Stronger Joints: How Advanced Welding Boosts Car Safety and Efficiency
"Explore how microstructure-based modeling enhances friction stir spot welding (FSSW) for safer, lighter vehicles."
In today's automotive industry, the quest for lighter, safer, and more fuel-efficient vehicles has led to significant advancements in welding technologies. Among these, friction stir welding (FSW) and its variant, friction stir spot welding (FSSW), have emerged as game-changers, especially for joining lightweight materials like aluminum and magnesium alloys.
Friction stir spot welding is particularly innovative. It creates strong bonds without melting the metal, which avoids common welding defects. By using mechanical friction and softening metals, it is possible to achieve a bond that is locally metallurgically sound. As the automotive industry increasingly adopts lightweight materials to meet global energy conservation and emission reduction goals, FSSW offers superior weldability and joint integrity compared to traditional methods like resistance spot welding, riveting, and threaded connections.
The impact of improved welding on vehicle performance is substantial. With thousands of joints in a single vehicle, enhancing each one contributes significantly to overall rigidity, collision resistance, and other critical safety parameters. A recent study published in the Journal of Manufacturing Processes explores an innovative approach to analyzing and optimizing FSSW joints using microstructure-based modeling and thermo-mechanical coupling simulation. This method aims to predict and enhance the mechanical properties of welded joints with greater accuracy, ultimately leading to safer and more efficient vehicles.
Understanding Friction Stir Spot Welding: The Science Behind Stronger Joints
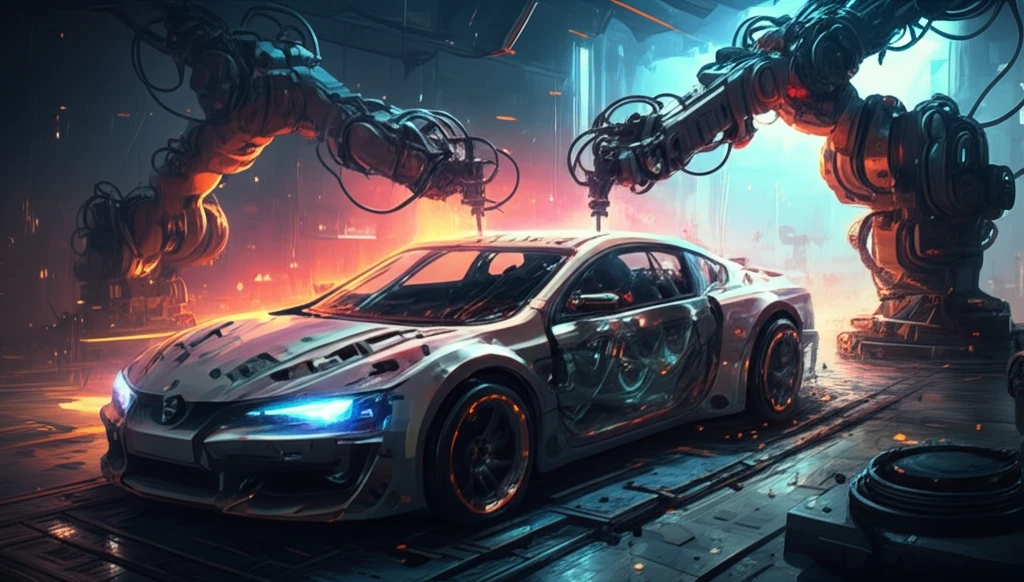
Friction stir spot welding is a solid-state joining process that relies on frictional heat and plastic flow to create a weld. Unlike traditional welding methods that melt the base metals, FSSW uses a rotating tool to generate heat and pressure, causing the materials to soften and intermix at the joint. Here’s a breakdown of the key elements:
- Plunging: A rotating tool is inserted into the overlapping sheets of metal to a specific depth. Initially, the tool pin acts alone before the shoulder makes contact with the top surface of the workpiece.
- Dwelling: The tool remains in place for a set time, during which friction generates stable heat at the contact interface between the tool and the materials being joined.
- Retracting: The tool is withdrawn, leaving behind a solid-state weld.
The Future of Automotive Manufacturing: Lighter, Safer, and More Efficient Vehicles
As the automotive industry continues to evolve, advanced welding techniques like FSSW will play an increasingly crucial role in creating vehicles that meet the demands of a rapidly changing world. By embracing innovative approaches to design, materials, and manufacturing, we can pave the way for a future of driving that is safer, more sustainable, and more enjoyable for everyone.