Unlocking Chip Secrets: A Guide to Backside Decapsulation for Failure Analysis
"Discover how mechanical decapsulation can revolutionize failure analysis in non-exposed die pad packages, ensuring accuracy and efficiency."
In today's fast-paced microelectronics industry, the demand for increasingly complex chips is ever-growing. With this complexity, however, comes a higher susceptibility to failures caused by external electrical stress or manufacturing defects. Identifying the root cause of these failures quickly and accurately is crucial for maintaining product quality and reliability.
One essential technique used in failure analysis is exposing the die backside, often achieved through chemical preparation. While effective, this method has significant drawbacks, especially when dealing with small, non-exposed die pad packages. The risk of over-etching copper leads with harsh chemicals like 65% Acid Nitric Fuming can hinder further electrical measurements, rendering the process ineffective.
This article explores an innovative solution: mechanical decapsulation. This alternative method offers a more controlled and precise approach to backside sample preparation, ensuring the copper leads remain intact and enabling accurate electrical measurements. Learn how this technique can revolutionize your failure analysis process and improve the overall effectiveness of your results.
The Problem with Chemical Etching
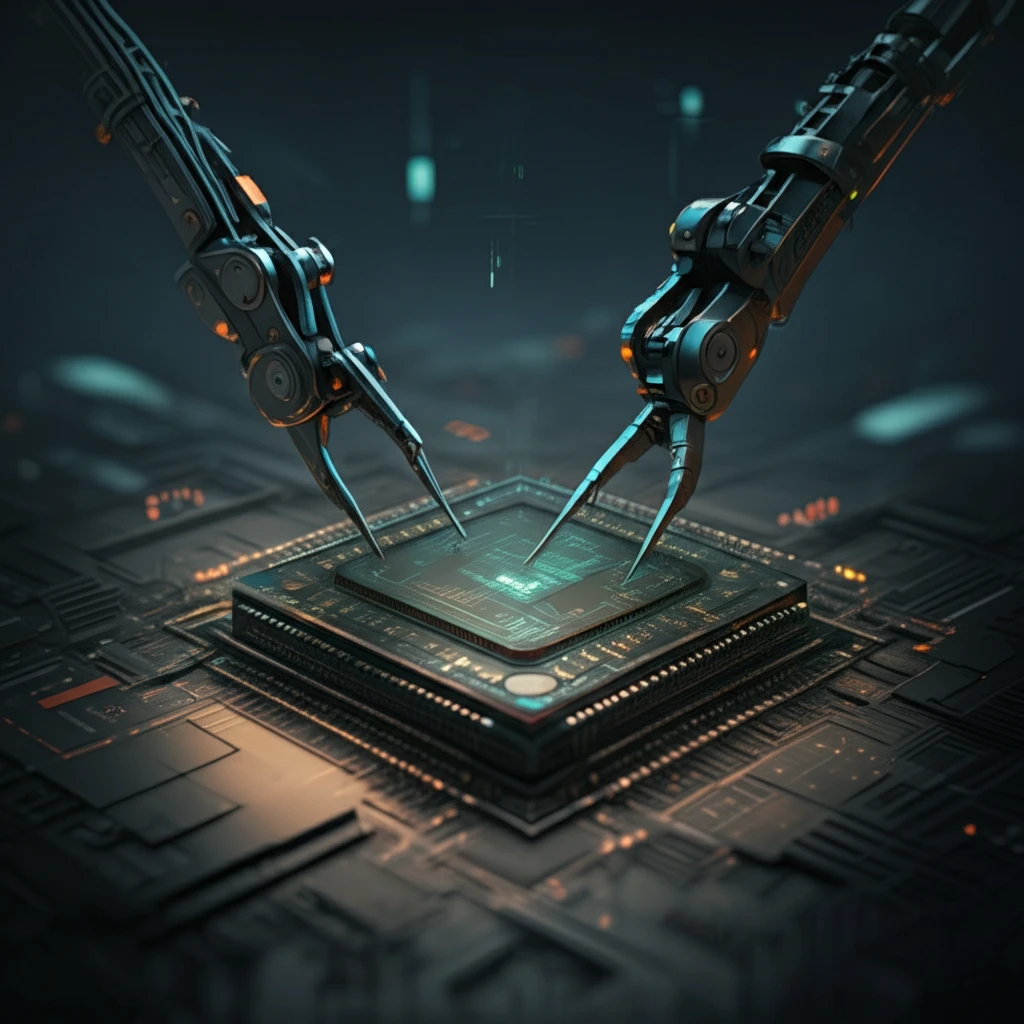
Traditional chemical etching has long been a standard practice for exposing the die backside. It's generally known for its speed and ability to deliver a clean surface. However, its application is not without challenges, especially when dealing with delicate packages. Small, non-exposed die pad packages, where the die is fully covered with mold compound, are particularly vulnerable.
- Copper Lead Damage: The acid can aggressively attack the copper leads, causing them to erode or even break.
- Measurement Hindrance: Damaged leads compromise the ability to perform accurate electrical measurements, a critical step in failure analysis.
- Limited Application: Chemical etching becomes unsuitable for package designs with large die pad areas and small lead areas due to this over-etching risk.
Embracing the Future of Failure Analysis
In conclusion, mechanical decapsulation presents a compelling alternative to chemical etching for backside sample preparation, particularly in non-exposed die pad package designs. By mitigating the risk of over-etching and preserving the integrity of copper leads, this technique ensures more reliable electrical measurements and enhances the overall effectiveness of failure analysis. As the microelectronics industry continues to advance, embracing innovative methods like mechanical decapsulation will be crucial for maintaining product quality, reducing failure rates, and driving continuous improvement.