The Flow Shop Fix: How Optimizing Assembly Lines Can Save Your Business
"Tired of production bottlenecks? Discover how flow shop scheduling with assembly operations can revolutionize your efficiency and boost your bottom line with the latest trends."
In today's fast-paced business environment, efficiency is the name of the game. Every company, from small startups to large corporations, is constantly seeking ways to optimize their processes and gain a competitive edge. One area where significant improvements can often be made is in production, specifically in assembly line operations. The concept of flow shop scheduling with assembly operations has emerged as a powerful approach to tackling production bottlenecks and maximizing output.
Flow shop scheduling involves arranging production processes in a linear sequence, where each job follows the same path from start to finish. When assembly operations are integrated into this model, it creates a dynamic system where components are manufactured and then assembled into final products. This approach is particularly useful for businesses that deal with complex products requiring multiple stages of assembly.
The benefits of mastering flow shop scheduling with assembly operations are substantial. By implementing efficient scheduling strategies, companies can reduce production times, minimize work-in-progress inventory, and improve on-time delivery performance. This not only leads to increased customer satisfaction but also translates into significant cost savings and revenue growth. Ready to transform your production line? Let's dive into the world of flow shop scheduling and explore how it can revolutionize your business.
Understanding Flow Shop Scheduling with Assembly Operations
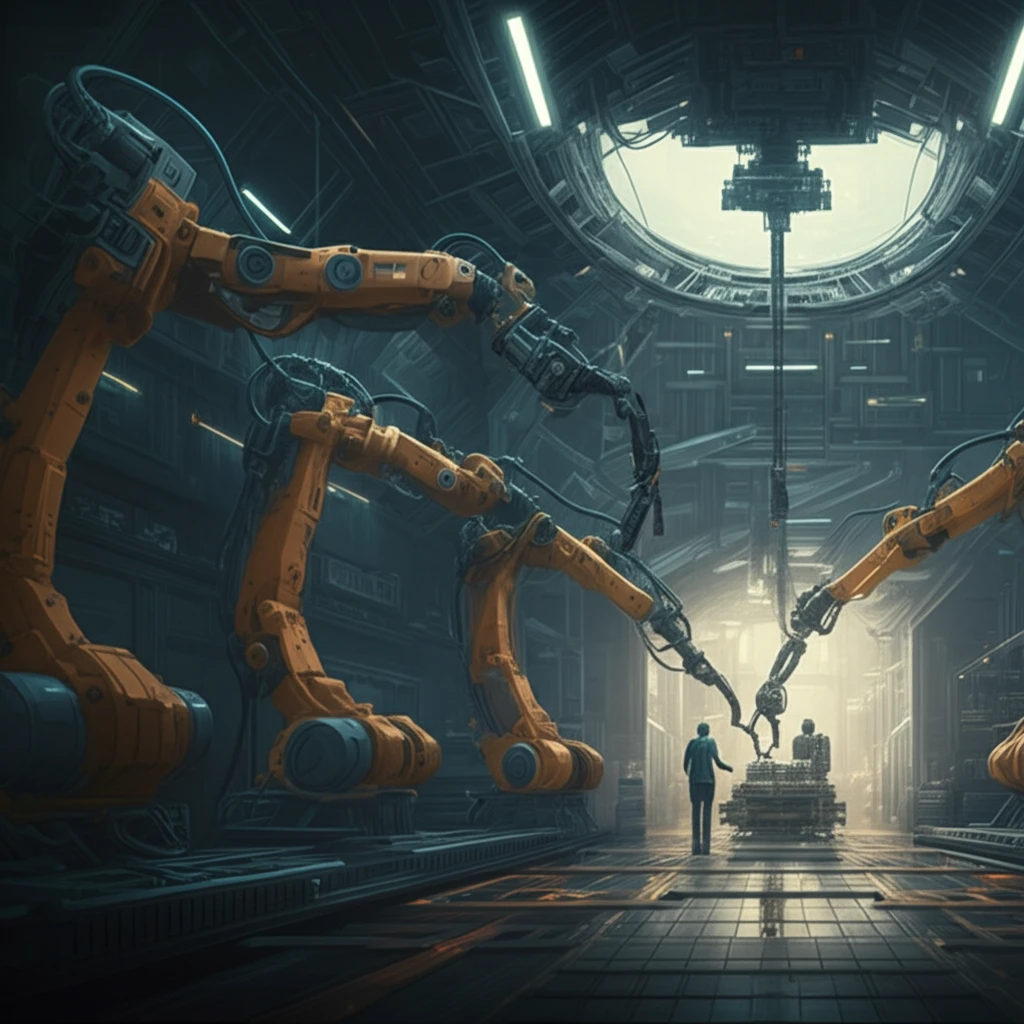
At its core, flow shop scheduling is about creating a smooth and efficient workflow. Imagine a series of workstations arranged in a line, where each station performs a specific task on every product that passes through. This linear arrangement ensures that all jobs follow the same sequence of operations, making it easier to manage and optimize the production process.
- Fabrication Stage: This involves manufacturing the individual components needed for the final product. This stage may involve machining, molding, or other processes to create the necessary parts.
- Assembly Stage: This is where the components come together to form the final product. Assembly can range from simple tasks to complex procedures requiring specialized equipment and skilled labor.
- Hierarchical Assembly Structure: Many products have a hierarchical structure, meaning that sub-assemblies are created before being integrated into the final product. Managing this hierarchy is crucial for efficient scheduling.
Future Directions and Untapped Opportunities
While flow shop scheduling with assembly operations has been extensively studied, there are still many avenues for future research and innovation. Areas such as incorporating uncertain processing times, exploring different assembly structures, and addressing real-world constraints like limited resources and machine breakdowns offer exciting opportunities to further enhance the effectiveness of these scheduling strategies. By embracing these challenges, businesses can unlock even greater levels of efficiency and competitiveness.