Tungsten Under Fire: Unveiling Microstructural Secrets for Fusion Energy
"How High-Flux Plasma Changes Tungsten and What It Means for the Future of Fusion Reactors"
Tungsten is a critical material in the quest for sustainable fusion energy, poised to be the workhorse in the International Thermonuclear Experimental Reactor (ITER) and future DEMO reactors. As the divertor material and protective coating for reactor walls, it endures extreme conditions. Understanding how tungsten behaves under intense heat and radiation is not just academic—it's key to making fusion power a reality.
Imagine the surface of a material enduring temperatures hotter than the sun, bombarded by high-energy particles. This is the reality for tungsten inside a fusion reactor. These conditions create thermomechanical stresses that lead to plastic deformation, ultimately causing cracks to form and spread. Understanding the breaking points of tungsten helps to ensure structural integrity and prevent reactor failures.
Beyond structural concerns, the interaction between tungsten and plasma affects how well the material retains harmful plasma components like tritium. If tritium isn't properly contained, it poses significant safety risks. The study of these microstructural changes is therefore not just about improving reactor performance; it's about ensuring the safe operation of future fusion power plants.
How Does High-Flux Plasma Change Tungsten's Microstructure?
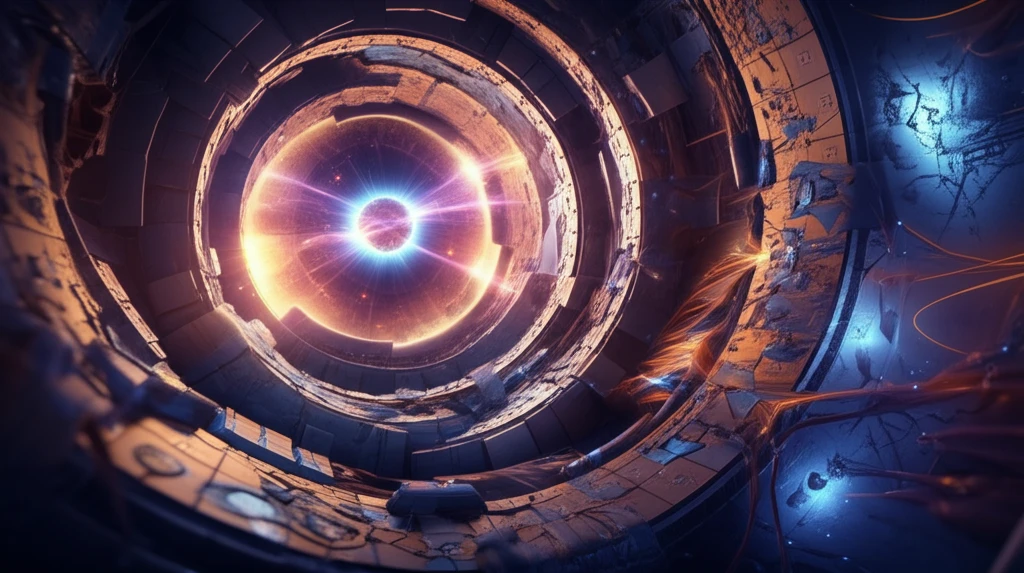
Researchers used transmission electron microscopy (TEM) to examine tungsten samples before and after exposure to high-flux plasma. Two types of samples were tested: annealed tungsten and heavily deformed tungsten. The goal was to see how the initial state of the material influenced the damage caused by the plasma.
- Increased Dislocation Density: The most significant change was a substantial increase in dislocation density near the surface of both annealed and deformed tungsten.
- Localized Deformation: The plastic deformation was deep and localized, meaning it didn't just affect the immediate surface but extended several micrometers into the material.
- Microstructural Recovery: At a depth of 10-15 micrometers, the material's microstructure began to resemble that of the unexposed bulk material, indicating a limit to the plasma's effect.
- Dislocation Loops: Dislocation loops, another form of crystal defect, were observed at depths of 2.5-5 micrometers, adding to the overall damage.
Why This Matters for the Future of Fusion
The research highlights the importance of understanding how plasma interacts with reactor materials at a microstructural level. By identifying the types of damage that occur and how deep they penetrate, scientists and engineers can develop strategies to mitigate these effects. This may involve developing new tungsten alloys, optimizing reactor designs, or refining plasma control techniques. The findings also underscore the need for continued research into deuterium diffusion and its impact on material properties under fusion conditions. As fusion research progresses, insights like these will be instrumental in making fusion energy a safe, reliable, and sustainable source of power.