The Future of Precision: How Membrane Restrictors are Revolutionizing Hydrostatic Bearings
"Unlocking Efficiency and Accuracy in Mechanical Systems with Innovative Bearing Technology"
In the world of precision engineering, hydrostatic guides and bearings stand as essential components for ensuring the smooth and accurate operation of mechanical systems. These bearings, which use a film of pressurized fluid to support loads, are critical in applications ranging from machine tools to automotive engines.
A key innovation in hydrostatic bearing technology is the use of membrane restrictors. These devices regulate the flow of fluid within the bearing, maintaining optimal pressure and stability. While the underlying principles may seem complex, understanding the basics of membrane restrictors can provide valuable insights into improving the efficiency and accuracy of various machines.
This article breaks down the complexities of membrane restrictors, presenting the core concepts in an accessible manner. Drawing from recent research, we will explore how these restrictors work, their benefits, and their potential for future advancements in mechanical engineering.
Understanding Membrane Restrictors and Hydrostatic Bearings: A Simplified Guide
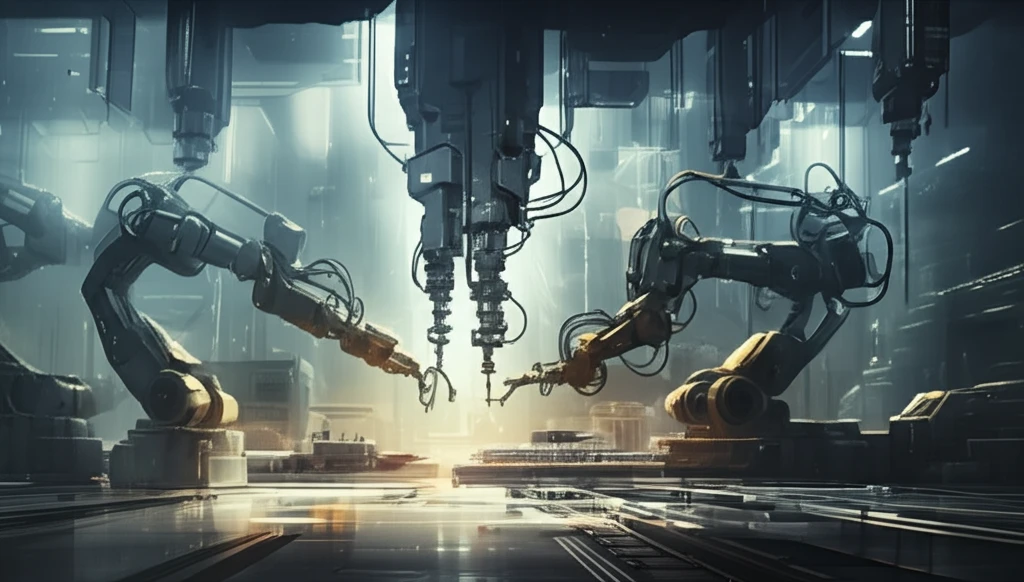
Hydrostatic bearings operate by using a thin layer of pressurized fluid, typically oil, to separate moving surfaces. This fluid film eliminates direct contact between parts, reducing friction and wear. Unlike traditional bearings that rely on rolling elements, hydrostatic bearings offer superior accuracy and load-carrying capacity, especially in high-precision applications.
- Reduced Friction: By eliminating direct contact between moving parts, hydrostatic bearings minimize friction, leading to smoother operation and reduced energy consumption.
- High Accuracy: The fluid film provides consistent and even support, resulting in exceptional precision and accuracy in mechanical systems.
- Load Capacity: Hydrostatic bearings can support heavy loads due to the pressurized fluid distributing the force evenly across the bearing surface.
- Damping Capability: The fluid film also acts as a damper, absorbing vibrations and reducing noise.
The Path Forward: Optimizing Performance and Expanding Applications
As technology advances, the potential of membrane restrictors in hydrostatic bearings continues to grow. Future research will likely focus on developing even more sophisticated designs and control strategies. These advancements will enable engineers to create mechanical systems that are more efficient, accurate, and reliable than ever before, paving the way for innovations in manufacturing, robotics, and beyond.