Under Pressure: The Ultimate Guide to Preventing Buckling in Composite Beams
"Discover how advanced analytical models are revolutionizing the design of lightweight structures, ensuring safety and efficiency under compressive loads."
In today's world, the push for efficiency and sustainability is driving innovation in every sector. One area where this is particularly evident is in the construction and engineering of lightweight structures. These structures, often made from composite materials, offer a fantastic strength-to-weight ratio, reducing material costs and energy consumption. However, their very nature makes them susceptible to a phenomenon known as buckling, which can compromise their structural integrity. Understanding and mitigating buckling is therefore crucial for ensuring the safety and reliability of these modern designs.
Buckling, in simple terms, is what happens when a structural member subjected to compressive forces suddenly deforms or collapses. Think of pushing down on a thin ruler – at a certain point, it will bend or buckle. In complex composite beams, predicting exactly when and where buckling will occur is a significant challenge. Traditional methods often oversimplify the problem, leading to potentially unsafe designs. This is why advanced analytical models are so important.
Recent research introduces a holistic, closed-form analytical model designed to predict local buckling in thin-walled composite beams. This model considers the interactions between different parts of the beam, providing a more accurate and reliable prediction of buckling load. By understanding the science behind this model and its implications, engineers can create lighter, stronger, and more efficient structures for a wide range of applications.
What's the Big Deal About Buckling, Anyway?
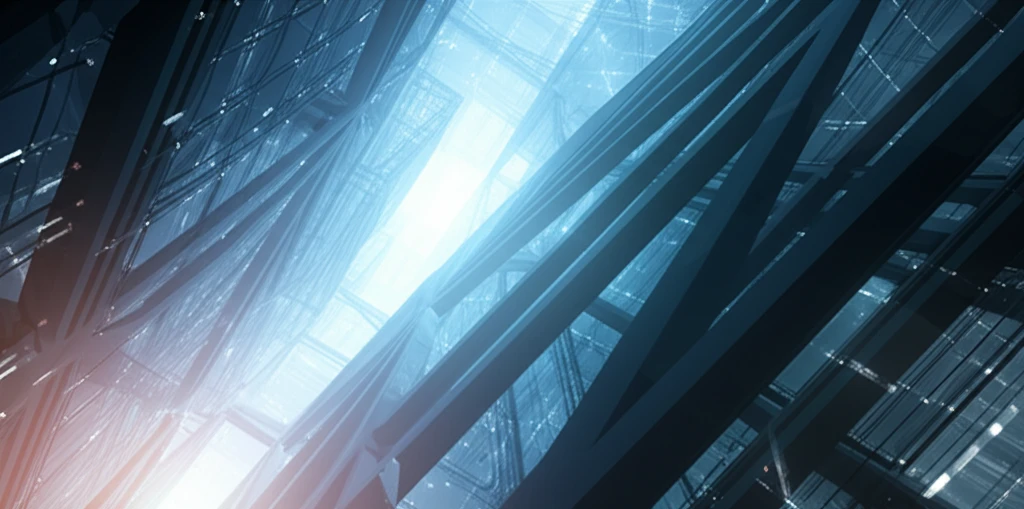
Imagine a bridge designed with lightweight composite beams. If these beams buckle under the weight of traffic or environmental stressors, the consequences could be catastrophic. Buckling isn't just about structural failure; it also affects performance and longevity. When a component buckles, even slightly, it can lead to:<ul> <li>Reduced Load Capacity: The structure can't bear the intended weight or stress.</li><li>Increased Stress Concentrations: Buckling can create localized areas of high stress, accelerating wear and tear.</li><li>Unpredictable Behavior: Buckled structures may behave erratically, making it difficult to assess their safety over time.</li><li>Costly Repairs: Addressing buckling issues often requires extensive repairs or even complete replacement of structural elements.</li></ul>
- Material Properties: The specific materials used in the composite (e.g., carbon fiber, fiberglass, resin type).
- Laminate Structure: How the layers of material are arranged (fiber orientation, stacking sequence).
- Beam Geometry: The shape and dimensions of the beam's cross-section (I-beam, C-channel, etc.).
- Support Conditions: How the beam is supported at its ends (simply supported, fixed, etc.).
- Loading Conditions: The type and magnitude of the compressive force applied.
What's Next for Lightweight Structures?
This new analytical model represents a significant step forward in the design of safe, efficient lightweight structures. By providing a more accurate and reliable way to predict buckling, it enables engineers to push the boundaries of innovation while ensuring structural integrity. This research paves the way for exciting advancements in various fields, from aerospace and automotive engineering to civil infrastructure and sustainable building design. As we continue to seek lighter, stronger, and more sustainable solutions, understanding and preventing buckling will remain a critical area of focus.