Spot Welding Secrets: How to Join Steel and Aluminum Like a Pro
"Unlock the secrets of joining dissimilar metals! Discover how advanced resistance spot welding techniques can revolutionize manufacturing, reduce vehicle weight, and boost fuel efficiency."
In today's automotive industry, the quest for lighter vehicles is paramount. Reducing vehicle weight translates directly into improved fuel efficiency and lower emissions, a win-win for both consumers and the environment. This drive has led to increased interest in using both high-strength steel and aluminum alloys in vehicle construction.
The challenge? Joining these dissimilar materials efficiently and reliably. While various welding methods exist, resistance spot welding (RSW) stands out due to its cost-effectiveness, high production speed, and automation potential. Recent research has focused on optimizing RSW techniques for joining steel and aluminum, particularly in triple-sheet configurations.
This article delves into a groundbreaking study on the resistance spot welding of DP 600 steel, A5052 aluminum alloy, and DP 600 steel in a triple-sheet arrangement. We'll explore the process, the resulting microstructures, and the mechanical properties of these joints, uncovering the secrets to creating robust and lightweight vehicle components.
What's the Secret? Mastering Resistance Spot Welding for Dissimilar Metals
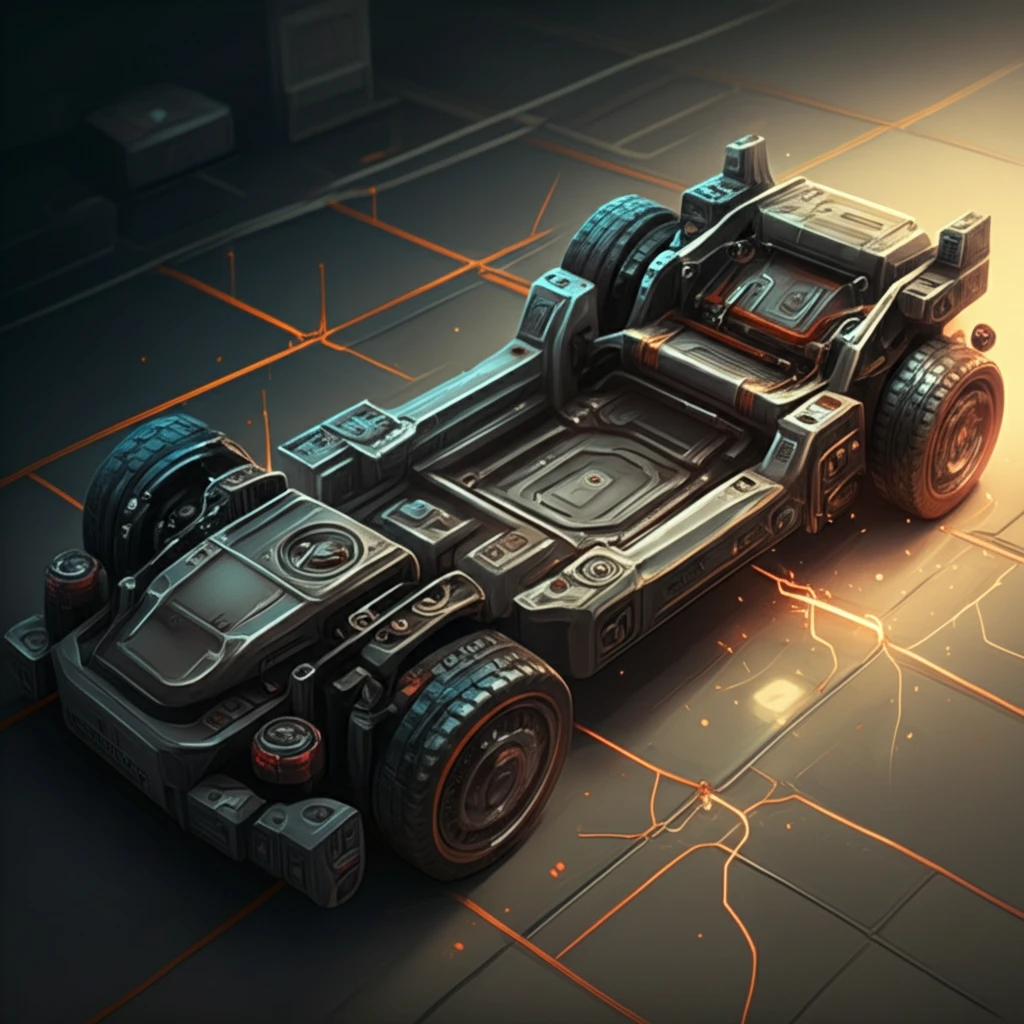
The core of the study involved joining DP 600 steel, A5052 aluminum alloy, and DP 600 steel sheets using resistance spot welding. The researchers meticulously examined the fusion zone's microstructure, revealing a composition of lath martensite in the DP 600 steel and column crystals in the A5052 aluminum alloy. These grains tended to coarsen as the distance from the base metals increased.
- Shorter Welding Times: With shorter welding times, the needle-like Fe4Al13 phase near the A5052 aluminum alloy tended to be longer.
- Longer Welding Times: As the welding time increased, this phase shortened, while the Fe2Al5 IMC layer near the DP 600 steel widened.
- Optimal Welding Time: The study found that a welding time of 14 cycles resulted in the highest tensile-shear load for the DP 600/A5052/DP 600 joints, achieving an impressive 10.796 kN.
What Does It All Mean? The Future of Lightweight Vehicle Design
This research provides valuable insights into optimizing resistance spot welding for joining dissimilar metals in automotive applications. By carefully controlling welding parameters, manufacturers can create strong, reliable joints between steel and aluminum, paving the way for lighter, more fuel-efficient, and sustainable vehicles. While the brittle nature of IMCs remains a challenge, ongoing research into alternative welding techniques and materials promises to further enhance the performance and durability of dissimilar metal joints.