The Secret to Stronger Titanium: How Alloy Composition Impacts Brazing Joints
"Unlock the potential of titanium-Ag28Cu brazing by understanding the influence of titanium alloy composition on joint strength and fracture behavior."
Titanium brazing is emerging as a key technique for assembling high-performance aerospace components. This method joins parts using a filler metal with a lower melting point than the base materials. It's particularly useful for creating complex geometries and joining dissimilar metals.
However, brazing titanium isn't without its challenges. The formation of brittle intermetallic phases at the joint interface can compromise the structural integrity. Overcoming these challenges is essential for ensuring the reliability and safety of aerospace structures.
Recent research has focused on understanding how the composition of titanium alloys influences the formation of these intermetallic phases and, consequently, the strength of the brazed joints. By carefully selecting and manipulating the alloy composition, engineers can optimize the brazing process to create stronger, more durable joints.
Decoding Interfacial Reactions: The Key to Brazing Titanium
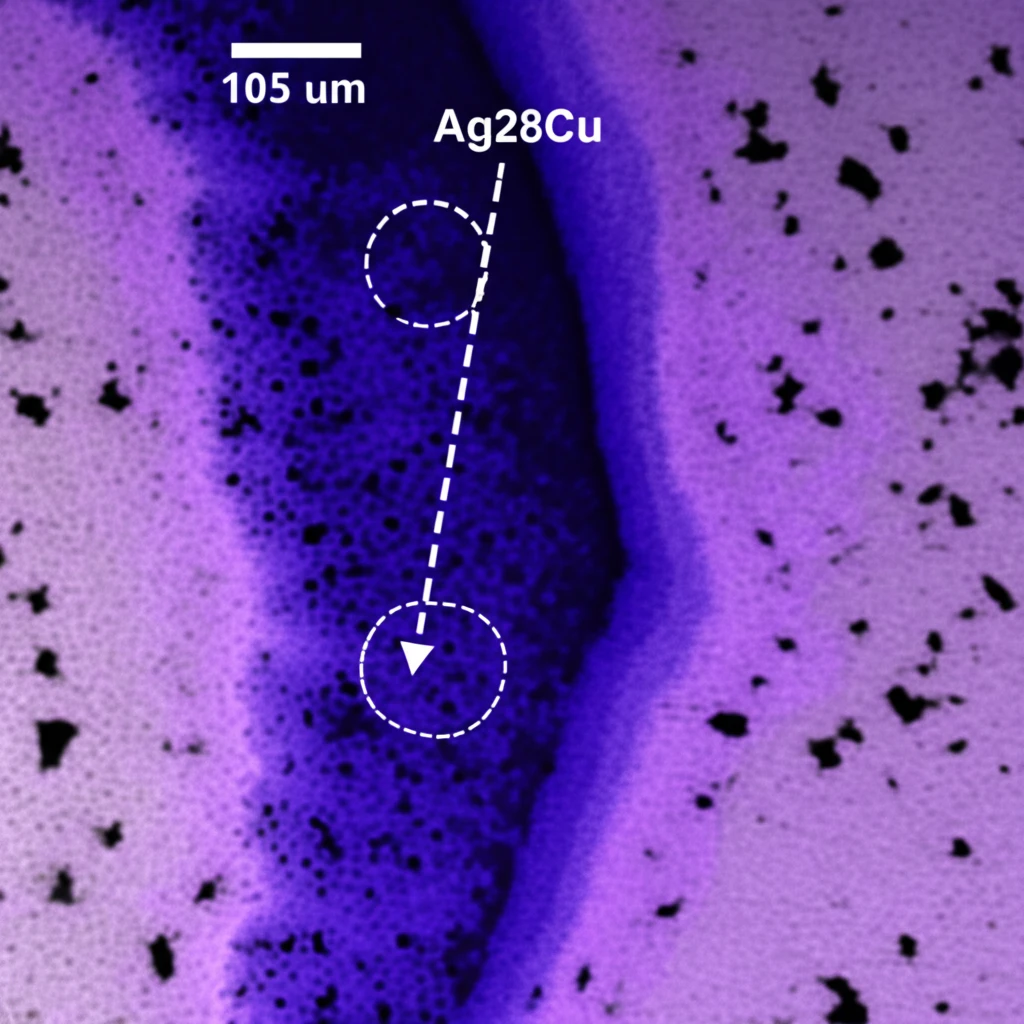
A recent study investigated the interphase formation in brazed joints made from various titanium alloys (Ti-CP2, Ti-CP4, Ti-6Al-4V, Ti-6Al-2Mo-4Zr-2Sn) and Ag28Cu. The findings revealed complex reactions leading to the formation of several intermetallic phases, including a Ti2Cu-TiCu boundary zone. The composition of the titanium alloys significantly influenced the resulting microstructures, which were characterized using advanced techniques like synchrotron X-ray microtomography.
- Complex reactions leading to intermetallic phase formation.
- Influence of titanium alloy composition on microstructure.
- Enhanced Ti2Cu-TiCu boundary strength with specific alloys.
- Changes in crack propagation paths for improved joint toughness.
Implications for Future Aerospace Manufacturing
These findings highlight the critical role of titanium alloy composition in determining the strength and fracture behavior of brazed joints. By carefully controlling the alloy composition and microstructure, engineers can optimize the brazing process to create stronger, more reliable joints for demanding aerospace applications. Further research into the effects of specific alloying elements on intermetallic phase formation and boundary strength will pave the way for even more advanced titanium brazing techniques.