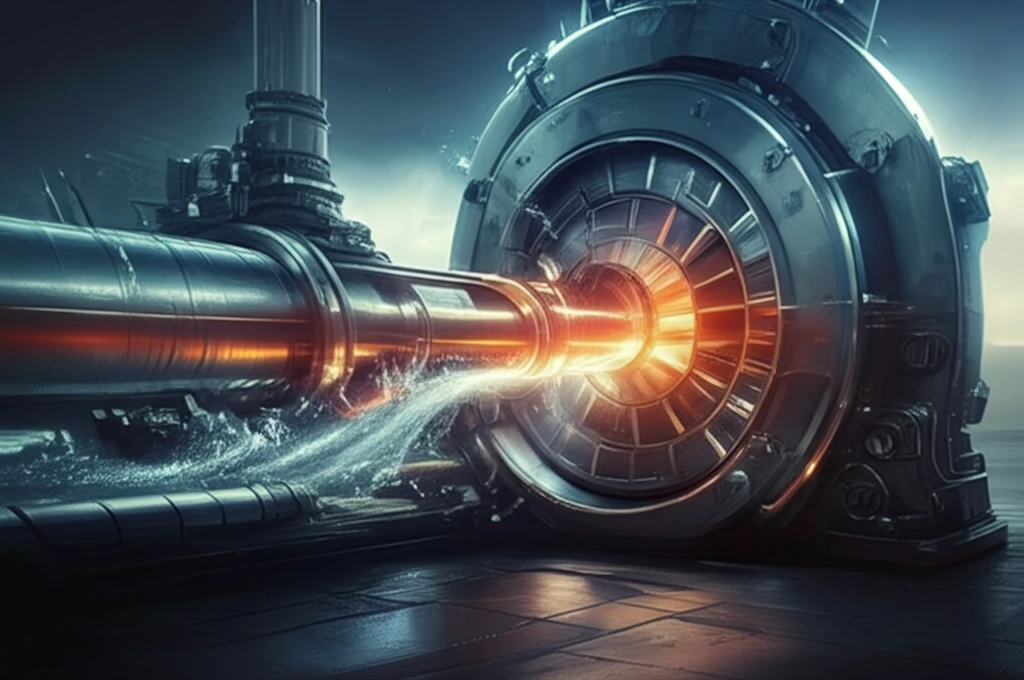
The core finding? Decreasing the axial spacing, especially at lower flow rates, can substantially boost a pump's hydraulic head—essentially, its ability to push fluid against pressure. This might seem counterintuitive, but the research, conducted using water as the working fluid, showed a clear trend: tighter spacing, better performance.
- Wake Effects: The wake from the rotor, the disturbed flow trailing behind its blades, significantly influences how water enters the stator.
- Incidence Angle: Closer axial spacing reduces the angle at which the flow hits the stator blades (the incidence angle).
- Flow Separation: By reducing the incidence angle, tighter spacing helps prevent flow separation, a phenomenon where the flow detaches from the blade surface, creating turbulence and energy loss.
Practical Implications: Designing for Peak Efficiency
This research provides valuable insights for engineers designing and optimizing axial pumps. While the ideal axial spacing will depend on the specific pump design and operating conditions, the study suggests that erring on the side of tighter spacing can lead to noticeable performance gains, particularly in applications where low flow rates are common. By carefully considering the rotor-stator interaction, it's possible to unlock new levels of efficiency and reduce energy consumption.