Unlock Efficiency: Mastering Interior Permanent Magnet Synchronous Motors
"A Comprehensive Guide to Parameter Estimation for Peak Performance"
In today's fast-paced world, efficiency isn't just a buzzword—it's a necessity. From electric vehicles to high-performance servo drives, Interior Permanent Magnet Synchronous Motors (IPMSMs) are at the forefront of innovation. Their superior efficiency, high torque density, and wide speed range make them indispensable in various applications. But, to truly harness their power, you need a deep understanding of their parameters.
Think of an IPMSM as a finely tuned instrument. Just like a musician needs to understand their instrument to create beautiful music, engineers and technicians need to grasp the intricacies of IPMSM parameters to achieve optimal performance. This is where parameter estimation comes in—it’s the key to unlocking the full potential of these motors.
This article is your guide to mastering parameter estimation for IPMSMs. We'll break down complex concepts, explore cutting-edge techniques, and show you how to apply them in real-world scenarios. Whether you're an experienced engineer or a curious student, you'll gain valuable insights that can transform your approach to motor control.
The Inverse Problem Approach: A Deep Dive
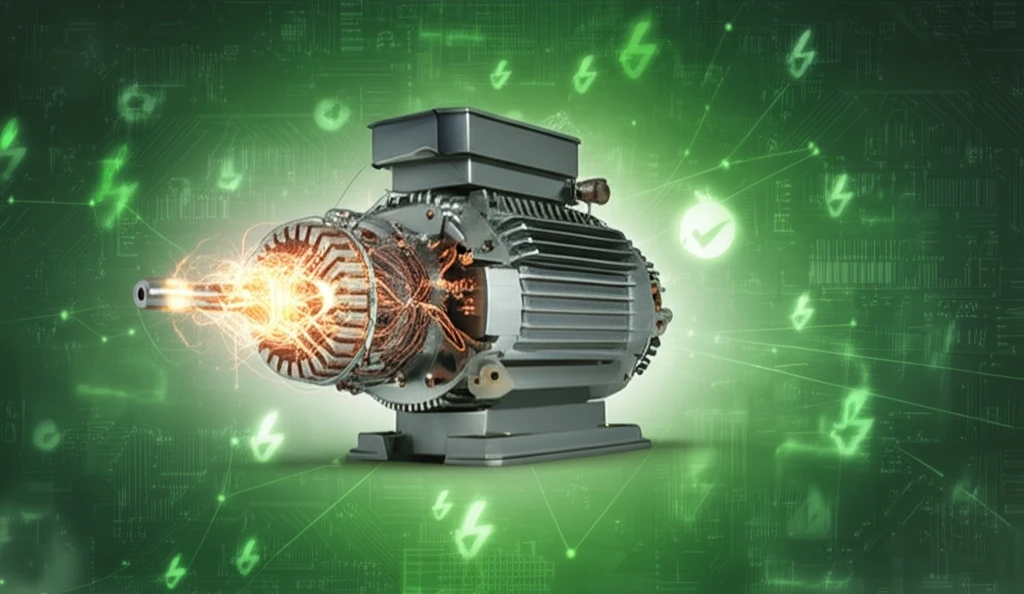
At the heart of efficient IPMSM control lies the accurate estimation of d- and q-axis parameters. These parameters are fundamental to vector control algorithms, enabling fast and precise responses. Traditionally, methods like Finite Element Analysis (FEM) have been used to determine IPMSM reactance. While accurate, FEM can be time-consuming. A faster alternative is the magnetic circuit modeling approach, which has been successfully applied to various electrical machines, including IPMSMs.
- Efficiency: Reduces computation time compared to traditional methods.
- Accuracy: Provides reliable parameter estimations for optimal motor control.
- Versatility: Applicable to a wide range of IPMSM applications.
- Practicality: Uses readily available measurements to compute the objective function.
Real-World Applications and Future Trends
The techniques discussed aren't just theoretical exercises—they have tangible real-world applications. From improving the energy efficiency of electric vehicles to enhancing the precision of industrial robots, accurate parameter estimation is crucial. As technology advances, the demand for even more efficient and reliable motor control systems will only increase. Embracing these innovative approaches will pave the way for a more sustainable and technologically advanced future.