The Future of Machining: How Advances in Chip Formation are Reshaping Manufacturing
"Unlock precision and efficiency in manufacturing with the latest breakthroughs in chip formation technology. Discover how these advancements are transforming industries and creating new possibilities."
In the ever-evolving landscape of manufacturing, the quest for precision and efficiency is relentless. One critical area of focus is chip formation—the process by which material is removed from a workpiece during machining. Recent advancements in this field are not only optimizing traditional methods but also paving the way for innovative techniques that promise to reshape entire industries.
Traditionally, chip formation has been viewed through the lens of free cutting with a single shear plane. However, this approach often falls short in capturing the complexities of modern machining, particularly in constrained cutting scenarios. Constrained cutting, where the cutting region is influenced by multiple edges or complex tool geometries, demands a more sophisticated understanding and control of chip formation.
This article delves into the groundbreaking research and methodologies that are revolutionizing chip formation in constrained cutting. We'll explore the latest approaches, analytical descriptions, and experimental methods that are enabling manufacturers to achieve unprecedented levels of precision, efficiency, and material utilization. Whether you're a seasoned engineer, a manufacturing enthusiast, or simply curious about the future of technology, this exploration will provide valuable insights into the transformative power of chip formation.
Understanding Constrained Cutting: The Key to Manufacturing Efficiency
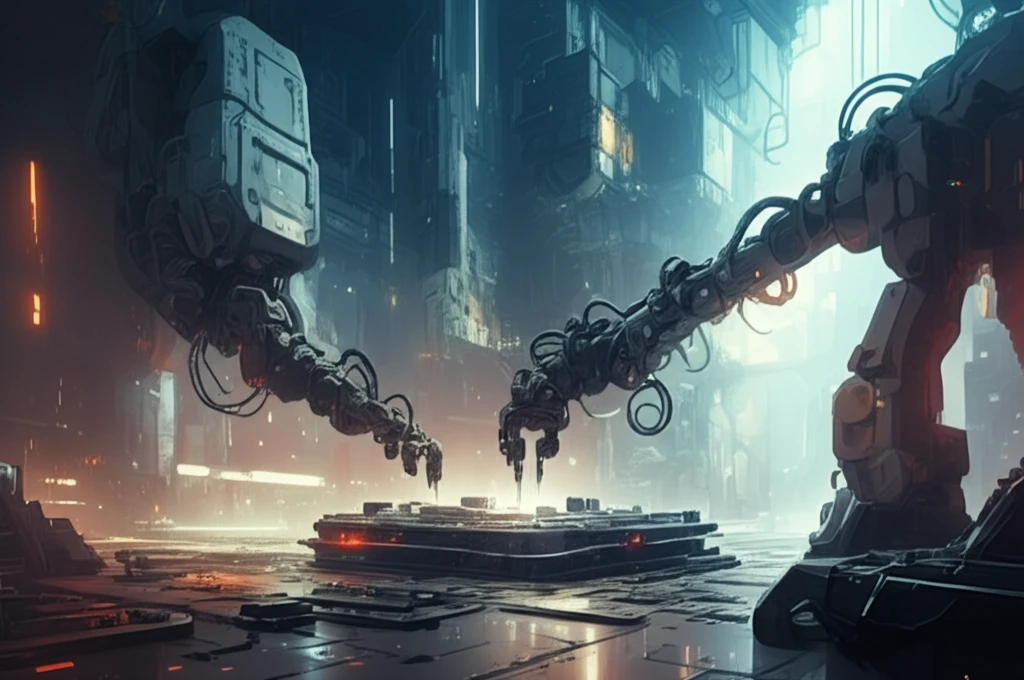
Constrained cutting represents a significant departure from traditional free cutting methods. In constrained cutting, the interaction between the cutting tool and the workpiece is influenced by multiple factors, such as tool geometry, cutting speed, and material properties. This complexity requires a more nuanced approach to understanding and controlling chip formation.
- Advanced Analytical Models: Researchers are developing sophisticated analytical models to describe the conditional shear surface in constrained cutting. These models take into account factors such as cutting edge geometry, shear angle, and material properties to provide a comprehensive understanding of chip formation.
- Experimental Validation: To validate these models, experimental methods are employed to observe and measure chip formation under various cutting conditions. High-speed imaging, force measurements, and material analysis techniques are used to refine the models and ensure their accuracy.
- Application-Specific Optimization: By combining analytical models with experimental data, manufacturers can optimize cutting parameters for specific applications. This leads to improved surface finish, reduced tool wear, and increased material removal rates.
The Horizon of Chip Formation Technology
As research and development efforts continue to push the boundaries of chip formation technology, the future of machining looks brighter than ever. The ability to precisely control material removal at the micro and nano scales opens up new possibilities for creating complex geometries, enhancing surface properties, and tailoring materials to specific applications. From aerospace to biomedical engineering, the impact of these advancements will be felt across a wide range of industries.